ВВЕДЕНИЕ
Электронное учебное пособие по дисциплине «Механика. Модуль прикладная механика» направлено на формирование универсальных общепрофессиональных компетенций в соответствии с федеральным государственным образовательным стандартом по уровню специалитета:
(ОК-2) пониманием сущности и социальной значимости своей будущей профессии, проявлением к ней устойчивого интереса, высокой мотивацией к работе;
(ОК-3 )владением математической и естественнонаучной культурой как частью профессиональной и общечеловеческой культуры;
(ОК-13) способностью собирать и интерпретировать с использованием современных информационных технологий данные, необходимые для формирования суждений по соответствующим социальным, научным и этическим проблемам;
(ПК-2) способностью и готовностью к самостоятельному обучению в новых условиях производственной деятельности с умением установления приоритетов для достижения цели в разумное время ;
(ПК-12) способностью и готовностью устанавливать причины отказов судового оборудования, определять и осуществлять мероприятия по их предотвращению;
(ПК-30) способностью участвовать в фундаментальных и прикладных исследованиях в области судов и судового оборудования;
(ПК-31) способностью создавать теоретические модели, позволяющие прогнозировать свойства объектов профессиональной деятельности;
(ПК-32) способностью разрабатывать планы, программы и методики проведения исследований объектов профессиональной деятельности;
(ПК-33) способностью выполнять информационный поиск и анализ информации по объектам исследований;
(ПК-34) способностью осуществлять и анализировать результаты исследований, разрабатывать предложения по их внедрению;
Электронное учебное пособие предназначено для обучающихся по направлению подготовки специальностей 26.05.07 «Эксплуатация судового электрооборудования и средств автоматики» и может быть использовано при изучении других дисциплин, направленных на формирование общепрофессиональных компетенций.
В электронном учебном пособии содержится вопросы, относящиеся к дисциплинам, которые традиционно входят в курс прикладной механики.
Цель электронного учебного пособия – сообщить студентам необходимые сведения из области кинематики и динамики механизмов, теоретических основ сопротивления материалов, а также методы расчёта на прочность, жёсткость деталей машин и механизмов, дать первые практические навыки расчётов и проектирования деталей и механизмов. Курс "Прикладная механика" является базой для изучения профилирующих дисциплин, требующих умения проводить расчёты на прочность, долговечность, а так же навыков конструирования.
Содержание данного электронного учебного пособия соответствует рабочей программе дисциплины и основано на материалах отечественных и зарубежных исследований.
Каждый раздел электронного учебного пособия включает контрольные вопросы и тестовые задания.
АННОТАЦИЯ ДИСЦИПЛИНЫ
МЕХАНИКА. МОДУЛЬ ПРИКЛАДНАЯ МЕХАНИКА
1. Место дисциплины в структуре образовательной программы.
Дисциплина изучается в 4 семестре II курса очной формы обучения и на III курсе заочной формы обучения.
Перечень базовых дисциплин и их разделов, необходимых для изучения курса "Прикладная механика":
1. Математика. Разделы: векторная алгебра, аналитическая геометрия, математический анализ.
2. Физика. Раздел: механика.
3. Инженерная графика. Разделы: ортогональные проекции, аксонометрия, техническое черчение.
4. Применение вычислительной техники в инженерных и экономических расчётах.
2. Планируемые результаты обучения по дисциплине
В результате освоения дисциплины обучающийся должен:
Знать:
- методы кинематического анализа и синтеза механизмов
- теоретическую, структурную и функциональную классификацию механизмов и машин
- иметь общие понятия о работе машин
-
Уметь:
- производить расчёты на прочность и жесткость наиболее распространенных деталей и узлов машин, механизмов приборов
- осуществлять практическое проведение анализа и синтеза механизмов
- рассчитывать по механической прочности типовые детали и узлы машин
Владеть:
- проведением проверочных расчётов на прочность и жёсткость
…
- первыми навыками по конструированию деталей и узлов механизмов, изучаемых в профессиональном блоке дисциплин.
3. Объем дисциплины по видам учебных занятий
- Объем дисциплины составляет 4 зачетные единицы; всего 164 часа, из которых по очной форме 108 часа составляет контактная работа обучающегося с преподавателем ( 64 часов – занятия лекционного типа, 22 часа – занятия практические 22 лабораторные работы; по очно-заочной
ГЛОССАРИЙ
В учебном пособии использована Международная система единиц
Systeme International d’Unites (в русской транскрипции СИ), которая является обязательной во всех областях науки и техники. Кратко напомним некоторые основные указания по применению СИ.
Наименование десятичных кратных и дольных единиц образуется присоединением приставок к наименованиям исходных единиц (табл.1).
Таблица 1
Приставка |
Сокращенное обозначение |
Множитель |
Тера |
Т |
1012 |
Гига |
Г |
109 |
Мега |
М |
106 |
Кило |
к |
103 |
Гекто |
г |
102 |
Дека |
да |
101 |
Деци |
д |
10-1 |
Санти |
с |
10-2 |
Милли |
м |
10-3 |
Микро |
мк |
10-6 |
Нано |
н |
10-9 |
Пико |
п |
10-12 |
Среди производных единиц с большой буквы пишутся те, которые образованы от фамилий ученых (Гц, Н, Па и т.д.).
Производные единицы связаны с основными, например:
1 Н = 1 кгм/с2; 1 Па=1 Н/м2; 1 Дж=1 Нм; 1 Вт=1 Дж/с.
В некоторых задачах по сопротивлению материалов в исходных данных используются внесистемные единицы, например обороты в минуту или сантиметр в четвертой степени и т.д. Это связано с тем, что на многих работающих сейчас электродвигателях, создающих динамическую нагрузку, обозначено именно количество оборотов в минуту, а в действующих сортаментах на прокат даны геометрические характеристики пока еще в единицах, производных от сантиметра. Переход от этих единиц к системным очевиден. Например:
1см4 = 1(10-2 м)4 = 1∙10-8 м4; 300 об/мин = 5 об/с = 5∙2π Гц.
Основные механические величины в единицах СИ и соотношения между ними и прежними единицами, подлежащими изъятию, приводятся в таблице 2.
Таблица 2
Наименование величины |
Единица |
Соотношение единиц |
|
Наименование |
Обозначение |
||
1 |
2 |
3 |
4 |
Сила, нагрузка, вес |
Ньютон |
Н |
1Н ≈ 0,1 кгс 1кН ≈ 0,1 тс |
Линейная нагрузка |
Ньютон на метр |
Н/м |
1Н/м ≈ 0,1 кгс/м 1кН/м ≈ 0,1 тс/м |
Механическое напряжение, модуль упругости |
Паскаль |
Па |
1Па ≈ 0,1 кгс/м2 1кПа ≈ 0,1 тс/м2 1мПа ≈ 10 кгс/см2 |
1 |
2 |
3 |
4 |
Момент силы, момент пары сил |
Ньютон-метр |
Нм |
1Нм ≈ 0,1 кгсм 1кНм ≈ 0,1 тсм |
Работа (энергия) |
Джоуль |
Дж |
1Дж ≈ 0,1 кгсм |
Мощность |
Ватт (джоуль в секунду) |
Вт |
1Вт≈0,1 кгсм/с 1 кВт ≈ 1,36 л.с. |
Основные обозначения
F, P |
- сосредоточенная сила |
N |
- продольная (нормальная) сила |
q |
- интенсивность распределенной нагрузки |
M |
- сосредоточенный момент |
Qx, Qy |
- поперечные силы, направленные вдоль осей x, y |
Mx, My |
- изгибающие моменты в поперечном сечении бруса относительно осей x, y |
T, Mкр |
- крутящий момент в поперечном сечении бруса |
Mu |
- изгибающий момент в поперечном сечении бруса |
Mэкв |
- эквивалентный момент |
b |
- ширина |
t |
- толщина |
e |
- эксцентриситет силы |
l |
– длина, пролет |
x |
- продольная ось стержня |
y, z |
- главные центральные оси инерции поперечного сечения стержня. |
σ |
- нормальное напряжение (общее обозначение) |
σx, σy |
– нормальные напряжения на площадках с нормалями параллельными осям x и y |
τ, τα, τxy |
- касательное напряжение (общее обозначение) |
σэкв |
- эквивалентное напряжение |
σсм |
- нормальное напряжение при смятии |
σy |
- предел текучести |
σut |
– предел прочности при растяжении |
σuc |
– предел прочности при сжатии |
σmax, σmin, σm, σa |
- нормальные напряжения цикла: максимальное, минимальное, среднее, амплитуда |
τa, τm |
- касательные напряжения цикла: амплитуда и среднее |
σm |
- средние напряжения |
σв |
- временное сопротивление (предел прочности) |
σ-1, τ-1 |
- пределы выносливости при симметричном цикле изгиба и кручения |
σ0, τ0 |
- пределы выносливости при отнулевом цикле изгиба и кручения |
R |
- расчетное сопротивление |
[σ], [τ] |
- допускаемые нормальное и касательное напряжения |
n |
- коэффициент запаса прочности |
[n] |
- допускаемый (требуемый) коэффициент запаса прочности |
∆l |
- абсолютное удлинение (абсолютная линейная деформация) |
Ε |
- относительное удлинение (относительная линейная деформация) |
εt |
- поперечная деформация |
γ |
- угол сдвига (относительная угловая деформация) |
E |
- модуль продольной упругости |
G |
- модуль упругости при сдвиге (модуль сдвига) |
Μ |
- коэффициент Пуассона |
W |
- работа внешних сил |
U |
- потенциальная энергия деформации |
φ |
- угол поворота поперечного сечения бруса при кручении |
f |
- прогиб балки |
θ |
- угол поворота поперечного сечения балки при изгибе |
A |
- площадь поперечного сечения бруса брутто |
Sx, Sy |
- статические моменты сечения относительно осей x, y |
Ix, Iy |
- осевые моменты инерции сечения относительно осей x, y |
Ip |
- полярный момент инерции сечения |
Ixy |
- центробежный момент инерции сечения |
ix, iy, iz |
- радиусы инерции сечения относительно соответствующих осей |
imin |
- наименьший радиус инерции сечения |
Wx, Wy, Wz |
– моменты сопротивления сечения относительно осей x–x, y–y и z–z соответственно |
Wp |
- полярный момент сопротивления сечения |
Kσ, Kτ |
- эффективные коэффициенты концентрации напряжений |
KF |
- коэффициент влияния шероховатости поверхности на предел выносливости |
KV |
- коэффициент влияния упрочнения поверхности на предел выносливости |
Kd |
- коэффициент влияния абсолютных размеров поперечного сечения на предел выносливости |
Pкр |
- критическая сила |
σcr, σкр |
- критическое напряжение |
λ |
- гибкость стержня |
1.ЗАДАЧИ И МЕТОДЫ СОПРОТИВЛЕНИЯ МАТЕРИАЛОВ
Сопротивление материалов это наука об инженерных методах расчета на прочность, жесткость и устойчивость элементов сооружений и деталей машин.
Элементы сооружений отличаются друг от друга формами, размерами, материалом, функциональным назначением, рядом специальных требований. При этом следует отметить, что все без исключения элементы как искусственного, так и естественного происхождения обладают такими свойствами, как прочность и жесткость, то есть способностью, не разрушаясь воспринимать различные нагрузки и сопротивляться изменению своих первоначальных форм и размеров, без чего не может нормально функционировать сооружение. Цель расчетов в сопротивлении материалов – создание прочных, устойчивых, обладающих достаточной жесткостью, долговечностью и вместе с тем экономичных элементов сооружений
Прочностные и жесткостные качества элементов сооружений зависят от многих факторов: материала, размеров, характера возникающих деформаций и др. Металлические конструкции обладают большей прочностью и жесткостью, чем аналогичные деревянные конструкции. Стержень из одного и того же материала, имеющий большие поперечные размеры, более прочный и жесткий, при этом его легче разрушить, изгибая, чем растягивая. Тонкий стержень при его сжатии разрушается в результате выпучивания в поперечном направлении, в то же время это явление отсутствует при продольном растяжении и для разрушения стержня требуется значительно большая нагрузка.
Подведя итог можно утверждать, что всякое реальное тело под воздействием сил меняет свою форму и размеры, т. е. деформируется. Деформации обуславливают появление внутри элемента сил сопротивления. Если внешние силы больше сил сопротивления, происходит разрушение элемента сооружения.
При возрастании нагрузки выше определенных значений в теле наряду с упругими будут возникать деформации не исчезающие после снятия нагрузки. Такие деформации называются остаточными. Возникновение остаточных деформаций, наравне с разрушением связано с нарушением нормальной работы конструкции и, как правило, недопустимо.
Способность конструкции воспринимать заданную нагрузку, не разрушаясь и без остаточных деформаций, называют прочностью.
Все элементы сооружения, из каких бы материалов они ни были изготовлены, под нагрузкой деформируются. Однако значительные деформации могут мешать нормальной эксплуатации сооружения.
Способность сооружений и ее частей под нагрузкой сохранять свои размеры и форму в установленных нормами пределах называется жесткостью.
Способность конструкции, и ее частей, сохранять под нагрузкой первоначальную форму упругого равновесия называется устойчивостью.
Методами сопротивления материалов выполняются расчеты, на основании которых определяются необходимые размеры деталей машин и конструкций инженерных сооружений. Любая конструкция должна обладать надежностью при эксплуатации и быть экономичной.
Надежность – свойство конструкции выполнять заданные функции, сохраняя свои эксплуатационные показатели в определенных нормативных пределах в течение требуемого промежутка времени.
Ресурс – допустимый срок службы изделия. Указывается в виде общего времени наработки или числа циклов нагружения конструкции.
Отказ – нарушение работоспособности конструкции.
Опираясь на вышесказанное, можно дать определение прочностной надежности.
Прочностной надежностью называется отсутствие отказов, связанных с разрушением или недопустимыми деформациями элементов конструкции.
Надежность конструкции обеспечивается, если она сохраняет прочность, жесткость и устойчивость при гарантированной долговечности. Ее экономичность в значительной мере определяется расходом материала, применением менее дефицитных конструкционных материалов, возможностью изготовления деталей по наиболее прогрессивным технологиям. Надежность и экономичность - противоречивые требования.
В сопротивлении материалов широко применяются методы теоретической механики и математического анализа, используются данные из разделов физики, изучающих свойства различных материалов, материаловедения и других наук. К тому же сопротивление материалов является наукой экспериментально-теоретической, так как она широко использует опытные данные и теоретические исследования.
В отличие от теоретической механики сопротивление материалов рассматривает задачи, в которых наиболее существенными являются свойства твердых деформируемых тел, а законами движения тела как жесткого целого здесь пренебрегают. В теоретической механике рассматривают равновесие абсолютно твердого (недеформированного) тела, при составлении уравнений равновесия допустимы замена системы сил статически эквивалентной системой, перенос сил вдоль линии их действия, замена ряда сил их равнодействующей. При решении задач сопротивления материалов, подобные замены или перенос сил недопустимы.
Методы сопротивления материалов базируются на упрощенных гипотезах, которые, с одной стороны, позволяют решать широкий круг инженерных задач, а с другой, получать приемлемые по точности результаты расчетов.
При этом главной задачей курса является формирование знаний для применения математического аппарата при решении прикладных задач, осмысления полученных численных результатов и поиска выбора наиболее оптимальных конструктивных решений. Конечная цель науки сопротивления материалов – определение размеров элементов сооружений, обеспечивающих его работоспособность при минимальном расходе материалов.
Сопротивление материалов является основой для изучения курса «Детали машин».
Зарождение науки о сопротивлении материалов относится к XVII в. и связано с работами знаменитого ученого того времени Галилео Галилея. Значительный вклад в ее развитие был сделан выдающимися учеными: Гуком, Бернулли, Сен-Венаном, Коши, Ламе, Эйлером и др. В России в конце XIX-начале XX века важные исследования в области сопротивления материалов провели русские ученые Д.И.Журавский,
Ф.С.Ясинский, И.Г.Бубнов, С.П.Тимошенко и др.
1.1.Реальный объект и расчетная схема.
В сопротивлении материалов, как и во всякой отрасли естествознания, исследование вопроса о прочности или жесткости реального объекта начинается с выбора расчетной схемы. Расчетная схема конструкции это его упрощенная схема, освобожденная от несущественных в данной задаче особенностей. К числу существенных факторов расчетной схемы относят: геометрию объекта, его форму и размеры;
физические характеристики материала; нагрузки, прикладываемые к объекту. Например, при расчете на прочность троса, поднимающего груз, можно не учитывать форму груза, сопротивление воздуха, изменение давления и температуры воздуха с высотой, силу тяжести троса и многие другие факторы, учет которых усложняет расчет троса, но практически не влияет на конечный результат. Трос, свитый из большого числа тонких проволочек, в данном примере можно рассматривать как однородный стержень круглого поперечного сечения, нагруженный растягивающей силой, сосредоточенной в месте крепления груза.
Такого рода упрощения задачи совершенно необходимы, так как решение с полным учетом всех свойств реального объекта является принципиально невозможным в силу их очевидной неисчерпаемости.
Основным упрощающим приемом в сопротивлении материалов является приведение геометрической формы тела к схемам бруса (стержня), оболочки или пластины. Как известно, любое тело в пространстве характеризуется тремя измерениями.
Под стержнями подразумеваются тела довольно разнообразной и вместе с тем специфической формы. Представим себе некоторую линию, вдоль которой движется плоская фигура так, что её центр тяжести находится на этой линии, а плоскость фигуры нормальна к ней (рис. 1.1). Если размеры фигуры b, h существенно меньше длины линии l, то описанное указанным образом тело называется стержнем (или брусом);
соответственно отмеченная плоская фигура называется поперечным сечением стержня, а отмеченная линия – осью стержня.
