51. Системы электронного управления двигателями фирм «Катерпиллар», «МАН-Дизель», «Вяртсиля-Зульцер».
Применение электронного управления двигателями открывает новые возможности в совершенствовании процессов сгорания, тем самым повысить экологичность, экономичность и надёжность.
Сайт: | СДО "ФАРВАТЕР" |
Курс: | Обеспечение технической эксплуатации главных судовых энергетических установок III курс 1 семестр |
Книга: | 51. Системы электронного управления двигателями фирм «Катерпиллар», «МАН-Дизель», «Вяртсиля-Зульцер». |
Напечатано:: | Гость |
Дата: | Понедельник, 25 августа 2025, 15:34 |
Оглавление
Применение электронного
управления двигателями открывает новые возможности в совершенствовании
процессов сгорания, тем самым повысить экологичность, экономичность и
надёжность.
Первой, освоившей промышленный выпуск дизелей с электронным управлением, была фирма «Катерпиллар». В области судового двигателестроения первые шаги сделали фирмы MAN&BW (Intelligent engine) — 2-х тактные, и Вяртсиля: 4-х тактные двигатели и двигатели 2-х тактные — Зульцер (RTA-flex).
Устанавливаемый на двигатели микропроцессор выполняет функции:
• Электронного регулятора скорости, поддерживающего заданный скоростной и нагрузочный режим;
• Управления подачей топлива в соответствии с заданным режимом;
•
Фиксирования и мониторинга
основных параметров двигателя и
обслуживающих его систем;
• Осуществления АПС и З;
•
![]() |
|
Фиксирования в памяти процессора всех нарушений в работе двигателя и вне зависимости от срока давности выдачи их на экран, подключаемого к микропроцессору компьютера.
Реализация перечисленных функций существенно повышает уровень контроля и технической эксплуатации, продлевает ресурс двигателя. Принципиальная схема системы электронного управления представлена на Рис. 1 Учитывая жесткие требования по безопасности мореплавания, в систему включено дублирование электронных модулей, рукояток управления, датчиков оборотов и положения ВМТ (см. Рис. 1). Для исключения внезапного отказа основной электронный блок каждые 50с. посылает сигналы резервному блоку и, по получении обратного сигнала, продолжает функционировать по своему назначению. В случае нарушений в его работе сигналы от основного блока прекращаются, и тогда включается в работу резервный. Равным образом функционируют и зарезервированные датчики оборотов.
Оптимизация моментов подачи
топлива решается программой, заложенной в электронный блок,
и получающей сигналы от датчиков числа
оборотов, нагрузки (положения топливной рукоятки), давления наддува, температуры топлива.
В соответствии с величинами перечисленных сигналов
программа вычисляет оптимальные для данного режима значения начала и конца подачи топлива и подает ток на соленоиды насос-форсунок, перемещающие управляющие клапаны в положения — подача или отсечка (см. рис. 2).
Когда управляющий клапан (Рис. 3) находится в нижнем положении, он сообщает полость под плунжером через канал 2 с отсечкой (канал 1) и даже при движении плунжера вниз (ход нагнетания), давление под ним не будет расти. Последнее начнет подниматься лишь после того, как включение соленоида потянет клапан вверх и посадит его на седло, полость под плунжером будет разобщена с отсечкой. Когда давление под плунжером а, следовательно, и под иглой достигнет 350 бар, начнется впрыск топлива в цилиндр. Конец подачи происходит в момент прекращения подачи тока на соленоид, клапан под действием пружины опускается вниз и сообщает полость нагнетания с отсечкой.
С помощью подключаемого к микропроцессору компьютера и заложенной в него программы по известным кодам осуществляется диагностика двигателя. В качестве компьютера обычно используется Notebook, для него разработана программа, позволяющая при подключении не только собирать информацию о работе двигателя за предыдущий период его эксплуатации, но диагностировать его техническое состояние, включая и диагностику всей электроники. Для тестирования насос-форсунок программа в автоматическом режиме поочередно отключает цилиндры и по увеличению подачи топлива на работающих цилиндрах определяется какую часть нагрузки он брал на себя. Очень важным достижением фирмы является тот факт, что в новой модели двигателя серии С-9 с гидроприводом насос-форсунок на компьютер выдается усредненная для данного режима величина цикловой подачи топлива каждой форсунки.
Поскольку давление впрыска в этих форсунках находится в прямой зависимости от давления гидромасла, то фиксирование микропроцессором этих давлений и фаз подачи на коротком отрезке времени позволяет подсчитать давления Рвпр и продолжительность впрыска (tвnp = ϕвпр / 6 n ), и по ним и известной величине эффективного сечения сопловых отверстий ( µf с) определить среднюю величину цикловой подачи.
Сопоставление подач по всем
цилиндрам позволяет оценить работу каждой насос-форсунки.
Начало работ по
системам электронного управления двухтактных малооборотных двигателей
относится к 1991 году, в 2003 году были построены и установлены на танкерах
первые двигатели 7S-50МЕ-С и 6S70ME-C с электронным управлением.
Фирмой было прежде всего разработано и заложено в основу электронной системы
программное обеспечение.
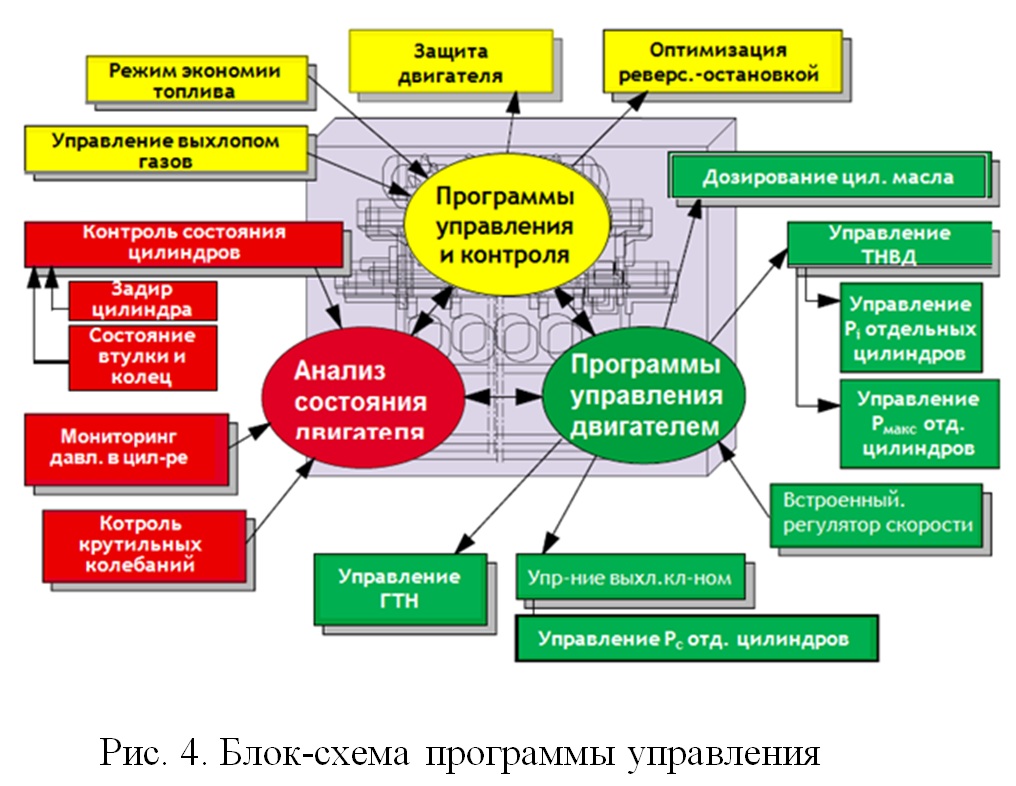
На Рис. 4 представлена блок-схема программ, включающих решение задач по анализу состояния двигателя и управлением топливоподачей, движением выхлопных клапанов, смазкой цилиндров и турбонаддувом.