Рис. 1.1 Прямой брус (стержень) постоянного сечения
Если поперечное сечение при движении вдоль оси не изменяется, то тогда имеет место стержень постоянного сечения; в противном случае – стержень переменного сечения. Если ось стержня – прямая линия, то это прямой стержень. Если ось стержня – кривая линия, то его называют кривым стержнем. Используются также и другие названия, в частности, брус, работающий на растяжение, называют стержнем (рис.1.2, а), на изгиб, обычно называют балкой, а стержень, передающий вращательное движение, – валом.
Стержневые элементы, воспринимающие вертикальные сжимающие силы, называют стойками, а наклонные элементы - раскосами.
Конструкцию, состоящую из соединенных изгибаемых стержней, называют рамой. Если же благодаря шарнирному соединению стержней все они работают только на растяжение или сжатие (от нагрузки, приложенной в узлах), то конструкцию называют фермой.
Второй основной геометрической формой, рассматриваемой в сопротивлении материалов, является оболочка, под которой подразумевается тело, у которого одно из измерений (толщина) намного меньше, чем два других (рис.1.2, в). К оболочкам относятся различного рода резервуары, котлы, купола зданий, корпуса подводных лодок, обшивка фюзеляжа самолета и т.п.
Срединная поверхность – это геометрическое место точек, равноудаленных от внешней и внутренней поверхностей оболочки.
Оболочка, срединная поверхность которой представляет собой плоскость, называется пластиной (рис.1.2, б). Примером могут служить крыши и днища резервуаров, перекрытия зданий, различные диски и т.п.
Элемент конструкции, размеры которого во всех направлениях мало отличаются друг от друга, называется массивом. К ним относятся фундаменты сооружений, подпорные стенки и т.п.
Методы расчета пластин, оболочек и массивных тел при больших деформациях рассматриваются в курсе «Прикладная теория упругости». Способы расчета стержневых систем изучаются в курсе «Строительная механика».
Рис. 1.2. Основные
модели формы в моделях прочностной надежности:
а – стержень; б – пластина; в – оболочка
В заключение отметим, что если для одного объекта может быть предложено несколько расчетных схем, то, с другой стороны, одной расчетной схеме может быть поставлено в соответствие много различных реальных объектов.
Последнее обстоятельство является весьма важным, так как исследуя некоторую схему, можно получить решение целого конкретных задач, сводящихся к данной схеме.
1.2.Связи и опорные устройства.
Для соединения отдельных частей конструкции между собой и передачи внешней нагрузки на основание на нее накладываются связи, ограничивающие перемещения тех точек сооружения, к которым они приложены. Связи могут ограничивать либо повороты точек сооружения, либо их линейные смещения, либо и то и другое.
Основным видом связей в расчетной схеме является шарнирная связь.
Простой шарнир (рис. 1.3) накладывает две связи.
Рис. 1.3.
В расчетную схему входит основание, т.е. тело, на котоpое опирается cистема в целом, считающееся неподвижной.
Неподвижность расчетной схемы относительно основания обеспечивается опорными связями (опорами).
Рис. 1.4 Опорные связи (опоры).
Все опорные связи условно делятся на три основных типа:
- Подвижная шарнирная опора (рис.1.4, а). Такая опора не препятствует вращению конца бруса и его перемещению вдоль плоскости качения. В ней может возникать только одна реакция, которая перпендикулярна плоскости качения и проходит через ось катка (R).
- Неподвижная шарнирная опора (рис.1.4, б). Такая опора допускает вращение конца бруса, но устраняет поступательное движение ее в любом направлении. Возникающую в ней реакцию можно разложить на две составляющие, одна из которых направлена вдоль оси бруса (Н), другая - перпендикулярно к оси бруса (R).
- Жесткая заделка или защемление (рис.1.4, в). Такое закрепление не допускает ни линейных, ни угловых перемещений опорного сечения. В этой опоре в общем случае может возникать реакция, которую обычно раскладывают на две составляющие (H и R) и момент защемления (М).
При рассмотрении реального объекта в число внешних сил включаются не только заданные нагрузки, но и реакции связей (опор), дополняющие систему сил до равновесного состояния.
1.3. Внешние и внутренние силы. Метод сечений
Силы являются мерилом механического взаимодействия тел. Если конструкция рассматривается изолированно от окружающих тел, то действие последних на нее заменяется силами, которые называются внешними. Внешние силы, действующие на тело, можно разделить на активные (независимые) и реактивные. Реактивные усилия возникают в связях, наложенных на тело, и определяются действующими на тело активными усилиями.
По способу приложения внешние силы делятся на
объемные и поверхностные.
Объемные силы распределены по всему объему рассматриваемого тела и приложены к каждой его частице. В частности, к объемным силам относятся собственный вес сооружения, магнитное притяжение, сила тяжести или силы инерции. Единицей измерения объемных сил является сила, отнесенная к единице объема кН/м3.
Поверхностные силы приложены к участкам поверхности и являются результатом непосредственного контактного взаимодействия рассматриваемого объекта с окружающими телами (давление ветра, воды на стенку).
В зависимости от соотношения площади приложения нагрузки и общей площади поверхности рассматриваемого тела, поверхностные нагрузки подразделяются на сосредоточенные и распределенные.
Если давление q1 (Н/м2) передается на элемент конструкции через площадку, размеры которой очень малы по сравнению с размерами всего элемента (a≪l), то его на основании принципа Сен-Венана можно привести к сосредоточенной силе F (рис. 1/5). Например, воздействие колонн на фундаментную плиту достаточно больших размеров можно рассматривать как действие на нее сосредоточенных усилий.
Сосредоточенная сила F измеряется в ньютонах (Н), килоньютонах (кН). Подобным образом вводятся понятия сосредоточенных изгибающих и крутящих моментов.
Рис. 1/5
Если давление q2 (Н/м2) передается на элемент конструкции через площадку, размеры которой сравнимы с размерами всего элемента (c<l), то его представляют в виде распределенной или погонной нагрузки q3 с размерностью кН/м или кН/м2 (рис. 5). Примером может служить собственный вес балки, действие снеговой или ветровой нагрузки на сооружение, давление жидкости в резервуаре. Распределенная нагрузка может действовать и по линии как, например, при соприкасании двух цилиндров при параллельном расположении их осей.
На расчетной схеме вместо бруса изображается его ось. Нагрузки, распределенные по линии и сосредоточенные в точках, реально не существуют. Их можно получить лишь в результате схематизации реальных нагрузок, распределенных по объему (объемных сил) и по поверхности.
По характеру изменения силы во времени различают нагрузки статические и динамические. Статические нагрузки (постоянные) - такие, которые изменяют свою величину или точку приложения (направление) с очень небольшой скоростью, так что возникающими при этом ускорениями (силами инерции) можно пренебречь. Динамические нагрузки - изменяются во времени с большой скоростью, при этом силы инерции должны быть учтены, так как оказывают существенное влияние на конструкцию. Динамические нагрузки подразделяются на внезапно приложенные, повторно-переменные и ударные. Примером внезапно приложенной нагрузки может служить действие веса железнодорожного состава, проходящего через мост; повторно-переменной – нагрузка на шатун в двигателе внутреннего сгорания; ударной – действие силы удара молота на его фундамент или гидравлический удар в гидросистеме. Ударные нагрузки возникают также в случае плохой пригонки или износа сопряженных деталей, когда зазоры превышают величину, допустимую по конструктивным и технологическим условиям. Например, при износе зубьев шестерен или деталей шариковых подшипников в машине возникают характерные стуки, свидетельствующие о возникновении ударных нагрузок, быстро приводящих к выходу конструкции из строя.
Временная нагрузка может сохранять более или менее постоянную величину в течение всего периода ее действия, а может непрерывно изменяться по некоторому закону; в последнем случае она называется переменной нагрузкой.
Если переменная нагрузка изменяется по циклическому (повторяющемуся) закону, то она называется циклической.
В машиностроении расчетные нагрузки определяются в зависимости от конкретных условий работы машины: по номинальным значениям мощности, угловой скорости отдельных ее деталей, силы тяжести, сил инерции и т. п.
При систематическом чередовании нагружения и разгрузки накопление дефектов структуры ведет к возникновению микроскопических трещин, слияние которых приводит к усталостному разрушению.
По отношению к выбранному материальному телу (элементу конструкции) все действующие силы подразделяются на внешние и внутренние силы. Под внешними силами (нагрузками) понимаются силы взаимодействия данного материального тела со всеми другими окружающими его телами.
Взаимодействие между частями рассматриваемого тела характеризуется
внутренними силами, которые возникают внутри тела под действием внешних нагрузок и определяются силами межмолекулярного воздействия. Эти силы сопротивляются стремлению внешних сил разрушить элемент конструкции, изменить его форму, отделить одну часть от другой. Вообще внутренние силы возникают между всеми смежными частицами тела при нагружении.
Для выявления внутренних сил и последующего их определения применяют метод сечений, суть которого заключается в следующем. Пусть к элементу сооружения, имеющего форму бруса, приложена система внешних сил, удовлетворяющая условиям равновесия. Под действием этой нагрузки в элементе возникают внутренние силы. В произвольном месте мысленно рассечем брус поперечным сечением на две части (рис. 1.6, а).
Рис.1.6. Определение внутренних сил методом сечений:
а) – элемент до рассечения поперечным сечением;
б) – приведение системы внутренних сил к центру тяжести сечения;
в) – разложение главного вектора и главного момента по осям координат
Так как связи между частями устранены, то необходимо действие правой части на левую, и левой на правую заменить системой сил в этом сечении. Эти силы определяют взаимодействие между частицами тела, расположенными по разные стороны от мысленно проведенного сечения, и поэтому являются внутренними для тела в целом. Согласно закону действия и противодействия система сил, возникающих на поверхности сечения в левой отсеченной части, равна, но обратна по знаку системе сил на поверхности сечения в правой отсеченной части. Согласно допущению о сплошности материала следует считать, что внутренние силы распределены по сечению непрерывно по некоторому не известному нам закону.
Внутренние усилия должны быть так распределены по сечению, чтобы деформированные поверхности сечения при совмещении правой и левой частей тела в точности совпадали. Это требование в механике твердого деформируемого тела носит название условия неразрывности деформаций.
Рассмотрим отдельно какую-либо из отсеченных частей бруса, например левую. Внутренние силы, возникающие в сечении целого бруса по отношению к рассматриваемой отсеченной части бруса, являются внешними и дополняют систему заданных внешних сил до равновесной. Приведем систему внутренних сил к центру тяжести сечения (рис. 1.6, б). В результате получим главный вектор R и главный момент M.
Выберем систему координат так, чтобы ось z совпала с нормалью к сечению (располагалась вдоль оси элемента), а оси у и x лежали в плоскости нормального сечения. Разложив главный вектор и главный момент по осям координат, получим составляющие: три силы и три момента. Эти составляющие называют внутренними силовыми факторами в сечении бруса, каждая из которых имеет свое наименование: N - нормальная сила; Qy и Qz - поперечные силы; Т - крутящий момент; Mz и Му - изгибающие моменты относительно осей x и y (рис. 1.6, в).
При известной нагрузке все шесть внутренних силовых факторов могут быть определены из уравнений равновесия составленных для рассматриваемой части бруса. Заметим, что в каждое уравнение войдут проекции на соответствующую ось (или моменты относительно оси) всех внешних сил, приложенных к рассматриваемой части, и только один из внутренних силовых факторов.
ΣZ = ΣFzотс + N = 0; Σmz = ΣMzотс + T = 0;
ΣY = ΣFyотс + Qy = 0; Σmy = ΣMyотс + My = 0;
ΣX = ΣFxотс + Qx = 0; Σmx = ΣMxотс + Mx = 0.
Уравнения равновесия позволяют сформулировать правило определения каждого из внутренних силовых факторов:
Продольная сила в произвольном поперечном сечении бруса численно равна алгебраической сумме проекций на ось z, всех внешних сил, действующих на одну из отсеченных (левую или правую) частей бруса.
N = ΣFzотс.
То же для определения поперечных сил Qy и Qx,, только проектировать внешние силы необходимо на оси y и x.
Qy = ΣFyотс, Qx = ΣFxотс.
Изгибающие моменты Mx и My и крутящий момент T, численно равны алгебраической сумме моментов всех сил по одну сторону от сечения, относительно соответствующих осей x, y и z.
T = ΣMzотс, Mx = ΣMxотс, My = ΣMyотс.
Для установления знака внутреннего силового фактора будем придерживаться следующих правил:
Условимся продольную силу считать положительной, если она вызывает растяжение, т.е. направлена от сечения и отрицательной, если она вызывает сжатие, т. е. направлена к сечению.
При решении задач знак N удобнее устанавливать в зависимости от направления внешних сил. Если внешняя сила, направлена в противоположную от сечения сторону, то она вызывает в нем положительную продольную силу (растяжение), и наоборот, если внешняя сила, направлена к сечению, то она вызывает в нем отрицательную продольную силу (сжатие) (рис. 1.7, а).
Поперечную силу Q будем считать положительной, если она направлена так, что стремиться повернуть отсеченную часть бруса по ходу часовой стрелки (рис. 1.7, б), и отрицательной, если - против хода часовой стрелки.
Согласно этому правилу внешняя сила, стремящаяся повернуть рассматриваемую часть бруса относительно сечения по ходу часовой стрелки, вызывает в сечении положительную поперечную силу
Крутящий момент Т будем считать положительным, если при взгляде со стороны внешней нормали на рассматриваемое сечение он направлен по ходу часовой стрелки или внешний скручивающий момент направлен против хода часовой стрелки (рис.1.7, в).
Изгибающий момент Mx считается положительным, если он вызывает растяжение нижних волокон рассматриваемой части бруса. В противном случае изгибающий момент считается отрицательным (рис. 1.7, г).
Рис. 1.7. Виды сопротивлений:
а) растяжение (сжатие); б) сдвиг; в) кручение; г) изгиб
Согласно принятому правилу знаков для изгибающего момента, если внешняя сила, приложенная к рассматриваемой части бруса изгибает участок, расположенный между сечением точкой ее приложения выпуклостью вниз, то изгибающий момент положительный. Отрицательному значению изгибающего момента соответствует противоположное направление выпуклости балки
Таким образом, метод сечений позволяет найти значения внутренних силовых факторов и установить вид нагружения в любом сечении бруса при действии любой нагрузки. Для этого необходимо выполнить следующее:
1. Мысленно рассекаем брус на две части в пределах исследуемого i–го участка.
2. Оставляем ту часть бруса, на которую действует меньше сил.
3. Заменяем действие условно отброшенной части бруса положительными внутренними силовыми факторами, приведенными к центру тяжести исследуемого сечения бруса.
4. Выберем для оставленной части бруса скользящую систему координат (начало координат совмещаем с границей участка, положение исследуемого сечения определяется координатой zi, где 0≤zi≤c и c – длина i-го участка).
5. Определяем искомые внутренние силовые факторы из уравнений равновесия ΣZ = 0; ΣY = 0; ΣX = 0; Σmz = 0; Σmy = 0; Σmx = 0, которые составляем для оставленной части бруса.
Проверка правильности определения усилий ведется в двух направлениях:
а) выполнение условий равновесия, не использованных при определении внутренних усилий;
б) проверка равновесия части тела, которая не рассматривалась при решении задачи.
В зависимости от вида внутренних силовых факторов, возникающих в сечении, различают различные следующие виды нагружения бруса.
- Растяжение или сжатие. Действует только продольная сила N.
- Кручение. Действует только крутящий момент T.
- Сдвиг. Действует только поперечная сила Qx или Qy
- Изгиб. Действует только изгибающий момент Mx или My (чистый изгиб), при действии изгибающего момента и поперечной силы (поперечный изгиб).
- Сложное сопротивление. Одновременное действие нескольких силовых факторов. Например, Mx и T, M и N.
Итак, внутренние усилия в сечении есть функции параметров, определяющих положение сечения в теле, и нагрузок по одну сторону от сечения. Эти функции могут быть представлены аналитически или графически. График, показывающий изменение внутреннего усилия в зависимости от положения сечения, называется эпюрой. Ординаты усилий в определенном масштабе откладывают от линии, соответствующей оси бруса.
1.4. Дифференциальные уравнения равновесия для внутренних усилий в поперечных сечениях стержней
В общем случае нагрузка на стержень может быть задана интенсивностью сил с составляющими n, qy, qz, и интенсивностью моментов с составляющими t, my, mz. Возможна также нагрузка, сосредоточенная в отдельных точках. Для бесконечно малой части стержня (рис.8) составим дифференциальные уравнения равновесия.
Рис. 1.8
Из условий ΣX=0, ΣY=0, ΣZ=0, ΣMx=0, следуют уравнения:
Из условий ΣX=0, ΣY=0, ΣZ=0, ΣMx=0, следуют уравнения:
Из условий ΣMy=0, ΣMz=0 получаем:
откуда, пренебрегая бесконечно малыми второго порядка, находим
Подставляя выражения Qy и Qz в соответствующие дифференциальные уравнения, получаем
Интегрируя полученные шесть уравнений, находим выражения для внутренних усилий:
Постоянные интегрирования Сi (i=1,2,...,6) определяются из граничных условий для рассматриваемых внутренних усилий.
Поскольку дифференциальные уравнения выражают равновесие любого бесконечно малого элемента стержня, то удовлетворение им означает выполнение условий равновесия стержня в целом.
Дифференциальные зависимости используются для проверки результатов, полученных с помощью алгебраических уравнений равновесия. Они позволяют, например, по эпюре Mz(My) определить характер эпюры Qy(Qz). В частности, на участках, где mz=0 (my=0), т.е. при соблюдении зависимостей
можно установить, что при Мz = const имеем Qy = 0 (при Мy = const имеем Qz = 0). Переменная величина Mz(My) достигает экстремальных значений в точках, где Qy = 0 (Qz = 0).