Конфигурация системы управления, приведенная на Рис.5 включает панель управления на мостике, главную панель управления в посту управления, два микропроцессора (основной А и резервный В), в которые заложены программы управления, панель местного управления также с двумя электронными блоками А и В и модулями на каждом цилиндре.
Перевод мощных двигателей на
электронное управление потребовал не только поиска и разработки программ управления,
высоконадежных средств электроники, но и радикального решения по замене мощных
механических
приводов. Достаточно сказать, что привод топливного насоса в стандартном варианте испытывает весьма большие нагрузки, если учесть, что в мощной машине в цилиндр за цикл подается около 200 г. топлива, сжатого до 80-90 МПа. Высокие нагрузки приходятся и на привод выхлопных клапанов. Поэтому единственно верным решением было применить в качестве силовых передач гидропривод (МАН Дизель и Турбо), либо аккумуляторную систему топливоподачи, как это сделала фирма Зульцер. Схема системы топливоподачи с гидроприводом представлена на Рис.6. В число основных компонентов системы входят:
Самоочищающийся 10 микронный фильтр тонкой очистки маcла, необходимость в котором определяется более высокими требованиями к маслу, используемому в гидроприводе.
• Гидронасосы, использующие масло из общей системы смазки двигателя и поднимающие его давление до 17,5 МПа (электроприводные и применяемые при пуске двигателя) и до 25 МПа с приводом от двигателя, берущие на себя снабжение гидросистемы маслом во время его работы. Масло направляется в аккумулятор (Рис. 6), давление в котором поддерживается путем изменения производительности гидронасосов, находящейся под управлением электронных блоков. Из аккумулятора масло направляется к установленным на каждом рабочем цилиндре гидроцилиндрам-усилителям привода ТНВД и выхлопного клапана, включающим блок распределения с гидравлическими аккумуляторами и электронно управляемыми, пропорциональными, быстродействующими клапанами положения (NC) см. Рис.7. В задачу последних входит управление фазами и давлениями топливоподачи, фазами движения выхлопного клапана.
Электронное управление и гидропривод топливного насоса.
Топливный насос высокого давления
в сравнении с традиционными конструкциями механически значительно
проще. В нем отсутствуют механический привод плунжера, (заменен на гидропривод), механизм управления фазами подачи топлива, механизм VIT.
Плунжер представляет собой гладкий поршень без косых кромок, что существенно упрощает технологию его изготовления и повышает ресурс. Масло из аккумулятора через управляющий клапан, активизация которого осуществляется электронным блоком, попадает в полость над гидропоршнем. Воспринимаемое им усилие, будучи усиленным в 4,47 раза (отношение площадей Fгп / Fпл = 4,47), передается поршню-плунжеру топливного насоса, осуществляющему сжатие топлива до заданных процессором давлений в 50 - 100МПа и подачу его к форсункам.
Как уже отмечалось,
моменты поступления масла в цилиндр гидроусилителя, а,
следовательно, фазы и количественная характеристика подачи, задаются
микропроцессором, в свою очередь воздействующим на управляющий клапан. В
микропроцессор заложены программы, позволяющие изменять давление масла по ходу
процесса впрыска, тем самым менять характер кривой давлений впрыска и подбирать
необходимый для данного режима закон подачи топлива. Возможные варианты
приведены на Рис. 9. Рис. 10 иллюстрирует влияние характера
впрыска на развитие давлений в рабочем цилиндре. Здесь мы видим впрыск с резким ростом давлений в начальной стадии и последующим спадом давления и, сопровождаемым уменьшением скорости впрыска топлива (поз.А). Такой вариант, равно как и последующий (поз.В), приведет к резкому росту тепловыделения в цилиндре в начальной стадии сгорания и большим Рмакс. В итоге - будет достигнута высокая экономичность, но и большие тепловые и механические нагрузки на ЦПГ. Более мягкая организация подачи в ее начале и резкое окончание в конце (поз. С) позволяет уменьшить нагрузки, но в ущерб экономичности двигателя. В то же время, улучшается распыливание топлива в конце подачи, а, следовательно, достигается меньшее догорание на линии расширения. Мягкое сгорание в начальной стадии и меньшие температуры рабочего цикла достигаются при двухфазном впрыске (поз.D). К этому варианту прибегают, когда стоит задача уменьшения содержания в выхлопных газах NOx.