При определении внутренних усилий из уравнений равновесия целесообразно нагрузку на поверхности переносить в соответствующие точки на оси стержня с соблюдением условий статической эквивалентности. Полученная таким образом силовая схема является составной частью так называемой расчетной схемы (системы), когда брус представляется его осью.
1.5. Допущения, применяемые в сопротивлении материалов
Для построения теории сопротивления материалов принимают некоторые понятия и допущения относительно структуры и свойств материалов, а также о характере деформаций. Приведем основные из них.
1. В сопротивлении материалов принято рассматривать все материалы как однородную сплошную среду, независимо от их микроструктуры.
Под однородностью материала понимают независимость его свойств от величины выделенного из тела объема. И хотя в действительности реальный материал, как правило, неоднороден (уже в силу его молекулярного строения), тем не менее, указанная особенность не является существенной, поскольку в сопротивлении материалов рассматриваются конструкции, размеры которых существенно превышают не только межатомные расстояния, но и размеры кристаллических зерен.
С понятием однородности тесно связано понятие сплошности среды, под которым подразумевают тот факт, что материал конструкции полностью заполняет весь отведенный ему объем, а значит в теле конструкции нет пустот и не учитывается реальная структура материала (зернистая, кристаллическая и др.). Это допущение позволяет использовать в сопротивлении материалов методы математического анализа (дифференциальное и интегральное исчисления). Для большинства машиностроительных конструкций расчеты, основанные на допущении о сплошности строения дают
практически удовлетворительные результаты. Это объясняется тем, что размеры детали во много раз больше межатомных расстояний.
2. Обычно сплошная среда принимается изотропной, т.е. предполагается, что свойства тела, выделенного из нее, не зависят от его ориентации в пределах этой среды. Материалы, имеющие различные свойства в разных направлениях, называют анизотропными (например, дерево, ткани (косой и кривой крой), армированная пластмасса, бетон). К анизотропным относятся и материалы с направленной кристаллизацией и с монокристаллической структурой. Отдельно взятый кристалл материала анизотропен, но т.к. в объеме реального тела содержится бесконечно большое количество хаотично расположенных кристаллов, принимается, что материал изотропен.
Металлы и сплавы, как правило, изотропны, так как большинство металлов имеет мелкозернистую структуру. Благодаря большому количеству кристаллов свойства материалов выравниваются в различных направлениях и можно считать эти материалы практически изотропными. В настоящее время широкое распространение получили анизотропные композиционные материалы, состоящие из двух компонентов – наполнителя и связующего. Наполнитель состоит из уложенных в определенном порядке высокопрочных нитей – матрицы, что и определяет значительную анизотропию композита. Композиционные материалы имеют высокую прочность при значительно меньшем, чем металлы весе.
3. Принимается, что до определенной величины деформации материалов подчиняются закону Гука и весьма малы относительно размеров тела, поэтому все расчеты выполняются по исходной, т.е. недеформированной, схеме, к которой применим принцип независимости действия сил (принцип суперпозиции).
Результат воздействия на тело системы сил равен сумме результатов воздействия тех же сил, прилагаемых к телу последовательно и в любом порядке (рис. 1.9). Под словами «результат воздействия» следует понимать – деформации, внутренние силы и перемещения отдельных точек.
Рис. 19. Использование принципа суперпозиции
Должны соблюдаться два условия:
1. перемещения малы по сравнению с размерами тела,
2. перемещения линейно зависят от силы.
С помощью этого принципа сложный случай приводится к простым.
4. После снятия нагрузки геометрические размеры тела полностью или частично восстанавливаются. Свойство тела восстанавливать свои первоначальные размеры после разгрузки называется упругостью. При решении большинства задач в сопротивлении материалов принимается, что материал конструкций абсолютно упругий. Это допущение справедливо, пока нагрузки не превышают определенного значения. При больших нагрузках в элементах конструкций появляются пластические деформации. Пластичностью называется свойство тела сохранять после прекращения действия нагрузки, или частично полученную при нагружении, деформацию.
Ползучестью называется свойство тела увеличивать деформацию при постоянных внешних нагрузках.
5. Перемещения, возникающие под действием внешних сил в упругом теле, малы по сравнению с его размерами. Это допущение называется принципом начальных размеров. В большинстве случаев механические конструкции работают в упругой зоне (в зоне действия закона Гука), а упругие деформации малы по сравнению с геометрическими размерами (рис. 1.10). Допущение позволяет при составлении уравнений равновесия пренебречь изменениями формы и размеров конструкции.
∆l≪l
Рис. 1.10. Принцип неизменности геометрических размеров
6. Предполагается, что в сечениях, достаточно удаленных от мест приложения нагрузки, характер распределения напряжений не зависит от конкретного способа нагружения. Основанием для такого утверждения служит принцип Сен-Венана, справедливый для любого типа напряженного состояния и формулируемый следующим образом: особенности приложения внешних нагрузок проявляются, как правило, на расстояниях, не превышающих характерных размеров поперечного сечения стержня или другое определение: в точках тела, достаточно удаленных от мест приложения нагрузок, величина внутренних сил весьма мало зависит от конкретного способа приложения этих нагрузок, а зависит только от ее статического эквивалента (рис. 11). Этот принцип во многих случаях позволяет производить замену одной системы сил другой системой, статически эквивалентной, что позволяет часто значительно упростить расчет.
Рис. 1. 11. Использование принципа Сен-Венана
7. Принимается гипотеза плоских сечений (гипотеза Бернулли),
введенной швейцарским ученым Д. Бернулли, гласящей, что плоские поперечные сечения стержня до деформации остаются плоскими и после деформации (рис.12).
Рис. 1.12. Гипотеза плоских сечений
8. Считается, что ненагруженное тело свободно от каких бы то ни было внутренних сил любой природы. Изменению формы и размеров тела под нагрузкой сопротивляются силы взаимодействия между частицами материала, называемые силами упругости. В дальнейшем, говоря о внутренних силах, будем иметь в виду именно эти силы упругости, не принимая во внимание молекулярные силы, имеющиеся и в ненагруженном теле. Это допущение полностью не выполняется ни для одного материала. Причины возникновения неравномерных внутренних или начальных усилий:
- В стальных деталях из-за неравномерного остывания;
- В дереве из-за неравномерного высыхания;
- В бетоне в процессе твердения.
В тех случаях, когда есть основания предполагать, что эти силы значительны, стараются определить их экспериментально. Однако, часто они достаточно малы, чтобы их учитывать.
Использование этих понятий и допущений существенно упрощает изучение поведения конструкций под нагрузкой, а соответствие условного материала реальным материалам достигается введением в расчет элементов сооружений экспериментально получаемых механических характеристик реальных материалов.
При определении внутренних силовых факторов их считают приложенными в центре тяжести сечения. В действительности внутренние силы, являясь результатом взаимодействия частиц тела, непрерывно распределены по сечению. Интенсивность этих сил в разных точках сечения может быть различной. При увеличении нагрузки на элемент конструкции увеличиваются внутренние силы и соответственно увеличивается их интенсивность во всех точках сечения. Если в некоторой точке интенсивность внутренних сил достигнет определенного для данного материала значения, в этой точке возникает трещина, развитие которой приведет к разрушению элемента, или возникнут недопустимые пластические деформации. Следовательно, о прочности элементов конструкций следует судить не по значению внутренних силовых факторов, а по их интенсивности. Меру интенсивности внутренних сил называют напряжением.
В окрестности произвольной точки, принадлежащей сечению некоторого нагруженного тела, выделим элементарную площадку , в пределах которой действует внутреннее усилие ∆F (рис. 1.13, а).
Среднее значение интенсивности внутренних усилий на площадке, называемое средним напряжением, определяют по формуле
Уменьшая площадь ∆A, в пределе получаем истинное напряжение в данной точке сечения
Векторная величина p называется полным напряжением в точке. В международной системе единиц (СИ) за единицу напряжения принят паскаль (Па=Н/м2) – это напряжение, при котором на площадке 1 м2 действует внутренняя сила 1 Н.
Так как эта единица очень мала, в расчетах используют кратную единицу напряжения – мегапаскаль (1 МПа=106 Па).
Разложим вектор полного напряжения p на две составляющие (рис.1.13, б).
Проекция вектора полного напряжения p на нормаль к данной площадке обозначается через σ и называется нормальным напряжением.
Рис. 1.13
Составляющую, лежащую в сечении в данной площадке обозначается через τ и называется касательным напряжением.
Нормальное напряжение, направленное от сечения, считают положительным, направленное к сечению – отрицательным.
Нормальные напряжения возникают, когда под действием внешних сил частицы, расположенные по обе стороны от сечения, стремятся удалиться одна от другой или сблизиться. Касательные напряжения возникают, когда частицы стремятся сдвинуться одна относительно другой в плоскости сечения.
Касательное напряжение можно разложить по координатным осям на две составляющие и (рис.1.13, в). Первый индекс при τ показывает, какая ось перпендикулярна сечению, второй – параллельно какой оси действует напряжение. Если в расчетах направление касательного напряжения не имеет значения, его обозначают без индексов.
Между полным напряжением и его составляющими существует зависимость
Через точку тела можно провести бесконечное число сечений и для каждого из них напряжения имеют свое значение. Следовательно, при определении напряжений необходимо указывать положение не только точки тела, но и сечения, проведенного через эту точку.
Совокупность напряжений для множества элементарных площадок, проходящих через данную точку, образует напряженное состояние в этой точке.
В дифференциальные уравнения равновесия бесконечно малого прямоугольного параллелепипеда входят шесть независимых скалярных величин, соответствующих составляющим напряжений по его граням. Они определяют тензор напряжений:
При этом учитывается свойство парности касательных напряжений (τxy = τyx, τxz = τzx, τyz= τzy): на двух взаимно перпендикулярных площадках составляющие касательных напряжений, перпендикулярные к линии пересечения площадок, равны по величине и взаимно направлены либо к линии пересечения, либо от нее.
Если площадка dA совпадает с поверхностью тела, то составляющие напряжения трансформируются в составляющие внешних сил, действующих на поверхности тела. Соответствующие уравнения выражают условия на поверхности, или статические граничные условия.
Площадка, на которой касательные напряжения равны нулю, называется главной. Через точку проходят три главные площадки. По ним действуют главные напряжения, которые обозначаются σ1, σ2, σ3 (σ1≥σ2 ≥σ3).
Напряжения в поперечных сечениях связаны с внутренними силовыми факторами определенными зависимостями.
Возьмем в сечении бесконечно малую площадку площадью dA. По этой площадке в общем случае действуют бесконечно малые (элементарные) внутренние силы (рис. 1.14)
Рис. 1.14
Соответствующие элементарные моменты относительно координатных осей x, y, z имеют вид:
Просуммировав бесконечно малые силы и моменты, действующие в сечении, получим выражения, связывающие внутренние силовые факторы с напряжениями:
В соответствии с теоремой Вариньона, известной из теоретической механики, и зависимостью между напряжениями τ, и , выражение для можно записать в виде
где
Интегральные зависимости (1.4) можно использовать для определения напряжений по найденным методом сечений внутренним силовым факторам при условии, что известны законы распределения напряжений по сечению. Поскольку эти законы зависят от вида деформации, то обратная задача (определение напряжений через внутренние усилия) решается путем совместного использования условий равновесия и условий деформирования тела. Задача становится статически неопределимой.
Под действием внешних сил твердые тела изменяют свою геометрическую форму, то есть деформируются. Если в теоретической механике тела считаются абсолютно жесткими, то в сопротивлении материалов тела обладают способностью деформироваться, т.е. под действием внешней нагрузки изменять свои начальные размеры и форму. Точки тела при этом неодинаково перемещаются в пространстве. Вектор , имеющий свое начало в точке А недеформированного состояния, а конец в т. деформированного состояния, называется вектором полного перемещения т. А (рис. 15, а). Его проекции на оси xyz называются осевыми перемещениями и обозначаются u, v и w, соответственно.
Для того, чтобы охарактеризовать интенсивность изменения формы и размеров тела, рассмотрим точки А и В его недеформированного состояния, расположенные на расстоянии S друг от друга (рис. 15, б).
Рис. 1.15
Пусть в результате изменения формы тела эти точки переместились в положение и , соответственно, а расстояние между ними увеличилось на величину S и составило S + S. Величина
называется линейной деформацией в точке А по направлению АВ. Если рассматривать деформации по направлениям координатных осей xyz, то в обозначения соответствующих проекций линейной деформации вводятся индексы , , .
Линейные деформации , , характеризуют изменения объема тела в процессе деформирования, а формоизменения тела угловыми деформациями. Для их определения рассмотрим прямой угол, образованный в недеформированном состоянии двумя отрезками ОD и ОС (рис. 1.15, б). При действии внешних сил указанный угол DOC изменится и примет новое значение . Величина
называется угловой деформацией, или сдвигом в точке О в плоскости СОD. Относительно координатных осей деформации сдвига обозначаются , , .
Линейные и угловые деформации – величины безразмерные. Деформацию , , часто называют относительной линейной деформацией, а , , – относительным сдвигом.
Положительными принимают линейную деформацию, соответствующую растяжению, и деформацию сдвига, отвечающую уменьшению первоначального угла пересечения отрезков. Полагая деформации малыми, мы можем в дальнейшем пренебрегать ими по сравнению с единицей, а также их высокими степенями по сравнению с первой степенью.
Совокупность линейных и угловых деформаций по различным направлениям и плоскостям в данной точке образует деформированное состояние в точке. В случае малых деформаций оно полностью определяется линейными деформациями трех взаимно перпендикулярных линейных элементов тела, проходящих через данную точку, и тремя деформациями сдвига этих линейных элементов. Соответствующие шесть независимых скалярных величин определяют тензор деформаций:
Главные оси деформации – три взаимно перпендикулярные прямые, проходящие через данную точку тела и совпадающие по направлениям с такими тремя линейными элементами тела, которые остаются взаимно перпендикулярными и после деформации. Линейные деформации по направлениям этих осей называются главными деформациями и обозначаются ε1, ε2, ε3 (ε1≥ε2≥ε3).
Следует подчеркнуть, что в сопротивлении материалов слово деформация имеет данное выше строгое определение и выступает как количественная мера изменения геометрических размеров в окрестностях точки.
1.8. Закон Гука и принцип независимости действия сил
Многочисленные экспериментальные наблюдения за поведением деформируемых тел показывают, что в определенных диапазонах перемещения точек тела пропорциональны действующим на него нагрузкам. Впервые указанная закономерность была высказана в 1776 году английским ученым Р.Гуком в формулировке «ut tensio sic vis» - «какого растяжение - такова и сила» и носит название закона Гука.
В соответствии с этим законом перемещение произвольно взятой точки А (рис. 15, а) нагруженного тела по некоторому направлению, например, по оси x, а может быть выражено следующим образом:
где Р - сила, под действием которой происходит перемещение u; - коэффициент пропорциональности между силой и перемещением.
Очевидно, что коэффициент зависит от физико-механических свойств материала, взаимного расположения точки А и точки приложения и направления силы Р, а также от геометрических особенностей системы. Таким образом, последнее выражение следует рассматривать как закон Гука для данной системы.
В современной трактовке закон Гука определяет линейную зависимость между напряжениями и деформациями, а не между силой и перемещением.
Касательные напряжения τ вызывают угловые деформации γ, причем при малых деформациях они не влияют на изменение линейных размеров и, следовательно, на линейные деформации. Нормальное напряжение σ не влияет на угловые деформации, так как при этом изменяются только линейные размеры отрезков, а не углы между ними.
Параметры E и G, входящие в эти формулы, называют модулями упругости материала соответственно первого и второго рода. Они характеризуют его сопротивляемость деформированию, или жесткость в упругой стадии деформации. При одном и том же напряжении деформации больше у того материала, у которого меньше модуль упругости. Численные значения E и G для каждого конструктивного материала определяются экспериментально. Они имеют размерности напряжений. На практике удобно использовать единицы, кратные паскалю: мегапаскаль (1 МПа=106 Па) и гигапаскаль (1 ГПа=109 Па).
При растяжении или сжатии одновременно с продольной деформацией ε =∆l/l (рис. 16, а), в элементе возникает поперечная деформация = -∆а/а.
Отношение
называют коэффициентом Пуассона.
Величины коэффициента Пуассона и модуля упругости для различных материалов определяют опытным путем и их значения приведены в ГОСТ. Между модулем упругости и модулем сдвига существует зависимость
Установим связь между нормальными напряжениями и линейными деформациями, справедливые для любого напряженного состояния. Рассмотрим бесконечно малый элемент, имеющий форму кубика, на гранях которого возникают напряжения растяжения σx, σy, σz. При действии только напряжения σx, элемент получает продольную деформацию в направлении оси х, равную, согласно закону Гука, σx/Е (рис. 16,б). Одновременно его размеры вдоль осей y и z уменьшатся, при этом соответствующие поперечные деформации будут равны
Аналогичное действие оказывает растягивающие напряжения σy и σz.. Каждое из них вызывает продольную деформацию в своем направлении σу/Е и σz/Е и поперечные деформации по двум другим направлениям (рис. 16,в, г).
Суммируя деформации в направлениях каждой оси, получаем
Эти зависимости представляют собой математические выражения обобщенного закона Гука. Напряжения σx, σy, σz следует подставлять в формулы со своим знаком.
Рис. 1.16. Деформация элемента при растяжении:
а) общий вид элемента; б) деформации в направлении оси z;
в) то же оси x; г) то же оси у
Системы, для которых соблюдается условие пропорциональности между напряжениями и деформациями, подчиняются принципу суперпозиции, или принципу независимости действия сил.
В соответствии с этим принципом перемещения и внутренние силы, возникающие в упругом теле, считаются независящими от порядка приложения внешних сил. То есть, если к системе приложено несколько сил, то можно определить внутренние силы, напряжения, перемещения и деформации от каждой силы в отдельности, а затем результат действия всех сил получить как сумму действий каждой силы в отдельности. Принцип независимости действия сил является одним из основных способов при решении большинства задач механики линейных систем.
1.9. Общие принципы расчета конструкции
В результате расчета нужно получить ответ на вопрос, удовлетворяет или нет конструкция тем требованиям прочности и жесткости, которые к ней предъявляются. Для этого необходимо прежде всего сформулировать те принципы, которые должны быть положены в основу оценки условий достаточной прочности и жесткости.
Условие невозникновения предельного состояния (условие прочности) в материале в рассматриваемой точке тела имеет форму неравенства
σпред (или σred)< σmax ,
которое отражает сущность так называемого поверочного расчета.
Методы расчета конструкций выбираются в зависимости от условий работы конструкций и требований, которые к ней предъявляются. Так, наиболее распространенным методом расчета деталей машин на прочность является расчет по методу допускаемых напряжений. В основу этого метода положено предположение, что определяющим параметром надежности конструкции является напряжение или, точнее говоря, напряженное состояние в точке. Если предельным состоянием материала в локальной области является хрупкое разрушение, то это может представить опасность для всей конструкции в силу развития области разрушения. В этой ситуации использование метода допускаемых напряжений является вполне обоснованным.
Расчет выполняется в следующем порядке.
На основании анализа напряженного состояния конструкции выявляется та точка сооружения, где возникают наибольшие расчетные (рабочие) напряжения . Расчетная величина напряжений сопоставляется с предельно допустимой величиной напряжений (или σred) для данного материала, полученной на основе предварительных лабораторных испытаний. Чтобы не нарушилась прочность элемента, рабочие напряжения в любой его точке должны быть меньше предельных. Для особо ответственных конструкций, для которых требуется не допускать возникновения пластических деформаций, за величину (или σred) принимается . В тех случаях, когда допустимо возникновение пластических деформаций, как правило, принимается . Для хрупких материалов, а в некоторых случаях и умеренно пластических материалов, принимается .
Для надежной работы элемента нельзя допустить, чтобы рабочие (расчетные) напряжения в наиболее напряженной точке были близки к предельным, нужно обеспечить запас прочности.
Отношение предельного напряжения для материала, из которого изготовлен элемент конструкции, к максимальному рабочему напряжению называют коэффициентом запаса прочности (или коэффициентом безопасной прочности).
Выбор коэффициента запаса прочности – один из основных и наиболее ответственных этапов расчета на прочность. При заниженном коэффициенте запаса прочности снижается надежность работы детали, повышается опасность ее разрушения при эксплуатации. При завышении запаса прочности увеличивается масса и стоимость детали.
Коэффициент запаса учитывает следующие основные факторы.
1. Погрешности в создании рабочей модели. Т.е. способы определения усилий в элементах конструкций сопряжены с некоторыми условностями.
2. Заданные нагрузки не вполне достоверны. Возможны превышения нагрузки в процессе эксплуатации.
3. Степень ответственности изделия.
4. Размеры сечений имеют некоторые допуски при изготовлении и могут меняться в течение срока службы конструкции (износ, коррозия и т.д.).
5. Несовершенства в определении свойств материала. Величины, характеризующие прочность и пластичность материала, могут быть разными для разных партий материала одной и той же категории.
6. Величины, характеризующие прочность и пластичность материала, могут быть разными для разных партий материала одной и той же категории; д) в некоторых случаях учет концентрации напряжений связан с рядом грубых допущений.
7. Необходимо считаться с особенностями действия динамических нагрузок и некоторыми другими факторами.
8. Вероятность возможных экстремальных ситуаций (землетрясение, случайный удар и т.п.).
При назначении коэффициента запаса прочности учитывают, насколько точно можно для проектируемой детали определить рабочее и предельное напряжения. Рабочие напряжения нельзя определить абсолютно точно, так как фактические, действующие на элемент конструкции нагрузки могут существенно отличаться от используемых в расчете. В процессе эксплуатации конструкции возможно кратковременное увеличение нагрузок (перегрузки), часто нагрузки непрерывно изменяются или носят случайный характер (например, нагрузки на крыло летящего самолета). Формулы сопротивления материалов основаны на определенных допущениях, упрощающих расчеты, и, следовательно, не обеспечивают высокой точности. В деталях сложной формы напряжения, как правило, можно определить только приближенно. Предельные напряжения, характеризующие прочность материала, также нельзя определить абсолютно точно вследствие непостоянства химического состава сплавов в различных плавках, отклонений в режимах технологического процесса изготовления материалов, погрешностей при испытании образцов. При расчете элемента конструкции необходимо учитывать возможные последствия его разрушения.
Так как все факторы, влияющие на прочность элемента конструкции, учесть точно в расчете невозможно, в расчет вводят требуемый (допускаемый) коэффициент запаса прочности , гарантирующий надежную работу элемента конструкции в течение требуемого срока службы (табл.1.1)
Таблица 1.1.
Ориентировочные значения допускаемого коэффициента запаса прочности
Вид материала |
Характер нагрузки |
Коэффициент запаса прочности |
Пластичный |
Статическая |
2,4-2,6 |
Ударная |
2,8-5,0 |
|
Повторно-переменная |
5,0-15,0 |
|
Хрупкий |
Статическая |
3,0-9,0 |
Часто этот коэффициент представляют в виде произведения частных коэффициентов запаса каждый из которых учитывает влияние на прочность элемента конструкции какого-либо одного ил нескольких факторов.
В каждой отрасли машиностроения существуют нормы на допускаемые запасы прочности, основанные на большом опыте расчета деталей и их эксплуатации. Определяемые по нормам коэффициенты запасы прочности называют нормативными.
Прочность элемента конструкции считают обеспеченной, если расчетный коэффициент запаса не меньше допускаемого
Это равенство называют условием прочности.
Если установлен допускаемый коэффициент запаса прочности и для выбранного материала известно предельное напряжение, определяют максимальное напряжение, которое можно допустить для надежной работы элемента конструкции. Такое напряжение называют допускаемым
Часто величина допускаемого напряжения берется из таблиц, составленных на основе действующих норм. В практических расчетах считают, что прочность элемента конструкции обеспечена, если возникающие в нем максимальные напряжения не превышают допускаемых. Условие прочности имеет вид
Если материал имеет различные предельные напряжения при растяжении и сжатии, то допускаемое напряжение обозначают соответственно и .
Чтобы уточнить, какое напряжение принято в качестве предельного (предел текучести или прочности ), иногда в обозначения расчетных и допускаемых коэффициентов запаса прочности вводят соответствующие индексы: ; ; ; .
Вопросы для самопроверки
- В чем заключаются задачи курса «Сопротивление материалов»?
- Назовите выдающихся русских ученых в области прочности материалов?
- Что называют прочностью, жесткостью, устойчивостью детали?
- Что такое расчетная схема объекта?
- Укажите геометрические признаки стержня, оболочки и массивного тела.
- Какой брус называется призматическим?
- Изложите основные требования при проектировании машин и сооружений?
- Какие силы в сопротивлении материалов считают внешними? Какие силы являются внутренними?
- Что называют внутренними усилиями?
- Как определяют внутренние усилия?
- Какие правила знаков приняты для каждого из внутренних усилий?
- Являются ли реакции опор внутренними усилиями?
- В чем суть метода сечений?
- Как вычисляются продольная и поперечная силы в сечении?
- Как вычисляется изгибающий момент?
- Какие типы опор применяются для закрепления балок к основанию?
- Какие внешние реактивные силы возникают в различных опорах?
- Какие уравнения используют для определения опорных реакций?
- Как проверить правильность определения реакций?
- Какими методами определяют внешние силы? Как называют метод для определения внутренних сил?
- Как классифицируются нагрузки, действующие на части машин и сооружений?
- Что такое сосредоточенная сила, распределенная нагрузка и момент?
- Какие нагрузки принято считать сосредоточенными?
- Какое тело называют брусом? Нарисуйте любой брус и укажите ось бруса и его поперечное сечение?
- Как в сопротивлении материалов располагают систему координат?
- Что в сопротивлении материалов называют внутренними силовыми факторами?
- Перечислите внутренние силовые факторы.
- Как определяются внутренние силовые факторы через внешние силы?
- Запишите систему уравнений, используемую при определении внутренних силовых факторов в сечении?
- Как обозначается и как определяется продольная сила в сечении?
- Как обозначаются и как определяются поперечные силы?
- Как обозначаются и определяются изгибающие и крутящие моменты?
- Какие деформации вызываются каждым из внутренних силовых факторов?
- Поясните суть метода сечений.
- Как определяют внутренние силовые факторы?
- Какие основные виды деформаций вызываются внешними силами?
- Дайте определение понятия «напряжения» и какие виды напряжения вы знаете?
- В каких единицах измеряются напряжения?
- Чем отличаются нормальные напряжения от касательных?
- Как связаны напряжения в сечении с внутренними силовыми факторами?
- Какое напряжение называется нормальным и какое касательным?
- Что называется деформацией? Какие деформации называют упругими?
- Какие гипотезы используются при изучении курса «Сопротивление материалов»?
- Сформулируйте закон Гука и принцип суперпозиции.
- Перечислите основные допущения сопротивления материалов.
- Дайте формулировку принципа Сен-Венана?
- Что называется абсолютным удлинением?
- Что понимается под гипотезой плоских сечений?
- Что характеризует модуль упругости первого рода? Какова его размерность?
- Что такое коэффициент Пуассона?
- Как определить потенциальную энергию деформации при растяжении (сжатии)?
- Что называют прочностью, пластичностью, упругостью, твердостью материала?
- В чем заключается гипотеза о сплошности и изотропности материалов? Какие тела называются анизотропными?
- Какие напряжения считают предельными для материалов?
- Что представляет собой коэффициент запаса прочности, с какой целью и как его назначают?
- В чем заключается условие прочности элемента конструкции?
- Перечислите основные принципы расчета инженерных конструкций.
- Рабочее напряжение, возникающее в детали, равно 160 МПа, а опасное (предельное) напряжение для материала детали σпред=320 МПа. Определить коэффициент запаса прочности?
2. Виды испытаний материалов
Инженерные расчеты конструкций невозможны без сведений о материалах, из которых они изготавливаются. Все фактические сведения о конструкционных материалах, т.е. их механические характеристики, получают экспериментально. При опытном изучении образцов получают сведения об основных механических свойствах материалов к которым относятся прочность, жесткость, упругость, пластичность, твердость и др., устанавливают степень влияния на механические характеристики температуры, радиоактивного облучения, термообработки и других факторов.
Прочность - это способность конструкции сопротивляться разрушению при действии на нее внешних сил (нагрузок).
Жесткость - способность элемента конструкции сопротивляться деформации.
Упругость - это способность твердого деформируемого тела восстанавливать свою форму и объем после прекращения действия внешних нагрузок.
Пластичность - это свойство твердого деформируемого тела до разрушения необратимо изменять свою форму и объем от действия внешних сил.
Твердость – способность материала оказывать сопротивление деформированию и разрушению при местных контактных воздействиях.
Вязкость - это свойство оказывать сопротивление за счет трения происходящего при перемещении элементарных частиц тела относительно друг друга в процессе деформирования. Отметим, что при этом, как показывают результаты экспериментов, сила сопротивления, возникающая за счет внутреннего трения материалов, прямым образом зависит от величины скорости перемещения элементарных частиц относительно друг друга.
Ползучесть - это явление, характеризующее изменения во времени величин деформаций и напряжений в теле при действии статических нагрузок.
Выносливость - это явление, которое характеризуется чувствительностью и изменениями прочностных свойств материалов в зависимости от числа циклов нагружения.
В связи с различным использованием материалов на практике созданы разнообразные виды и методы испытаний.
Виды испытаний можно классифицировать следующим образом:
1) По характеру воздействия:
- кратковременные испытания;
- длительные испытания.
2) По виду напряженного состояния:
- испытания на растяжение, сжатие, изгиб, кручение, срез;
- испытания в условиях сложного напряженного состояния.
3) Технологические испытания:
- испытания для контроля пластичности;
- измерение твердости;
- испытание на вытяжку.
4) Испытание переменной нагрузкой:
- испытание на выносливость;
- испытание на малоцикловую усталость.
5) Испытание ударом:
- испытание на ударное растяжение;
- испытание изгибом на ударную вязкость;
- испытание поворотным ударом.
6) Натурные испытания:
- испытание на стендах;
- испытание готовых изделий.
При всех видах механических испытаний образцы металлов по возможности подвергаются тем же внешним воздействиям, что и на практике. Получаемые при этом механические характеристики свойств материала условны, т.к. они зависят от условий испытаний, поэтому методы испытаний унифицируются в рамках ГОСТов, рекомендаций, правил и международных рекомендаций с целью получения сопоставимых данных. Численные значения механических характеристик сводятся в справочные таблицы.
Машины, используемые для проведения испытаний материалов, должны обеспечивать необходимые постоянные скорости нагружения (или деформирования) образцов. Их оснащают аппаратурой для снятия показаний результатов опытов, а в необходимых случаях – приспособлениями для записи диаграммы испытаний. В лабораторных исследованиях используют специальные машины, способные деформировать и разрушать образцы при статических и динамических нагрузках с применением стандартных образцов на растяжение, сжатие, сдвиг, сдвиг, удар и др.
2.1. Требования к образцам, и их классификация
Объекты исследования при механических испытаниях – образцы, модели, элементы конструкций и конструкции в натуральную величину. Наиболее широко используются образцы. Образцом называется тело специальной формы, подвергающееся испытанию для оценки механических свойств материала. В настоящее время испытывают разнообразные образцы, которые отличаются друг от друга формой, размерами, назначением. Некоторые типы образцов регламентируются нормативами. К ним относятся образцы для испытаний на одноосное растяжение и сжатие, на кручение и изгиб, образцы для усталостных испытаний и др.
Условия проведения эксперимента реализуются путем выбора формы образца, приложением к нему таких внешних сил, при которых с достаточной степенью достоверности можно считать, что напряженное и деформированное состояния во всех точках исследуемого образца одинаковы, т. е. в нем создано однородное напряженно-деформиро-ванное состояние. Обеспечив такие условия эксперимента, по измерениям взаимных перемещений точек на поверхности образца можно судить о деформациях во внутренних точках. По измеренным внешним силам можно рассчитать напряжения во внутренних точках исследуемого образца, приняв гипотезы однородности, сплошности и изо тропности. На рабочей части образца выделяется расчетный участок, который используется для измерения соответствующих параметров (удлинений, укорочений, углов закручивания и поворота, изменений поперечных размеров и др.).
Геометрические формы образцов из металлов и сплавов, предназначенных для исследования упругопластических и прочностных свойств, весьма многообразны, но наиболее широко используются образцы в виде стержня с утолщениями на его концах (рис. 2.1). Эти утолщения называются головками. Форма головки зависит от конструкции захватов испытательной машины, соответствующих виду нагрузок на образец (рис. 2.2).
Рис. 2.1. Цилиндрический образец для
испытаний на растяжение:
1 – головка; 2 – рабочая часть
Рис. 2.2. Типы головок цилиндрических образцов для испытаний на растяжение
Длина рабочей части в 5–10 раз превышает ее наибольший поперечный размер. Способ закрепления образцов не должен допускать их проскальзывания относительно захватов, смятия опорных поверхностей головок, а также разрушения образцов на переходных участках и в головках.
При испытании на растяжение образцов, находящихся в хрупком состоянии, принимаются все меры к снижению концентрации напряжений и к высокоточному осевому нагружению образца. Образец из хрупкого материала показан на рисунке 5.
Образцы для испытаний на одноосное сжатие, как правило, не имеют головок и представляют собой короткие цилиндры или призмы в зависимости от вида заготовки. Отношение длины рабочей части образца к его наибольшему поперечному размеру для предотвращения изгиба не должно превышать трех (рис. 2.3). Торцы образца необходимо изготовить параллельными друг другу и перпендикулярными оси образца.
Рис. 2.3. Образец для испытаний на сжатие
Механические характеристики носят условный характер, так как зависят от метода испытаний и способа обработки экспериментальных данных. Поэтому оценку механических характеристик проводят строго регламентированными методами, что необходимо для обеспечения сопоставимости их значений.
К механическим характеристикам относится модуль упругости, коэффициент Пуассона, модуль сдвига, пределы пропорциональности, упругости, текучести и прочности, относительные остаточные удлинения и сужения после разрыва.
Машины для испытаний на растяжение системы И. В. Кудрявцева и М. И. Чулошникова
· Центральным научно-исследовательским институтом точного машиностроения сконструированы для испытания образцов на растяжение машины силой 4 т (ИМ-4) и 12 т (ИМ-12). Принципиальные схемы обеих машин аналогичны. На этих машинах можно испытывать цилиндрические образцы диаметром от 3 до 10 мм (ИМ-4Р) и от 6 до 15 мм (ИМ-12), а также плоские образцы соответственных размеров. Схемы машины ИМ-4Р даны на рисунке 4.
а) б)
Рис. 2.4. Схема машины ИМ-4Р
На станине 1 смонтированы все устройства машины. Образец при испытании на растяжение устанавливают в захваты 2 и 3. Рукоятью 4 приводится во вращение система зубчатых зацеплений 5, заканчивающихся зубчатой гайкой 6, которая втягивает в себя винт 7. В верхней части винта 7 устроен захват 2.
Создаваемое при этом усилие через образец передаётся захвату 3. От захвата 3 через тягу 8 усилие действует на короткое плечо рычага 9. Тяга 10 соединяет конец длинного плеча рычага 9 с коротким концом коленчатого рычага 11, который вместе с грузами 12 является маятником, уравновешивающим своим отклонением возникающее в образце усилие.
Отклонение маятника (пропорциональное силе, растягивающей образец) вызывает поворот рычага 14, насаженного на общую с маятником ось 13. Верхний конец рычага 14 приводит в движение вдоль горизонтальной рейки 15 каретку 16 с указателем и карандашом.