Электронное управление и гидропривод выхлопного клапана
Система привода включает
цилиндр-актюатор, заполняемый маслом высокого давления из аккумулятора через
управляющий клапан, активируемый электрическим сигналом, поступающим из
электронного блока (Рис. 7).
Перечисленные элементы практически выполняют функции традиционной системы механического привода клапана, состоявшей из распределительного вала с кулачком, толкателя и коромысла. В рассматриваемой системе гидропривода управляющий клапан по получении эл. сигнала от электронного блока в необходимый момент открывает доступ гидромасла высокого давления к поршню сервопривода (см. Рис. 11), который, двигаясь вниз, открывает клапан. Закрытие клапана происходит после перемещения управляющего клапана в положение, при котором полость актюатора разгружается от давления масла. Соответственно полость гидроусилителя также разгружается и воздушная пружина поднимает клапан в положение “закрыто”. В конструкции сервоприводов предусмотрены демпферы, смягчающие удары при открытии и закрытии клапана. Контроль за перемещениями клапана осуществляет установленный на корпусе датчик, реагирующий на изменение расстояния между ним и напрессованным на шток клапана измерительным конусом.
Важно отметить, что предоставленная электроникой возможность изменения фаз открытия и закрытия клапана позволяет их оптимизировать в соответствии с режимом работы двигателя.
Электронное управление лубрикатором.
Использование в системе
управления двигателем микропроцессоров позволило решить давно назревшую
проблему организации смазки цилиндров. В традиционной системе, где используется механический привод лубрикаторов,
ряд фирм для уменьшения подачи масла на смазку цилиндров при снижении
нагрузочного режима связывали механизм подачи с положением рейки топливных
насосов. Но, к сожалению, не могли достигнуть синхронизации подачи с движением
поршня рабочего цилиндра, а это приводило к тому, что часть поступающего из
штуцеров масла попадала в цилиндр над поршнем, и при его движении вверх
поршневыми кольцами перемещалось в направлении камеры сгорания, где выгорало.
Часть масла выходила из штуцеров цилиндра под поршень и при его движении вниз
кольцами забрасывалось в продувочные и выхлопные окна. Идеальной считается
подача в момент, когда масло выходит из штуцера в промежуток между первым и
вторым поршневыми кольцами. Тогда масло хорошо разносится по поверхности
цилиндра и ранее отмеченные потери исключаются. В современной системе эта задача
успешно решается и экономия в расходе цилиндрового масла в двигателях ME составляет свыше 0,3 г/кВт·час. Концепция новой
системы смазки цилиндров с электронным управлением представлена на Рис. 12.
Масло из цистерны цилиндрового масла поступает в насосную станцию, где его
давление поднимается до 4,5 МПа и направляется в индивидуальные для каждого
цилиндра аккумуляторы и далее в лубрикаторы. В станции находятся два рабочих
насоса и один, автоматически включаемый в режиме stand-by. Количество лубрикаторов (1 или 2) на каждом цилиндре
зависит от размеров цилиндра (количества штуцеров).
Лубрикатор
(см. Рис. 13) снабжен поршнем гидроусилителя, подача масла на который
осуществляется через быстродействующий двухпозиционный клапан, управляемый
микропроцессором. Поршень приводит в движение размещенные по окружности плунжеры
насосов высокого давления, обеспечивающие подачу одинаковых количеств масла по
всем точкам смазки и, практически, в один момент времени. Количество плунжеров
соответствует числу точек смазки. Лубрикатор подает масло через каждые в 4-5
или более оборотов коленчатого вала в зависимости от
требуемой величины подачи, выраженной в г\кВт·час. Увеличение подачи
достигается увеличением частоты подач, уменьшение - наоборот. Время впрыска
(момент подачи) задается микропроцессором с большой точностью с тем, чтобы
поступление масла в цилиндр происходило в период, когда поршень своим
комплектом колец находится в плоскости штуцера. Продолжительность подачи
укладывается в ~0,1°п.к.в. Величина создаваемого плунжерами давления в
нормальных условиях составляет 4,5 МПа, при закоксовывании отверстий может
существенно увеличиваться, что обеспечивает гарантированную подачу.