С системой зубчатых зацеплений 4–5–6 связан валик 17 (при помощи вспомогательной зубчатой передачи 18). Вращение всех зубчатых передач пропорционально величине опускания захвата 2.
Опускание захвата 3 мало (оно равно вертикальному перемещению конца очень короткого плеча рычага 9), поэтому можно считать, что карандаш 16 отмечает по окружности валика 17 величины, пропорциональные абсолютной деформации образца. Перемещение же карандаша вдоль деревянного валика пропорционально действующей силе.
Порядок пользования машиной ИМ-4Р
Наматывают рулон диаграммной бумаги на нижний валик 19, вращая его по часовой стрелке (если смотреть со стороны маятника). При заправке бумаги на верхний валик 17 его освобождают от сцепления с приводной системой зубчатых колес 18. Закрепив бумагу, включают сцепление валика 17 с зубчатками 18.
Каретку 16 с карандашом ставят в нулевое положение. Прочерчивают координатные оси: ось абсцисс наносится при холостом ходе машины, т. е. при нулевой нагрузке; ось ординат получается при отклонении вручную рычага 14 с кареткой 16 вправо при неподвижном валике 17.
Заправив бумагу, устанавливают в захватах машины образец. Затем вращением рукояти 4 устанавливают нижний захват 2 на такой высоте, что образец оказывается чуть натянутым. Через систему зубчатых передач 21, действующую от мотора 20 на систему 5–6–7, описанную ранее, пускают в ход электромотор. Переключатель от электромотора можно устанавливать в одно из трёх положений: прямой ход, стоп и обратный ход.
Нагружение можно производить также при помощи ручного привода, вращая рукоятку по часовой стрелке (система передач 21 при этом выключается). Разгружение производится вращением рукоятки против часовой стрелки. Нагружение ручным приводом требует больше времени, чем электромотором.
Автоматическую запись кривой иногда прекращают после прохождения участка текучести; если же запись ведётся вплоть до разрушения образца, то в момент разрыва образца из-за быстрого отклонения маятника 12 вправо связанная с ним каретка с пером также быстро передвигается к началу шкалы и попадает там на защёлку 22; одновременно нарушается сцепление рычага 14 с кареткой 16, и дальнейшие качания маятника происходят независимо от каретки, которая, попав на защёлку, остаётся неподвижной.
2.2. Испытание на растяжение-сжатие. Диаграммы испытаний.
Во многих случаях металлические материалы в конструкциях работают под статическими нагрузками. Поэтому для оценки механических свойств широко используются статические испытания, которые проводятся с применением разных схем напряженного состояния в образце. К основным разновидностям статических испытаний относятся испытания на растяжение, сжатие, изгиб и кручение.
Испытание на одноосное растяжение – наиболее распространенный вид испытаний для оценки механических свойств металлов и сплавов – сравнительно легко подвергаются анализу, позволяют по результатам одного опыта определять сразу несколько важных механических характеристик материалов, являющихся критерием его качества и необходимых для конструкторских расчетов.
Методы испытаний на растяжение стандартизованы. Имеются отдельные стандарты на испытания при комнатной температуре (ГОСТ 1497-84), при повышенных до 1473 К (ГОСТ 9651) и пониженных от 273 до 173 К (ГОСТ 11150) температурах.
Для проведения испытаний на растяжение (ГОСТ 1497-84) используют стандартные образцы круглого или прямоугольного сечения, у которых отношение расчетной длины l0 к диаметру поперечного сечения d0 равно десяти (рис.2.5, а). В случае некруглого сечения вместо диаметра принимают . Если по каким-либо причинам изготовить стандартные образцы невозможно, применяют так называемые пропорциональные образцы – меньшего сечения, но с тем же соотношением размеров (табл.2.4). При испытаниях на малых машинах с автоматической записью диаграммы пользуются малыми (кратными) образцами, у которых (рис.2.5, б). Для испытания листовых материалов используют плоские образцы (рис.2.5, в). Во всех случаях на концах образцов имеются головки для захвата их машиной, форма и размеры которых зависят от конструкции приспособлений для захвата. Между рабочей частью и головками образца обеспечиваются плавные переходы размеров. Поверхность рабочей части выполняется ровной, чистой.
Перед испытанием каждый образец маркируют, измеряют и размечают. Маркировку наносят вне пределов рабочей длины образца. Измерение размеров образцов до испытания проводят не менее чем в трех местах - в средней части и на границах рабочей длины. Диаметр цилиндрических образцов следует измерять с точностью не ниже 0,01 при do ≤ 10 мм и 0,05 мм при do < 10 мм. С такой же точностью следует измерять толщину плоских образцов. Для определения начальной площади поперечного сечения F0 необходимые геометрические размеры образцов измеряют с погрешностью не более ±0,5%. За начальную площадь поперечного сечения образца в его рабочей части F0 принимают наименьшее из полученных значений на основании произведенных измерений с округлением по ГОСТ 1497-84. Все размеры после испытаний определяют с точностью не ниже 0,1 мм. Для получения более точных результатов используют инструментальные микроскопы.
Каждый размер следует измерять несколько раз. Например, ГОСТ 1497-84 обязывает производить замер диаметра в середине и по краям рабочей части образца с последующим определением среднего значения, по которому рассчитывают площадь его поперечного сечения.
Рис. 2.5
Образцы для других видов испытаний материалов (сжатие, срез) имеют круглое или прямоугольное (квадратное) постоянное сечение без головок по концам; соотношение расчетной длины и размеров сечения оговаривается ГОСТ 9017-74, 10180-78, 25503-80 и др. (табл.2.1).
Наиболее ценные сведения при изучении характера деформируемости каждого материала можно получить из диаграмм испытания образцов. В процессе его исследования на машине специальным приспособлением записывается диаграмма испытания, связывающая нагрузку P на образец с его продольной деформацией ∆l.
Таблица 2.1.
Типы образцов для испытаний
Материал |
Образец |
Форма образца |
Расчетная Длина l0, мм |
Поперечные размеры, мм |
Растяжение |
||||
Сталь |
Стандартный |
Цилиндр |
100 |
10 |
Короткий |
Произвольная |
|
- |
|
Цилиндр |
50 |
10 |
||
Пропорциональный |
Произвольная |
|
- |
|
Цилиндр |
30 |
6 |
||
Сжатие |
||||
Чугун |
|
Цилиндр |
20 |
30...60 |
Камень |
|
Кубик |
70 |
70 |
Цемент |
|
Кубик |
70 |
70 |
Бетон |
|
Кубик |
100; 150 |
100; 150 |
Кирпич |
|
Параллелепипед |
120 |
120х160 |
По данным, полученным из опытной диаграммы, или же по результатам наблюдений за опытом строят диаграмму растяжений.
Диаграммой растяжения называется график, показывающий функциональную зависимость между нагрузкой и деформацией при статическом растяжении образца до его разрыва.
На рис. 2.6 показан примерный вид параметрической диаграммы растяжения малоуглеродистой стали в координатах: абсолютное удлинение ∆l(t) − нагрузка F(t). В качестве параметра здесь выступает время нагружения, которое для простоты обычно не показывают.
Рис. 2.6. Диаграмма растяжения пластичного материала
На диаграмме растяжения OABCDEG показаны 7 характерных точек, соответствующих определённому уровню нагрузки и ограничивающих 6 различных зон деформирования:
OA – зона пропорциональности (линейной упругости);
AB – зона нелинейной упругости;
BC – зона упругопластических деформаций;
CD – зона текучести (пластических деформаций);
DE – зона упрочнения;
EG – зона закритических деформаций.
Прямолинейный отрезок диаграммы соответствует состоянию материала образца, описываемому законом Гука; наклон прямой OA к оси абсцисс характеризует степень сопротивляемости материала деформированию в упругой стадии, т.е. его жесткость. Точка A соответствует его пределу пропорциональности , т.е. наибольшему напряжению, до которого материал следует закону Гука, которое определяется как отношение силы, при которой эта пропорциональность еще не нарушается, к начальной площади поперечного сечения образца
Точка B соответствует пределу упругости. Под пределом упругости понимается такое наибольшее напряжение, до которого материал не получает остаточных деформаций, т.е. после полной разгрузки последняя точка диаграммы совпадает с начальной точкой 0. Численные значения пределов пропорциональности и упругости получаются очень близкими, поэтому при испытаниях часто ограничиваются определением только предела пропорциональности.
На участке CD, называемом площадкой текучести, происходит лавинообразный выход дислокаций на поверхность, что приводит к значительному удлинению образца при почти постоянном уровне нагрузки, когда . Такое состояние материала названо текучестью.
Ордината точки C на диаграмме соответствует пределу текучести материала образца. Под пределом текучести понимается то напряжение, при котором происходит рост деформаций без заметного увеличения нагрузки и определяется как отношение силы, соответствующей точке C к начальной площади поперечного сечения образца
Если площадка текучести на диаграмме сильно наклонена к оси абсцисс или не совсем прямолинейна, различают верхний и нижний предел текучести. У материалов, не имеющих на диаграмме явно выраженной площадки текучести, принимают условный предел текучести , при котором остаточное удлинение образца ∆l достигает 0,2%.
На участке DE после выхода на поверхность большей части дефектов кристаллической решётки материал самоупрочняется, и образец всё ещё способен воспринимать некоторое приращение нагрузки. Указанный участок диаграммы называется зоной упрочнения. При подходе к т. E деформации начинают локализоваться в области наиболее слабого сечения, где зарождается шейка образца.
Точка E на диаграмме характеризуется наибольшей ординатой,
соответствующей пределу прочности, или временного сопротивления,
материала , т.е. отношению максимальной силы, которую способен выдержать образец, к его начальной площади поперечного сечения
На участке EG заканчивается формирование шейки. Происходит лавинообразное разрушение связей, когда процесс деформирования уже необратим и временное равновесие между внутренними силами и внешней нагрузкой возможно только при уменьшении последней. В т. G происходит разрыв образца. Его размеры восстанавливаются на величину упругой деформации, которая на 2 – 3 порядка меньше остаточных пластических деформаций. У многих материалов разрушение происходит без заметного образования шейки. Сила, соответствующая точке G, называется разрушающей Ffr, а напряжение – истинным сопротивлением разрыву (истинным пределом прочности). Этот предел не имеет особого практического значения и используется только при изучении процесса образования трещин. Разрушающие напряжения делятся на условные и истинные:
условное; истинное,
где - разрушающая нагрузка; - площадь поперечного сечения образца в месте разрыва.
Так как первоначальная площадь приблизительно в два раза превышает площадь разрыва , а разрушающая нагрузка составляет приблизительно 80 % от наибольшей нагрузки , то
Например, для низкоуглеродистой стали Ст3 = 380 МПа; =800...1000 МПа.
Истинное напряжение в месте разрыва образца к моменту его разрыва наиболее полно характеризует силу взаимодействия между частицами перед их отрывом друг от друга. Причем отрыв частиц происходит по центральной части поперечного сечения шейки, остальная часть скалывается под углом 450, с образованием по периметру сечения характерного венчика (рис.19, а). Такая форма разрушения наблюдается только у пластичных материалов.
Рис. 2.7
Рассмотренные выше пределы пропорциональности и упругости характеризуют упругие свойства материала. Пределы текучести и прочности являются характеристиками прочности материала. Пластичность материала оценивают относительными остаточными деформациями, накопленными образцом до его разрушения:
относительным остаточным удлинением
и относительным остаточным сужением ψ площади сечения образца при разрыве
где l0 и A0 начальные длина и площадь сечения образца; l1, A1- длина и площадь сечения образца, измеренные после его разрушения.
Сложенные части разорванного образца из пластичного материала длиннее исходного на величину остаточной деформации. Упругая часть деформации при разрушении образца исчезает. О ее величине можно судить по диаграмме (см. рис. 2.6), если спроецировать точку G на ось абсцисс по направлению линии OA (точка H). Наличие в материале упругих деформаций при его работе за пределом упругости подтверждается в опытах наклоном линии к оси абсцисс, которая появится на диаграмме, если в процессе опыта прекратить нагружение и произвести разгрузку образца с той же скоростью. После исчезновения упругой деформации образец окажется удлиненным на величину остаточной деформации.
Повторное нагружение разгруженного образца позволяет получить укороченную диаграмму, являющуюся продолжением начального участка полной диаграммы. Линия повторного загружения практически совпадает с линией разгрузки. Аналогичная картина наблюдается при разгрузке и повторном загружении образца для любой точки, выбранной на участке BG диаграммы.
Укороченная диаграмма характерна для образцов, изготовленных из материала, в результате холодной обработки (ковки, штамповки, вытяжки) получившего деформационное или механическое упрочнение или наклеп (упрочнение материала). Модуль упругости материала при этом практически не изменится, точки A и B на укороченной диаграмме окажутся намного выше, площадка текучести исчезнет. Это означает, что при наклепе повышаются прочностные свойства материала, но снижаются свойства пластичности и он становится ближе к хрупким материалам, у которых диаграмма испытаний очень короткая, так как образцы разрушаются при весьма малых остаточных деформациях.
Наклеп наблюдается не у всех материалов и даже не у всех металлов, таких, например, как свинец, олово и др. Явление наклепа широко используют в технике – упрочняют детали, подвергая их при изготовлении пластическому деформированию. Например, цепи и канаты подъемных машин подвергают предварительной вытяжке, чтобы устранить остаточные удлинения, которые могут возникнуть во время их работы. Аналогичной обработке подвергают также некоторые виды арматуры железобетонных конструкций, цилиндры гидравлических прессов, турбинные диски, пружины и другие элементы машин и механизмов.
Следует заметить, что после предварительной вытяжки металла в некотором направлении его механические свойства изменяются (металл наклепывается) при работе на растяжение только в том же направлении; при работе на сжатие в этом же направлении его свойства почти не изменяются. Последнее обстоятельство имеет большое значение для материала, который подвергается действию переменных напряжений.
В зависимости от характеристик пластичности материалы подразделяют на пластичные и хрупкие. К хрупким относят материалы с малым относительным остаточным удлинением при разрыве ( ), например чугун, бетон, стекло. Диаграмма растяжения хрупких материалов, например чугуна, не имеет площадки текучести. Для хрупких материалов при испытании на растяжение определяют в основном только предел прочности . Образец из хрупких материалов разрушается без образования шейки и зон сдвига. В результате отрыва частиц на нем появляется поперечная трещина, способствующая мгновенному разрушению (рис.2.7, б). На поверхности излома видна крупнозернистая структура материала.
Деление материалов на пластичные и хрупкие вообще условно, так как механические свойства их зависят от состояния, обусловленного условиями эксплуатации. Пластичные материалы при низких температурах разрушаются хрупко, а хрупкие при высоких давлениях проявляют незаурядные свойства пластичности.
Для испытаний на сжатие изготавливают короткие образцы: для металлов - цилиндры с отношением высоты к диаметру в пределах 1,5...3, для других материалов - кубики (см. табл.2.1 и рис. 2.8). Применение более длинных образцов недопустимо, так как такие образцы могут искривляться и тем самым искажать результаты испытаний. Следует обратить внимание на некоторую условность получаемых результатов из-за наличия сил трения в опорных поверхностях образца. Поэтому стараются ослабить влияние сил трения введением различных смазок (вазелин, солидол) и прокладок (тефлон, пропитанная парафином фильтровальная бумага) между торцовыми поверхностями образца и опорными плитами или использованием подкладок и образцов с конической поверхностью на торцах (рис. 2.8, в). Углы конусности α подбирают так, чтобы tgα был равен коэффициенту трения. Помимо конусности, в образце делают центральное отверстие, устраняющее концентрацию напряжений у острия конуса (рис. 2.8, г).
Но полностью устранить контактные силы трения и обеспечить в течение всего испытания линейное напряженное состояние в образце не удается. Это принципиальный недостаток испытаний на сжатие.
Для определения модуля нормальной упругости при сжатии, пределов упругости и пропорциональности иногда используют плоские образцы в виде пластин толщиной 2-5 мм, длиной 100 и шириной 20 мм. Они испытываются в специальных приспособлениях, обеспечивающих их продольную устойчивость.
Рис. 2.8.
Рис. 2.9. Образцы для испытаний на сжатие
Испытание на сжатие осуществляется обычно при помощи тех же испытательных машин с применением специальных приспособлений (реверсоров).
Образец закладывается между плитами испытательной машины и постепенно нагружается непрерывно возрастающей нагрузкой. При этом на диаграммном барабане машины вычерчивается диаграмма сжатия (рис. 10).
Скорость относительной деформации выбирают:
до предела текучести от 10-3 с-1 до 10-2 с-1,
за пределом текучести - не более 10-1 с-1,
для построения кривых упрочнения от 10-3 с-1 до 10-1 с-1.
Рис. 2.10. Диаграммы сжатия различных материалов
Результаты испытаний на сжатие зависят от условий проведения эксперимента. Практически очень трудно добиться приложения сжимающей силы точно по оси образца. Поэтому образец будет не только сжиматься, но и изгибаться. Чем длиннее образец, тем больше влияние изгиба (попробуйте сжать длинный и тонкий прутик). Для уменьшения влияния изгиба рекомендуется применять образцы, длина которых не более чем в два раза превышает их поперечные размеры. Применение слишком коротких образцов тоже нежелательно. При сжатии образца продольные размеры уменьшаются, а поперечные увеличиваются (по закону Пуассона).
Для пластичного материала (медь) диаграмма сжатия (рис. 2.10) до предела текучести совпадает с диаграммой растяжения, однако ярко выраженной площадки текучести не наблюдается. После прохождения стадии текучести происходит быстрое возрастание деформаций, а увеличивающееся поперечное сечение образца становится способным выдержать все большую нагрузку. Образец принимает бочкообразную форму из-за наличия сил трения на торцах (рис.2.9, а) и может быть сплющен в тонкую пластинку без признаков разрушения, иногда даже без образования трещин. Поэтому в процессе испытания обычно определяют только предел пропорциональности.