Система электронного управления фирмы «Вяртсиля-Зульцер»
В двигателе Зульцер с электронной системой управления, в его новой модификации RT-flex, взамен распределительных валов с их приводом, традиционных ТНВД и гидроприводов выхлопных клапанов была применена аккумуляторная система впрыска топлива и управления выхлопными клапанами, что существенно упростило его конструкцию. В двигателе с электронным управлением привод гидронасосов сервомеханизмов размещен непосредственно рядом с коленчатым валом. На уровне крышек цилиндров находятся аккумуляторы давления масла и топлива. Там же располагаются сервоприводы топливных насосов высокого давления и выхлопных клапанов.
Задача внедрения электронного управления заключалась в дальнейшей оптимизации рабочего процесса двигателей RTA, сокращении вредных выбросов с выхлопными газами и снижении удельного расхода топлива. Электроника позволила повысить гибкость в управлении углом опережения впрыска топлива, законом подачи топлива и их оптимизации на всем диапазоне рабочих режимов.
Также было реализовано управление фазами закрытия выхлопного клапана (VEC -Variable Exhaust valve Closing - Рис. 14). Более раннее закрытие клапана на режимах малых нагрузок позволило повысить действительную степень сжатия в цилиндрах и, тем самым, создать лучшие условия для сгорания топлива и избежать дымления.
Одним из важнейших изменений в двигателе явилось внедрение аккумуляторной системы топливоподачи, состоящей из ТНВД, создающего давление в 1000 бар, аккумулятора топлива и электронно-управляемых клапанов, распределяющих топливо по форсункам (Рис. 15).
Аккумулятор представляет собой
толстостенную трубу, идущую по всей длине двигателя на уровне крышек
цилиндров, в которой
размещается необходимый для впрыска объем топлива, находящегося под давлением 1000 бар и устройство демпфирования возникающих в ней волн давления. Подача и сжатие топлива до отмеченного давления осуществляется в обычных ТНВД, плунжеры которых приводятся в действие многокулачковым валиком.
Из аккумулятора топливо поступает к стандартным форсункам, открытие и закрытие игл которых происходит обычным путем под давлением топлива, попадающего к каждой из них от управляющего клапана. Последний устанавливает момент открытия иглы, угол опережения, количество впрыскиваемого топлива и форму кривой подачи топлива (закон подачи).
Три форсунки в каждом цилиндре управляются независимо одна от другой - программируются на работу каждая по отдельности или по мере необходимости в унисон (см Рис. 15, 16, 17, 18). Управление клапаном осуществляется посредством микропроцессорной системы электронного управления WECS 9500, имеющей модульное исполнение с отдельным микропроцессором для каждого цилиндра. На эту же системы возложены функции контроля за всем двигателем.
Ключевыми чертами аккумуляторной системы топливоподачи фирмы Зульцер являются:
♦ отмеривание величины объемной подачи топлива с высокой точностью, что обеспечивает более равномерную работу двигателя и низкий уровень вибраций, вызываемых неуравновешенными силами и моментами;
♦ возможность менять форму кривой подачи (закон подачи) и величину давлений впрыска;
♦ идеально соответствует использованию тяжелых топлив с различными характеристиками;
♦ обеспечивает устойчивую работу на самых малых оборотах (10-12 1/мин)
♦ полное сгорание топлива без видимых следов дыма на выхлопе. Возможность менять закон подачи топлива и, тем самым, снижать температуры, цикла позволили существенно снизить содержание окислов азота в выхлопных газах. (см. Рис. 17).
Как уже отмечалось, электронная система включает также управление гидроприводом выхлопного клапана и системой пуска двигателя (Рис. 20).