Образец нагружают непрерывно до напряжения, превышающего ожидаемое значение предела пропорциональности . Предел пропорциональности определяют по диаграмме (рис.23) и используя формулу:
Рис. 2.11. Диаграмма испытаний для определения предела пропорциональности при сжатии
ВОПРОСЫ ДЛЯ САМОПРОВЕРКИ
- Для чего необходимо знать механические характеристики материала?
- Какие виды испытаний материалов применяются на практике?
- Какая испытательная техника используется для испытания материалов?
- Какие характерные точки имеет диаграмма растяжения стали?
- Что называется пределом пропорциональности, пределом упругости, пределом текучести и пределом прочности?
- Какое явление называют текучестью?
- Что такое «шейка», в какой точке диаграммы растяжения она образуется?
- В чем различия между упругими и пластичными деформациями?
- Перечислите характеристики прочности?
- Перечислите характеристики пластичности?
- Назовите все характеристики прочности материала. Сколько их?
- Какие материалы считаются хрупкими?
- Что называется модулем продольной упругости Е? Как сказывается величина Е на деформации бруса?
- Как формулируется закон Гука?
- Что называют коэффициентом Пуассона и в каких пределах он принимает значения для различных материалов?
- Какое явление называют “наклёпом” (нагартовкой)?
- Что называют упругостью, пластичностью, ползучестью?
- Чем отличаются диаграммы растяжения и сжатия для пластичных материалов?
- Чем отличаются диаграммы растяжения и сжатия для хрупких материалов?
- Какие материалы называют анизотропными?
- Какая из механических характеристик выбирается в качестве предельного напряжения для пластичных и хрупких материалов?
- В чем различие между предельным и допускаемым напряжениями?
- Что называется относительной продольной и относительной поперечной деформацией? Для чего они определяются?
- Можно ли определить модуль упругости Е по диаграмме растяжения?
- Что понимается под наклепом материала?
- Что выражает собой площадь диаграммы растяжения?
- Что представляет собой коэффициент запаса прочности, с какой целью и как его назначают?
3. Осевое растяжение – сжатие.
3.1. Продольные силы в поперечных сечениях
Под растяжением (сжатием) понимают такой вид нагружения, при котором в поперечных сечениях стержня возникают только продольные силы N, а прочие силовые факторы (поперечные силы, крутящий и изгибающий моменты) равны нулю.
Это самый простой и часто встречающийся вид деформации. Обычно он наблюдается когда внешняя нагрузка действует вдоль продольной оси стержня. Продольной осью стержня называется линия, проходящая через центры тяжести поперечных сечений.
Обычным является растяжение стержня силами, приложенными к его концам. Передача усилий к стержню может быть осуществлена различными способами, как это показано на рис. 3.1.
Рис. 3.1
Во всех случаях, однако, система внешних сил образует равнодействующую F, направленную вдоль оси стержня. Поэтому независимо от условий крепления растянутого стержня, расчетная схема в рассматриваемых случаях (рис. 3.1, а, б) оказывается единой (рис. 3.1, в) согласно принципу Сен – Венана.
Если воспользоваться методом сечений (рис. 3.2), то становится очевидным, что во всех поперечных сечениях стержня возникают нормальные силы Nz, равные силе F (рис. 3.2, б).
Сжатие отличается от растяжения, формально говоря, только знаком силы Nz. При растяжении нормальная сила Nz направлена от сечения (рис. 3.2, б), а при сжатии – к сечению.
Рис. 3.2
Растягивающие продольные силы принято считать положительными (рис. 3.3, а), а сжимающие – отрицательными (рис. 3.3, б).
Рис. 3.3
При расчете стержней, испытывающий деформацию растяжения, на прочность и жесткость при статическом действии нагрузки, надо решить две основные задачи. Это определение напряжений (от Nz), возникающих в стержне, и нахождение линейных перемещений в зависимости от внешней нагрузки.
Продольные силы (Nz), возникающие в поперечных сечениях стержня, определяются по внешней нагрузке с помощью метода сечений.
График, показывающий изменение продольных сил по длине оси стержня, называется эпюрой продольных сил (эп. Nz). Он дает наглядное представление о законе изменения продольной силы.
Осью абсцисс служит ось стержня. Каждая ордината графика – продольная сила (в масштабе сил) в данном сечении стержня.
Эпюра позволяет определить, в каком сечении действует максимальное внутреннее усилие (например, найти Nmax при растяжении-сжатии). Сечение, где действует максимальное усилие будем называть опасным.
Перед построением эпюр необходимо освободить брус, в котором будем строить эпюры от опорных связей (выделить объект равновесия) и приложить к нему все действующие внешние силы (активные и реактивные). Затем необходимо установить границы участков, в пределах которых закон изменения внутренних сил постоянный. Границами таких участков являются сечения, где приложены сосредоточенные силы или начинается и кончается распределенная нагрузка, а также сечения, где имеется перелом стержня.
Применяя метод сечений и учитывая правила знаков изложенные выше, получаем уравнения изменения внутренних сил в пределах длины каждого участка бруса. Затем, используя, полученные зависимости строим графики (эпюры) этих усилий. Ординаты эпюр в определенном масштабе откладываем от базисной линии, которую проводим параллельно оси бруса.
Рассмотрим стержень постоянного поперечного сечения, жестко защемленный правым концевым сечением и нагруженный заданной внешней сосредоточенной нагрузкой F и распределенной q (рис. 3.4, а).
Прежде всего определим опорную реакцию R1, задавшись ее направлением вдоль оси z.
ΣFz=0, -R1 - 22 + 24∙0,6 = 0, R1= -7,6 кН.
Знак минус говорит о том, что действительное направление опорной реакции R1 противоположно показанному на рис. 3.4, а. Исправляем его и в дальнейших расчетах знак минус у опорной реакции R1 не учитываем (рис. 3.4, в, г).
Под участком будем понимать часть стержня, на которой Nz представляется некоторым аналитическим выражением. На другом участке Nz будет определяться другой функцией.
Границами участка являются начало и конец стержня, сечения, где приложены сосредоточенные нагрузки, начинается и заканчивается распределенная нагрузка.
В нашем случае стержень разбивается на два участка. В пределах первого участка мысленно рассечем стержень на две части нормальным сечением (рис. 3.4, б, в).
Рис. 3.4
Направления продольных сил (рис. 3.4, б – г) приняты в предположении, что они являются растягивающими (т. е. положительными). Если в результате расчета значение Ni получится со знаком «минус», то это будет означать, что в действительности стержень в этом сечении сжат.
Поскольку обе части стержня являются равноправными, то N1 на первом участке в сечении, определяемом координатой z1, можно определить рассматривая равновесие его правой (рис. 3.4, б) либо левой (рис. 2.4, в) частей.
В нашем случае для определения N1 предпочтительнее рассмотреть равновесие правой части – к ней приложено меньше сил (рис. 3.4, б). Начало координат совмещаем с правым концевым сечением первого участка. Ось z направляем налево. Пределы изменения положения сечения вдоль продольной оси 0≤z1≤0,6 м. Спроектируем все силы, действующие на правую часть, на продольную ось.
ΣFz=0, N1 - 24∙z1 = 0, N1 =24∙z1, N1(0)= 0, N1(0,6)= 14,4 кН.
Поскольку функция N1 =24∙z1 получилась линейная, то для построении графика ее изменения вдоль продольной оси (эп. Nz) достаточно вычислить значения продольной силы на границах первого участка, отложить их перпендикулярно продольной оси вверх (стержень растянут) и провести через них прямую линию (рис. 3.4, д).
Таким образом, в пределах первого участка стержень растянут и нормальная сила изменяется по линейному закону.
Этот же результат можно получить, рассматривая равновесие левой части стержня.
Здесь при выборе системы координат рассмотрим два варианта. При первом варианте начало координат совмещаем с левым концевым сечением второго участка. Ось z направляем направо. Пределы изменения положения сечения вдоль продольной оси 0,4 м≤ ≤1,0 м. Спроектируем все силы, действующие на левую часть, на продольную ось.
ΣFz=0, N1 +7,6 – 22 + 24∙( - 0,4)= 0, N1 =24- 24∙ , N1(0,4)= 14,4 кН, N1(1,0)= 0.
Во втором варианте введем скользящую систему координатных осей. Начало координат совмещаем с левым концевым сечением первого участка. Ось z направляем направо. Пределы изменения положения сечения вдоль продольной оси 0≤ ≤0,6 м. Имеем
ΣFz=0, N1 +7,6 – 22 + 24∙ = 0, N1 =14,4- 24∙ , N1(0)= 14,4 кН, N1(0,6)= 0.
Заметим, что при выборе скользящей системы координат, функция N1=f(z, q) меняется от нуля, что делает последующие расчеты менее трудоемкими.
Сравнивая все три варианта определения N1, приходим к выводу, что когда мы оставляем ту часть стержня, к которой приложено меньше внешних нагрузок, то расчеты оказываются более простыми.
При некотором навыке можно сразу составить выражение для N1, не изображая отдельные части бруса, на которые он расчленяется поперечными сечениями (рис. 3.4, б, в). Например,
при 0≤z1≤0,6 м, N1 =24∙z1;
при 0,4 м≤ ≤1,0 м, N1 =7,6 + 22 - 24∙( -0,4);
при 0≤ ≤0,6 м, N1 = -7,6 + 22 - 24∙ .
Таким образом, на основании метода сечений продольная сила в произвольном поперечном сечении стержня численно равна алгебраической сумме проекций внешних сил, приложенных к стержню по одну сторону от рассматриваемого сечения, на его продольную ось.
Причем проекция внешней силы берется со знаком плюс, если сила растягивает часть стержня от точки ее приложения до рассматриваемого сечения и, наоборот, со знаком минус – если сжимает.
Осталось определить значение продольной силы N2 в произвольном сечении, определяемом координатой z2, на втором участке (рис. 3.4, г). Так как продольная сила N2 численно равна алгебраической сумме внешних сил, приложенных к стержню слева от сечения (рассматриваем равновесие левой части стержня), то N2= -7,6 кН (реакция R1=7,6 кН сжимает часть стержня длиной z2). Здесь принимаем скользящую систему координат, с началом в левом концевом сечении второго участка. Ось z направляем направо.
Эпюра Nz на втором участке представлена на рис 3.4, д в виде прямоугольника со знаком минус, поскольку N2= -7,6 кН =const. Таким образом, в пределах второго участка стержень претерпевает сжатие постоянной нормальной силой.
Каждая ордината эп. Nz (рис. 3.4, д) в принятом масштабе равна величине продольной силы, действующего в том поперечном сечении стержня, которому соответствует эта ордината.
Видно, что на участке между точками приложения сосредоточенных сил R1 и F продольная сила имеет постоянное значение, а на участке, где приложена распределенная внешняя нагрузка, меняется по линейному закону (рис. 3.4, д).
Характерно, что скачки на эп. Nz обусловлены наличием в соответствующих сечениях сосредоточенных сил R1 и F.
3.2. Напряжение в поперечных сечениях стержня
Нормальная сила N приложена в центре тяжести сечения, является равнодействующей внутренних сил в сечении и, в соответствии с этим, определяется следующим образом:
Но из этой формулы нельзя найти закон распределения нормальных напряжений в поперечных сечениях стержня. Для этого обратимся к анализу характера его деформирования.
Если на боковую поверхность этого стержня нанести прямоугольную сетку (рис. 3.2, б), то после нагружения поперечные линии аа, bb и т.д. переместятся параллельно самим себе, откуда следует, что все поверхностные продольные волокна удлинятся одинаково. Если предположить также, что и внутренние волокна работают таким же образом, то можно сделать вывод о том, что поперечные сечения в центрально растянутом стержне смещаются параллельно начальным положениям, что соответствует гипотезе плоских сечений (гипотезе Бернулли).
Значит, все продольные волокна стержня находятся в одинаковых условиях, а следовательно, нормальные напряжения во всех точках поперечного сечения должны быть также одинаковы и равны
где A площадь поперечного сечения стержня.
В сечениях, близких к месту приложения внешних сил, гипотеза Бернулли нарушается: сечения искривляются, и напряжения в них распределяются неравномерно. По мере удаления от сечений, в которых приложены силы, напряжения выравниваются, и в сечениях, удаленных от места приложения сил на расстояние, равное наибольшему из размеров поперечного сечения, напряжения можно считать распределенными по сечению равномерно. Это положение, называемое принципом Сен-Венана, позволяет при определении напряжений в сечениях, достаточно удаленных от мест приложения внешних сил, не учитывать способ их приложения, заменять систему внешних сил статически эквивалентной системой. Например, экспериментально установлено, что во всех трех случаях нагружения стержня (рис. 3.7, а) значения напряжений в сечениях, удаленных от крайних сечений на расстояние не менее высоты сечения h, одинаковы: (рис. 3.7, б), а в сечениях, близких к местам приложения внешних сил, распределения напряжений по сечению существенно различны (рис. 3.7, в).
Рис. 3.7
Высказанное предположение о равномерном распределении нормальных напряжений в поперечном сечении справедливо для участков, достаточно удаленных от мест: резкого изменения площади поперечного сечения (рис. 3.7, в); скачкообразного изменения внешних нагрузок; скачкообразного изменения физико-механических характеристик конструкций.
Нормальные напряжения при сжатии определяют так же, как и при растяжении, но считают отрицательными.
Следует помнить, что длинные (тонкие) стержни, нагруженные сжимающими силами, могут потерять устойчивость. Расчет стержней на устойчивость рассмотрен в разделе «Устойчивость».
В инженерных сооружениях встречаются растянутые или сжатые элементы, имеющие отверстия. В сечениях с отверстием определяют осредненные нормальные напряжения по формуле
где площадь поперечного сечения нетто; A - площадь поперечного сечения брутто; - площадь его ослабления.
Деформации и перемещения. Закон Гука
Рассмотрим однородный стержень с одним концом, жестко заделанным, и другим - свободным, к которому приложена центральная продольная сила Р (рис. 3.8). До нагружения стержня его длина равнялась l - после нагружения она стала равной (рис. 2.8). Величину называют абсолютной продольной деформацией (абсолютным удлинением) стержня. В большинстве случаев оно мало по сравнению с его первоначальной длиной l (∆l<<l).
Рис. 3.8
Если в нагруженном стержне напряженное состояние является однородным, т.е. все участки стержня находятся в одинаковых условиях, деформация остается одной и той же по длине стержня и равной
Величина ε называется относительной продольной деформацией.
Если же по длине стержня возникает неоднородное напряженное состояние, то для определения его абсолютного удлинения необходимо рассмотреть бесконечно малый элемент длиной dz (рис. 3.8). При растяжении он увеличит свою длину на величину и его деформация составит:
В пределах малых деформаций при простом растяжении или сжатии закон Гука записывается в следующем виде (нормальные напряжения в поперечном сечении прямо пропорциональны относительной линейной деформации ):
Величина Е представляет собой коэффициент пропорциональности, называемый модулем упругости материала первого рода (модуль продольной упругости). Его величина постоянна для каждого материала. Он характеризует жесткость материала, т.е. способность сопротивляться деформированию под действием внешней нагрузки.
Из совместного рассмотрения уравнений (2.5) и (2.6) получим:
откуда с учетом того, что
окончательно получим:
Если стержень изготовлен из однородного изотропного материала с Е = const, имеет постоянное поперечное сечение A = const и нагружен по концам силой Р, то из (2.7) получим
Зависимость (2.8) также выражает закон Гука. Знаменатель EA называется жесткостью при растяжении - сжатии или продольной жесткостью.
При решении многих практических задач возникает необходимость, наряду с удлинениями, обусловленными действием механических нагрузок, учитывать также удлинения, вызванные температурным воздействием. В этом случае пользуются принципом независимости действия сил, и полные деформации рассматривают как сумму силовой и температурной деформаций:
где коэффициент температурного расширения материала; t перепад температуры тела. Для однородного стержня, нагруженного по концам продольными силами Р и равномерно нагретого по длине, получим:
Потенциальная энергия деформации
Внешние силы, приложенные к упругому телу и вызывающие изменение геометрии тела, совершают работу W на соответствующих перемещениях. Одновременно с этим в упругом теле накапливается потенциальная энергия его деформирования U. При действии динамических внешних нагрузок часть работы внешних сил превращается в кинетическую энергию движения частиц тела К. Приняв энергетическое состояние системы до момента действия данных сил равным нулю, и в условиях отсутствия рассеивания энергии, уравнение баланса энергии можно записать в следующем виде:
W = U + K. (2.11)
При действии статических нагрузок К = 0, следовательно,
W = U. (2.12)
Это означает, что при статическом нагружении работа внешних сил полностью преобразуется в потенциальную энергию деформации. При разгрузке тела производится работа за счет потенциальной энергии деформации, накопленной телом. Таким образом, упругое тело является аккумулятором энергии. Это свойство упругого тела широко используется в технике, например, в заводных пружинах часовых механизмов, в амортизирующих рессорах и др. В случае простого растяжения (сжатия) для вывода необходимых расчетных зависимостей потенциальной энергии деформации рассмотрим решение следующей задачи.
На рис. 3.9, а изображен растягиваемый силой Р стержень, удлинение которого соответствует отрезку , ниже показан график изменения величины удлинения стержня в зависимости от силы Р (рис. 3.9, б). В соответствии с законом Гука этот график носит линейный характер.
Пусть некоторому значению силы Р соответствует удлинение стержня . Дадим некоторое приращение силе соответствующее приращение удлинения составит . Тогда элементарная работа на этом приращении удлинения составит:
Рис. 3.9
вторым слагаемым, в силу его малости, можно пренебречь, и тогда
Полная работа равна сумме элементарных работ, тогда, при линейной зависимости “нагрузка перемещение”, работа внешней силы Р на перемещении будет равна площади треугольника ОСВ (рис. 3.9), т.е.
В свою очередь, когда напряжения и деформации распределены по объему тела V равномерно (как в рассматриваемом случае) потенциальную энергию деформирования стержня можно записать в виде:
Поскольку, в данном случае имеем, что , то
т.е. подтверждена справедливость (2.12).
С учетом (2.8) для однородного стержня с постоянным поперечным сечением и при Р = const из (2.17) получим:
Единицей измерения потенциальной энергии деформации является 1Hм = 1Дж.
3.3. Расчеты на прочность и жесткость при растяжении-сжатии.
Основной задачей расчета конструкции является обеспечение ее безопасной эксплуатации. Важнейшим условием, обеспечивающим безопасную эксплуатацию конструкции, является условие прочности. Существуют различные методы обеспечения прочности конструкций. Мы чаще всего будем пользоваться одним из этих методов – расчетом по допускаемым напряжениям. Согласно этому методу для конструкций, работающих на растяжение-сжатие, условие прочности, составленное для опасного сечения, можно записать в таком виде:
где – максимальное напряжение в конструкции; – характеристика материала, называемая допускаемым напряжением.
Допускаемое напряжение находится по формуле
где – предельное напряжение, при достижении которого в стержне наступает предельное состояние материала: появляются пластические деформации, если материал стержня – пластичный, или происходит разрушение, если стержень выполнен из хрупкого материала; n – нормируемый коэффициент запаса прочности.
Кроме формулы (2.26), возможен второй вариант условия прочности
называется действительным коэффициентом запаса прочности, показывающим во сколько раз надо увеличить максимальное напряжение в стержне, чтобы материал стержня оказался в опасном (предельном) состоянии.
Условие прочности в зависимости от цели поставленной задачи позволяет выполнять расчеты на прочность двух видов: проектный и проверочный. Для спроектированного стержня можно также определять допускаемую нагрузку.
Проектный расчет выполняют с целью определения размеров поперечных сечений элемента конструкции при известных рабочих нагрузках и материале (допускаемых напряжений). Площадь поперечного сечения определяют из выражения
Форма сечения стержня не влияет на его прочность при растяжении (сжатии). Форму сечения стержня необходимо знать только для определения размеров сечения при известном значении площади.
Зная площадь сечения и его форму, находят размеры сечения.
Проверочный расчет выполняют для спроектированной конструкции с целью проверки ее прочности. При проверочном расчете должны быть известны площадь опасного сечения, нагрузка и материал (допускаемое напряжение). Проверочный расчет выполняют по формуле (2.26).
Определение допускаемой нагрузки для спроектированного элемента конструкции, размеры поперечного сечения которого и материал (допускаемые напряжения) известны. Условие прочности в этом случае записывают в виде
Зная значение , определяют допускаемую нагрузку .
Так как допускаемые напряжения не имеют точного значения, а выбираются приближенно, то при проверочном расчете максимальные рабочие напряжения могут превышать допускаемые на 5%. По этой же причине можно округлять полученные в расчетах значения площади опасного поперечного сечения или допускаемой нагрузки так, чтобы максимальные напряжения отличались от допускаемых не более чем на 5%. По этой же причине можно округлять полученные в расчетах значения площади опасного поперечного сечения или допускаемой нагрузки та, чтобы максимальные напряжения отличались от допускаемых не более чем на 5%.
При проектировании элементов конструкций стремятся сделать их во всех сечениях равнопрочными.
Рассмотренные три вида расчетов на прочность можно выполнять не только при растяжении или сжатии, а при любом виде деформации (сдвиге, кручении, изгибе).
При проектировании строительных конструкций расчет на прочность стальных элементов, подверженных центральному растяжению или сжатию, следует выполнять по формуле
где – коэффициент условий работы, принимаемый по СНИП (см. табл. 3.1) или другим нормам.
Таблица 3.1
Элементы конструкции |
|
Колонны общественных зданий и опор водонапорных башен Элементы стержневых конструкций покрытий и перекрытий: а) сжатых при расчетах на устойчивость б) растянутых в сварных конструкциях Сплошные составные балки, колонны, несущие статическую нагрузку и выполненные с помощью болтовых соединений, при расчетах на прочность Сечения прокатных и сварных элементов, несущих статическую нагрузку, при расчетах на прочность Сжатые элементы из одиночных уголков, прикрепляемые одной полкой |
0,95
0,95 0,95
1,1
1,1 0,75 |
Примечание: В случаях, не оговоренных в настоящих нормах, в формулах следует принимать . |
Для хрупких строительных материалов условия прочности принимают вид:
при растяжении:
при сжатии:
где и – допускаемые напряжения при растяжении и сжатии; nt и nc – нормативные коэффициенты запаса прочности по отношению к пределу прочности (nt, nc>1).
Для центрально сжатых бетонных элементов формула (2.33) записывается в виде:
где – коэффициент, принимаемый для бетона тяжелого, мелкозернистого и легкого равным 1,00; для ячеистого автоклавного – 0,85; для ячеистого неавтоклавного – 0,75.
В некоторых случаях работоспособность элемента конструкции определяется не только его прочностью, но и жесткостью, т.е. способностью элемента воспринимать нагрузки без недопустимых упругих деформаций. При расчетах на жесткость определяют максимальные перемещения сечений и сопоставляют их с допускаемыми перемещениями.
Условие жесткости, ограничивающее изменение длины элемента, имеет следующий общий вид:
где - изменение размеров детали;
[ ] - допускаемая величина этого изменения.
Учитывая, что при растяжении (сжатии) абсолютное удлинение в общем виде определяется как алгебраическая сумма величин по участкам
условие жесткости при растяжении (сжатии) запишем следующим образом:
Так как перемещение, согласно закону Гука, зависит от нагрузки и размеров поперечного сечения, условие жесткости позволяет решать те же три вида задач, что и условие прочности.
3.4. Расчеты статически определимых стержней
Статически определимый стержень – это стержень, который можно рассчитать, используя только уравнения равновесия (уравнения статики).
В любой науке, которая называется «точной» и в которой используются аналитические методы описания состояний и явлений, не обойтись без моделей. В нашем случае при решении различных задач мы каждый раз будем выбирать для рассматриваемого объекта расчетную схему.
Расчетная схема – это упрощенная схема конструкции или ее элементов, освобожденная от несущественных в данной задаче особенностей. При этом расчетная схема должна отражать все наиболее существенное для характера работы данной конструкции и не содержать второстепенных факторов, мало влияющих на результаты ее расчета. Построение и обоснование расчетной схемы – ответственный этап проектирования и расчета конструкции.
Перейдем к рассмотрению конкретных примеров.
Пример 5.
Чугунная труба-стойка высотой H=l=3м с наружным диаметром D=25 см и внутренним диаметром d=20 см нагружена сжимающей силой F=50 т, модуль упругости чугуна . Найти напряжение в поперечном сечении колонны, абсолютное и относительное укорочения .
Решение.
Как уже говорилось выше, решение задачи начинается с выбора расчетной схемы. В данном случае стойка изображается как вертикальный стержень длиной H=l=3м, жестко закрепленный в нижней части (условное изображение фундамента или земли). К верхней части стержня приложена сосредоточенная сжимающая сила (направление к стержню). При этом линия действия силы должна совпадать с осью стержня. Кроме того, рядом необходимо изобразить поперечное сечение стойки с указанием основных размеров. В данном примере – это кольцо. Расчетная схема для решения задачи изображена на рис. 3.10, а.
Далее строим эпюру продольной силы и определяем максимальное внутреннее усилие, возникающее в колонне. Поскольку внешняя нагрузка постоянна по высоте, то возникает только одна сжимающая
продольная сила
Рис. 3.10
Максимальное нормальное напряжение определяется по формуле:
где A [м2] – площадь трубы:
тогда:
Абсолютное и относительное укорочения стойки определяем по формулам:
Знак "минус" обозначает уменьшение размера (укорочение).
3.5. Понятие о статически неопределимых системах
Основные положения. Связи необходимые и дополнительные.
Для решения задач сопротивления материалов необходимо знать все внешние силы, действующие на конструкцию, включая реакции наложенных на нее связей. Из теоретической механики известно, что для равновесия твердого тела, нагруженного плоской системой сил, достаточно наложить на тело три связи, а нагруженного пространственной системой сил – шесть связей. Соответственно для таких систем можно составить три и шесть независимых уравнений равновесия. Если при рассмотрении заданной системы, находящейся в равновесном состоянии от действия заданных внешних нагрузок, все реакции в связях закрепления можно определить с помощью уравнений равновесия, без использования дополнительных условий, то такая система называется статически определимой.
В реальной практике встречаются такие конструкции, при расчете которых одних лишь уравнений равновесия оказывается недостаточно, в связи с чем требуется формулирование дополнительных уравнений, связанных с условиями деформирования конструкции.
Системы, в которых количество наложенных связей больше, нежели число независимых уравнений равновесия, называются статически неопределимыми.
В машиностроении и строительных конструкциях такие системы находят широкое применение. В одних случаях статическая неопределимость является сущностью самой конструкции.
Рис. 3.11.
Примерами таких конструкций могут быть: армированные уголками стойки (рис.3.11, а); панель крыла самолета, состоящая из обшивки 1 с продольными ребрами 2 (рис. 3.11, б); составной цилиндр, полученный путем напряженной посадки двух труб из различных материалов (рис. 3.11, в). В других случаях, с целью повышения жесткости и надежности системы, вводятся дополнительные связи сверх тех минимально необходимых, которые обеспечивают ее кинематическую неизменяемость. Наложение на систему дополнительных связей превращает ее в статически неопределимую. Напомним, что кинематическая неизменяемость плоской системы обеспечивается тремя, а пространственной – шестью связями.
Конструкции, состоящие из стержней, соединенных шарнирами, называются шарнирно-стержневыми. В этих конструкциях есть стержни, которые обеспечивают геометрическую неизменяемость конструкции и при удалении которых система превращается в механизм. Такие стержни будем называть необходимыми. Если же при удалении некоторых стержней геометрическая неизменяемость конструкции не нарушается, то такие стержни назовем лишними. Лишними такие связи называются только потому, что они не являются необходимыми для обеспечения равновесия конструкции и ее геометрической неизменяемости, хотя постановка их диктуется условиями эксплуатации. По условиям прочности и жесткости конструкции лишние связи могут оказаться необходимыми.
В статически определимой системе есть только необходимые стержни, в статически неопределимой – число лишних стержней равно степени статической неопределимости.
а) б) в)
Рис. 3.12
На рис. 3.12 приведены схемы 3-х плоских систем с «лишними» связями: а – стержневой подвески; б – стержня, закрепленного обоими концами; в – стержневого кронштейна. В схеме, показанной на рис. 3.12, в, вся система состоит из упругих звеньев. Подсчет числа наложенных связей производится в этом случае следующим образом. Каждый стержень связан с опорной поверхностью двумя связями. Всего таких связей 8. Шарнир, соединяющий концы стержней, снимает связи, ограничивающие относительный или взаимный их поворот. При соединении двух стержней одним шарниром снимается одна связь, трех стержней – две связи, четырех – три и т.д. В данном случае снимаются три связи. Следовательно, всех связей, наложенных на эту систему оказывается пять, две из которых могут считаться «лишними».
Статически неопределимые конструкции характеризуются рядом особенностей, по сравнению со статически определимыми системами. Заключаются они в том, что в элементах статически неопределимых систем напряжения возникают не только от действия внешних сил, но и в результате изменения температуры, неточности изготовления деталей, неточностей их сборки, смещения мест опорных креплений и ряда других причин. Объясняется это тем, что деформация одного из элементов в статически неопределимой системе приводит к деформации и других ее элементов.
Например, если один из стержней системы (рис. 3.12, в) изготовлен по длине неточно, то соединение концов стержней одним шарниром возможно только путем деформации всех стержней.
Сила, возникающая при деформации одного из стержней, вызывает усилия в других стержнях, находящихся с ним в шарнирном соединении. Смонтированная система приходит в равновесие, следовательно, совокупность сил системы обеспечивает ее равновесие. Эти силы вызывают соответствующие, называемые начальными, напряжения в стержнях.
В статически неопределимых конструкциях при изменении температуры ее элементов по сравнению с температурой, при которой осуществлялась сборка, возникают дополнительные усилия и напряжения, которые принято называть температурными.
Распределение усилий между элементами системы зависит от их жесткости. Если увеличить жесткость какого- либо элемента, то он примет на себя большее усилие. Изменяя соотношение жесткостей элементов конструкций, можно менять распределение усилий между ними.
Эти особенности статически неопределимых конструкций должны учитываться при проектировании или применении таких систем.
Статически неопределимые системы обладают повышенной «живучестью». Разрушение одного или нескольких элементов (в зависимости от числа дополнительных связей) не вызывает потерю несущей способности конструкции в целом. Так разрушение даже двух стержней в системе, показанной на рис. 3.12, в не приводит к потере способности воспринимать силу P оставшимися двумя стержнями, конечно, при условии их достаточной прочности.
ВОПРОСЫ ДЛЯ САМОПРОВЕРКИ
- Что называется стержнем?
- Какой вид нагружения стержня называются осевым растяжением (сжатием)?
- Какие внутренние силовые факторы возникают в сечении бруса при растяжении и сжатии?
- Дайте определение эпюры внутреннего силового фактора.
- Какой вид нагружения стержня называется растяжением (сжатием)?
- Что называют нормальной силой?
- Как определяется значение нормальной силы в поперечном сечении?
- Какие нагрузки называют распределенными? Указать размерности различных внешних сил (в системе СИ).
- Как вычисляется значение продольной силы N в произвольном поперечном сечении бруса?
- Что представляет собой эпюра продольных сил и как она строится?
- Как распределены нормальные напряжения σх в поперечных сечениях центрального растянутого бруса и чему они равны?
- В каких сечениях растянутого бруса возникают наибольшие нормальные напряжения?
- Что называется жесткостью поперечного сечения при растяжении?
- Как формулируется закон Гука? Запишите формулы абсолютной и относительной продольной деформации бруса?
- Что представляют собой эпюра продольных перемещений?
- В чем смысл и какова формула поверочного расчета?
- Как назначаются допускаемые напряжения для пластичных и хрупких материалов?
- Как выполняется проектировочный расчет?
- Почему необходимо выполнять условие жесткости? Приведите примеры.
- Как вычисляется значение продольной силы в произвольном поперечном сечении стержня?
- Какого характера напряжения возникают в поперечном сечении при растяжении и сжатии: нормальные или касательные?
- Как распределены нормальные напряжения в поперечных сечениях центрально-растянутого или центрально-сжатого стержня и по какой формуле они определяются?
- В каких единицах измеряется напряжение?
- Как назначаются знаки продольной силы и нормального напряжения?
- Как связаны гипотеза плоских сечений (гипотеза Бернулли) и закон распределения нормальных напряжений в поперечном сечении растянутого (сжатого) стержня?
- Раскройте понятие эпюр продольных сил, нормальных напряжений и перемещений. Для чего они строятся? Каких правил придерживаются при построении эпюр?
- Что показывает эпюра продольной силы?
Что представляют собой эпюры внутренних силовых факторов? С какой целью их строят?
- Опишите технику построения эпюры продольных сил в брусе, загруженном несколькими сосредоточенными силами по оси бруса?
- Как вычислить значение продольной силы в произвольном поперечном сечении бруса?
- Как вычислить напряжения в поперечном сечение бруса при растяжении и сжатии? Как они распределены по поперечному сечению?
- Как определяют абсолютное удлинение ступенчатого бруса, нагруженного несколькими силами?
- Как определяется удлинение призматического бруса от собственного веса?
- Какое влияние оказывает собственный вес стержня при проектирования сооружения?
- Что понимается под брусом равного сопротивления?
- Запишите формулы для определения удлинения бруса. Что характеризует произведение АЕ и как оно называется?
- Какие деформации бруса называются абсолютными и какие относительными?
- Что называется удлинением стержня (абсолютной продольной деформацией)? Что такое относительная продольная деформация? Каковы размерности абсолютной и относительной продольных деформаций?
- Опишите технику определения продольных и поперечных деформаций бруса при растяжении-сжатии?
- Стальной стержень длиной 1,5 м вытянулся под нагрузкой на 3 мм. Чему равно относительное удлинение? Чему равно относительное сужение? ( = 0,25)
- Что характеризует модуль упругости материала? Какова единица измерения модуля упругости?
- Что называется модулем упругости Е? Как влияет величина Е на деформации стержня?
- Что называется жесткостью поперечного сечения стержня при растяжении (сжатии)?
- Относительные деформации и перемещения.
- Что понимается под жесткостью при растяжении или сжатия стержня?
- Принципы расчета на жесткость.
- Типы задач при расчетах на жесткость.
- Примеры влияния жёсткости на работоспособность конструкции.
- Сформулируйте закон Гука. Напишите формулы для абсолютной и относительной продольных деформаций стержня.
- Что происходит с поперечными размерами стержня при его растяжении (сжатии)?
- Что характеризует коэффициент поперечной деформации?
- Что такое коэффициент Пуассона? В каких пределах он изменяется?
- Как определяется коэффициент Пуассона?
4. Геометрические характеристики плоских сечений
Сопротивление стержня различным видам деформирования часто зависит не только от его материала и размеров, но и от характера осевой линии, формы поперечных сечений и их ориентации.
Уже в древности строители знали, что доска или брус, поставленные на ребро, во много раз лучше противостоят изгибу, чем положенные плашмя. Речь идет как об их несущей способности, так и о деформативности. Для двутавровой стандартной балки, поставленной на две опоры, эти показатели примерно в 7 и 30 раз выше, чем у балки квадратного поперечного сечения такой же площади, cделанной из того же материала. Таким образом, рациональное расположение материала по сечению позволяет снизить его расход.
Как увидим дальше, этот вывод имеет обобщение на форму конструкции в целом. Но в данный момент, отвлекаясь от физических свойств изучаемого объекта, рассмотрим основные геометрические характеристики поперечных сечений стержня, определяющие сопротивление различным видам его деформирования.