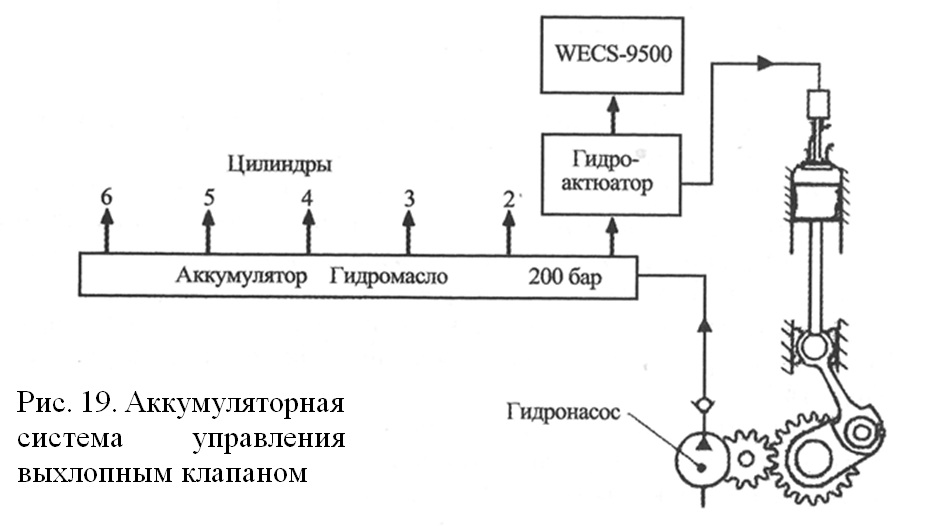
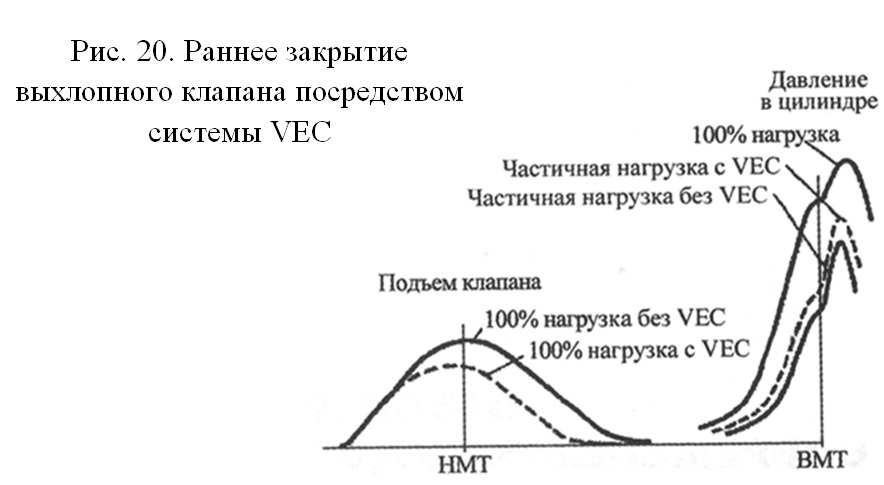
Открытие и закрытие выхлопных клапанов осуществляется аналогично тому, как это реализовано в двигателях RTA, но гидротолкатель приводится в действие гидромаслом, предварительно сжатым до 200 бар и находящимся в аккумуляторе. Сжимается масло специальным насосом, расположенным в одном блоке с ТНВД.
Электронный управляемый блок гидроусилителя клапана позволяет для каждого клапана в широких пределах менять фазы его открытия и закрытия. Как уже отмечалось, фирма в целях увеличения давления сжатия в цилиндрах прибегает к сокращению продолжительности открытия клапана. Благодаря этому, как видно из рис. 14.19, давление в цилиндре на частичных нагрузках существенно увеличивается, и это положительно отражается на полноте сгорания топлива.
Литература:
Возницкий И. В. Судовые двигатели внутреннего сгорания. Том 1. / И.В.Возницкий, А.С.Пунда – М.:МОРКНИГА, 2010.- 260 с. Стр. 190-205
MAN B&W G40ME-C9.5-TII Project Guide Electronically Controlled Two_stroke Engines