В расчетах конструкций на механическую надежность очень часто приходится оперировать такими характеристиками плоских фигур, как статический момент, осевой и полярный моменты инерции. Хотя вычисление вышеназванных геометрических характеристик относится к числу простейших задач интегрального исчисления, тем не менее, в силу их узкого прикладного значения они практически не рассматриваются во втузовском курсе высшей математики. По установившейся традиции геометрические характеристики плоских фигур изучаются в курсе сопротивления материалов.
Геометрические характеристики – числовые величины (параметры), определяющие размеры, форму, расположение поперечного сечения однородного по упругим свойствам деформируемого элемента конструкции (и, как следствие, характеризующие сопротивление элемента различным видам деформации).
4.1.Статические моменты сечения
Статическим моментом плоского сечения относительно некоторой оси называется, взятая по всей его площади А, сумма произведений площадей элементарных площадок dA на их расстояния от этой оси (рис. 4.1):
где yc – расстояние от центра тяжести всего плоского сечения до оси x; xc – расстояние от центра тяжести всего сечения до оси y.
Статический момент сложного сечения относительно некоторой оси равен сумме статических моментов всех частей этого сечения относительно той же оси:
В формулах (6) введены обозначения: А1, А2, …, Аn – площади простых элементов, составляющих плоское сложное сечение; x1, y1, x2, y2, x3, y3, … , xn, yn – координаты центров тяжести простых составляющих сложного плоского сечения относительно выбранных осей х и у.
Из выражений (4) можно определить координаты центра тяжести плоского сечения:
Для сложного поперечного сечения формулы (7) можно представить в следующем виде
Зависимости между статическими моментами одного и того же сечения относительно двух параллельных друг другу осей х и х1, а также у и у1 имеют вид:
где параметры a, b показаны на рис. 4.2.
Рис.4.2
У к а з а н и я.
1. Изменение положительного направления оси у вызывает изменение знака статического момента Sx. Аналогично, изменение положительного направления оси х вызывает изменение знака статического момента Sy.
2. Статический момент сечения равен нулю относительно любой оси, проходящей через центр тяжести этого сечения.
3. Если плоское сечение имеет ось симметрии, то эта ось всегда проходит через центр тяжести плоского сечения, а поэтому, согласно п.2, статический момент сечения относительно оси симметрии всегда равен нулю.
4. Если плоское сечение имеет две оси симметрии, то центр тяжести сечения лежит на пересечении этих осей симметрии.
4.2. Моменты инерции плоских сечений простой формы.
В дополнение к статическим моментам в системе координат x0y рассмотрим три интегральных выражения:
Первые два интегральных выражения называются осевыми моментами инерции относительно осей x и y, а третье центробежным моментом инерции сечения относительно осей x, y.
Для сечений, состоящих из n-числа областей (рис. 4.3), формулы (10) будут иметь вид:
Рис. 4.3.
4.3. Моменты инерции плоских сечений простой формы
В дополнение к статическим моментам в системе координат x0y рассмотрим три интегральных выражения:
Первые два интегральных выражения называются осевыми моментами инерции относительно осей x и y, а третье центробежным моментом инерции сечения относительно осей x, y.
Для сечений, состоящих из n-числа областей (рис. 4.4), формулы (10) будут иметь вид:
Рис. 4.4
где радиусвектор точки тела в заданной полярной системе координат.
Рис. 4.5
Вычислим полярный момент инерции круга радиуса R. На рис. 4.5, a показана элементарная площадка, очерченная двумя радиусами и двумя концентрическими поверхностями, площадью
Интегрирование по площади заменим двойным интегрированием:
Hайдем зависимость между полярным и осевыми моментами инерции для круга. Из геометрии видно (рис. 4.5, б), что
следовательно,
Данное условие называется условием инвариантности. Формулируется условие инвариантности следующим образом: сумма осевых моментов инерции относительно двух любых взаимно перпендикулярных осей есть величина постоянная и равная полярному моменту инерции относительно точки пересечения этих осей.
Так как оси x и y для круга равнозначны, то
Полярный момент инерции кольца может быть найден как разность моментов инерции двух кругов: наружного (радиусом R) и внутреннего (радиусом r):
Размерность моментов инерции L4. Осевые и полярные моменты инерции всегда положительны, центробежный момент инерции может быть положительным, отрицательным, равным нулю.
Для фигур, имеющих более двух осей симметрии, осевые моменты инерции относительно всех центральных осей равны между собой. К таким фигурам относятся равносторонний треугольник, квадрат, круг и т.д.
Моменты инерции простых сечений
Вычислим моменты инерции простейших фигур.
Прямоугольник (рис. 4.6)
Определим моменты инерции относительно осей, совпадающих со сторонами, и относительно центральных осей (рис.4.6).
По определению
Рис. 4.6
Элемент площади равен dA=bdy,
следовательно
По формуле , откуда, учитывая что А = bh, yc = 0,5h, находим
Аналогично получим и
Треугольник (рис. 4.7)
Момент инерции относительно оси х, cовпадающей с основанием,
Но dA = b(y)dy, b(y) = (b/h)(h-y).
Cледовательно,
Рис. 4.7
По формуле параллельного переноса , откуда
Круг (рис. 4.8)
Для любых центральных осей , поэтому
Как известно, полярный момент инерции круга равен
Рис. 4.8
Следовательно,
Кольцо (рис. 4.9)
Момент инерции относительно оси (рис.4.9) можно определить как разность моментов инерции наружного и внутреннего круга:
Для тонкого кольца существует приближенная формула , где dср – средний диаметр, t - толщина кольца.
Рис. 4.9
Моменты инерции сечений сложной формы
Момент инерции сечения сложной формы относительно некоторой оси равен сумме моментов инерций его составных частей относительно той же оси:
что непосредственно следует из свойств определенного интеграла. Таким образом, для вычисления момента инерции сложной фигуры надо разбить ее на ряд простых фигур, вычислить моменты инерции этих фигур, а затем просуммировать их.
4.3. Моменты сопротивления
Осевой момент сопротивления относительно рассматриваемой оси – величина равная моменту инерции относительно той же оси отнесенному к расстоянию до наиболее удаленной от этой оси точки
Полярный момент сопротивления
Осевой и полярный моменты инерции имеют размерность м3.
ВОПРОСЫ ДЛЯ САМОПРОВЕРКИ
- Что называют поперечным сечением стержня?
- Для чего необходимы геометрические характеристики плоских сечений?
- Что такое статический момент плоской фигуры? Какова его размерность?
- Какими свойствами обладает статический момент?
- Относительно каких осей статический момент равен нулю?
- Какую размерность имеет статический момент сечения?
- Как определяется положение центра тяжести сечения?
- Как определяются координаты центра тяжести сложного сечения?
- Что понимается под осевым, полярным и центробежным моментами инерций? Какими свойствами они обладают? Их размерность?
- Что такое полярный момент инерции?
- Размерность моментов инерции сечения?
- Как записываются формулы перехода для моментов инерции при параллельном переносе осей?
- Чему равен осевой момент инерции относительно центральной оси?
- Чему равен осевой момент инерции для круга и кольца?
- Получите соотношение между осевыми и полярными моментами инерции сечения?
- Что такое момент сопротивления сечения? Чему он равен для прямоугольного и круглого сечения?
- Чему равен центробежный момент инерции относительно главных осей инерции?
- Какие центральные оси являются главными у сечений, имеющих более двух осей симметрии?
- Почему производят разбивку сложного сечения на составляющие простые части при определении статических моментов и моментов инерции сечения?
- Какие оси называются центральными осями ?
5. Кручение, сдвиг, срез
5.1. Основные понятия. Крутящий момент
Под кручением понимается такой вид деформации, когда в поперечных сечениях бруса действует только крутящий момент Mk, (другое обозначение T, Mz), а остальные силовые факторы (нормальная и поперечная силы и изгибающие моменты) отсутствуют.
Или другое определение кручением называют деформацию, возникающую при действии на стержень пары сил, расположенной в плоскости, перпендикулярной к его оси..
Кручение возникает в валах, винтовых пружинах, в элементах пространственных конструкций и т.п.
Стержни круглого или кольцевого сечения, работающие на кручение, называют валами.
Внешние крутящие моменты передаются на вал в местах посадки на него шкивов, зубчатых колес, там, где поперечная нагрузка смещена относительно оси вала.
Мы будем рассматривать прямой брус только в состоянии покоя или равномерного вращения. В этом случае алгебраическая сумма всех внешних скручивающих моментов, приложенных к брусу, будет равна нулю.
При расчете брусьев, испытывающий деформацию кручения, на прочность и жесткость при статическом действии нагрузки, надо решить две основные задачи. Это определение напряжений (от Mk), возникающих в брусе, и нахождение угловых перемещений в зависимости от внешних скручивающих моментов.
При расчете валов обычно бывает известна мощность, передаваемая на вал, а величины внешних скручивающих моментов, подлежат определению. Внешние скручивающие моменты, как правило, передаются на вал в местах посадки на него шкивов, зубчатых колес и т.п.
Построение эпюр крутящих моментов
Для определения напряжений и деформаций вала необходимо знать значения внутренних крутящих моментов Mk (Mz) в поперечных сечениях по длине вала. Диаграмму, показывающую распределение значений крутящих моментов по длине бруса, называют эпюрой крутящих моментов. Зная величины внешних скручивающих моментов и используя метод сечений, мы можем определить крутящие моменты, возникающие в поперечных сечениях вала.
В простейшем случае, когда вал нагружен только двумя внешними моментами (эти моменты из условия равновесия вала ΣMz=0 всегда равны друг другу по величине и направлены в противоположные стороны), как показано на рис. 5.1, крутящий момент Mz в любом поперечном сечении вала (на участке между внешними моментами) по величине равен внешнему моменту |M1|=|M2|.
Рис. 5.1
В более сложных случаях, когда к валу приложено несколько внешних моментов, крутящие моменты Mk в поперечных сечениях различных участков вала неодинаковы.
На основании метода сечений крутящий момент в произвольном поперечном сечении вала численно равен алгебраической сумме внешних скручивающих моментов, приложенных к валу по одну сторону от рассматриваемого сечения.
При расчетах на прочность и жесткость знак крутящего момента не имеет никакого значения, но для удобства построения эп. Mk примем следующее правило знаков: крутящий момент считается положительным, если при взгляде в торец отсеченной части вала действующий на него момент представляется направленным по ходу часовой стрелки (рис.5.2).
В технике употребляется терминология « винт с правой нарезкой» или «…с левой нарезкой…», причем правый винт наиболее распространен, являясь стандартом. Полезно заметить, что при навинчивании гайки на правый винт мы прикладываем положительный момент Mкр , а при свинчивании гайки – отрицательный.
Рис. 5.2
На рис. 5.3, а изображен стержень, жестко защемленный в правом концевом сечении, к которому приложены три внешних скручивающих момента.
Рис. 5.3
В нашем случае крутящие моменты в их поперечных сечениях удобно выражать через внешние моменты, приложенные со стороны свободного конца бруса.
Это позволяет определять крутящие моменты, не вычисляя реактивного момента, возникающего в заделке.
Крутящий момент Mz1 в сечении I численно равен M1=200 нм и, согласно принятому правилу знаков, положителен.
Крутящий момент Mz2 в сечении II численно равен алгебраической сумме моментов M1 и M1, т.е. Mz2 =200-300=-100 нм, а его знак зависит от соотношения этих моментов.
Аналогичным образом вычисляется крутящий момент Mz3 в сечении III: Mz3 =200-300+500=400 нм.
Изменение крутящих моментов по длине вала покажем с помощью эпюры крутящих моментов. На рис. 5.3, б показана такая эпюра для стержня, изображенного на рис. 5.4, а.
Каждая ордината эп. Mk в принятом масштабе равна величине крутящего момента, действующего в том поперечном сечении бруса, которому соответствует эта ордината.
В сечении, в котором к брусу приложен внешний скручивающий момент, ордината эпюры изменяется скачкообразно на величину, равную значению этого момента.
Напряжения в поперечном сечении
Опыты показывают, что если на поверхности бруса круглого сечения нанести прямоугольную сетку, а на торцевой поверхности нанести радиальные линии (рис.5.5), то после деформации кручение окажется что:
- все образующие поворачиваются на один и тот же угол , а прямоугольники, нанесенные на поверхности, превращаются в параллелограммы;
- торцевые сечения остаются круглыми, плоскими, расстояния между ними не меняются;
- каждое сечение поворачивается относительно другого на некоторый угол , называемый углом закручивания;
- радиальные линии на торцевой поверхности остаются прямыми.
На основании этих наблюдений можно заключить, что может быть принята гипотеза Бернулли (гипотеза плоских сечений), а в вале возникают условия чистого сдвига, в поперечных сечениях действуют только касательные напряжения, нормальные напряжения равны нулю.
Рассмотрим поперечное сечение вала, расположенное на некотором расстоянии z от торцевого, где Мк=T (рис.5.4). На элементарной площадке dF будет действовать элементарная сила , момент который относительно оси вала равен . Крутящий момент Мк, в сечении равен
Рис.5.4
Для того чтобы проинтегрировать это выражение необходимо знать закон распределения напряжений в сечении. Выделим из вала элементарное кольцо длиной dz и толщиной (рис.5.5).
Правый торец элемента повернется относительно левого на угол , образующая СВ повернется на угол и займет положение СВ1. Угол - относительный сдвиг. Из треугольника ОВВ1 найдем:
Рис.5.5 Рис.5.6
Из треугольника СВВ1: . Откуда, приравнивая правые части, получим
На основании закона Гука при сдвиге:
Подставим выражение (5.2) в (5.1):
Откуда
Подставим значение в выражение (5.4) получим:
Таким образом, касательные напряжения при кручении прямо пропорциональны расстоянию от центра тяжести сечения до рассматриваемой точки и одинаковы в точках, одинаково удаленных от центра тяжести сечения (рис. 5.6). При получим . Наибольшие напряжения возникают в точках контура сечения при :
Величина отношения полярного момента инерции к радиусу вала называется моментом сопротивления сечения при кручении или полярным моментом сопротивления
Для сплошного круглого сечения
Для кольцевого сечения
где
Тогда максимальные касательные напряжения равны
Условие прочности при кручении вала круглого и кольцевого сечения
Условие прочности при кручении с учетом принятых обозначений формулируется следующим образом: максимальные касательные напряжения, возникающие в опасном сечении вала, не должны превышать допускаемых напряжений и записывается в виде
где - берется либо на основании опытных данных, либо (при отсутствии нужных опытных характеристик) по теориям прочности, соответствующим материалу.
Рациональная форма сечения вала
Анализируя эпюру касательных напряжений (рис.5.6) можно отметить, что наибольшие напряжения возникают на поверхности вала, в центральной части они значительно меньше и на продольной оси равны нулю. Следовательно, в сплошном валу материал, находящийся в центральной части в значительной степени недогружен, его вклад в прочность вала мал. Поэтому рациональным для валов считается кольцевое сечение.
5.2. Деформации при кручении и условие жесткости вала
Из выражения (5.5) следует, что
интегрируя которое по длине вала, получим:
Если Мк = const и по всей длине вала, то абсолютный угол закручивания
где - жесткость вала при кручении.
При скачкообразном изменении по длине бруса крутящего момента угол закручивания между его начальным и конечным сечениями определяется как сумма углов закручивания по участкам с постоянным Mk
Угол закручивания, приходящийся на единицу длины, называют относительным углом закручивания
Для обеспечения требуемой жесткости вала необходимо, чтобы наибольший относительный угол закручивания не превосходил допускаемого:
Эта формула выражает условие жесткости вала при кручении. Обычно принимается на 1 м длины вала.
5. 3. Расчеты на прочность и жесткость валов круглого и кольцевого сечений
При расчетах на прочность при кручении (также как и при растяжении) могут решаться три задачи:
а) проверочный расчет – проверить, выдержит ли вал приложенную нагрузку;
б) проектировочный расчет - определить размеры вала из условия его прочности;
в) расчет по несущей способности - определить максимально допустимый крутящий момент.
- При проверочном расчете на прочность рекомендуется следующий порядок расчета валов при кручении:
1) по схеме вала и действующим на него скручивающим моментам строят эпюру внутренних крутящих моментов по отдельным участкам;
2) выбирают материал для рассчитываемого вала и определяют для этого материала допускаемое напряжение, например по формуле (5.9), ;
3) для участка вала с максимальным по модулю значением крутящего момента записывают условие прочности при кручении
- Проектировочный расчет проводится, исходя из условия прочности на основе следующего соотношения:
Для сплошного круглого сечения , отсюда можем записать выражение для определения диаметра вала из условия его прочности:
Для кольцевого сечения
Определив размеры вала из условия прочности, проверяют вал на жесткость.
Условие жесткости требует, чтобы максимальный относительный угол закручивания , был меньше или в предельном случае равен допускаемому углу закручивания единицы длины вала, т.е.
Расчет заклепок на срез
На практике целый ряд деталей и элементов конструкций работает в таких условиях, что внешние силы стремятся их разрушить именно путем сдвига.
В соответствии с этим при проверке прочности таких элементов на первый план выступают касательные напряжения. Простейшими примерами подобных деталей являются болтовые и заклепочные соединения. Для образования заклепочного соединения в обоих листах просверливают или продавливают отверстия. В них закладывается нагретый до красного каления стержень заклепки с одной головкой; другой конец заклепки расклепывается ударами специального молотка или давлением гидравлического пресса (клепальной машины) для образования второй головки. Мелкие заклепки (малого диаметра — меньше 8 мм) ставятся в холодном состоянии (авиационные конструкции).
Для изучения работы заклепок рассмотрим простейший пример заклепочного соединения (рис.5.7). Шесть заклепок, расположенных в два ряда, соединяют два листа внахлестку. Под действием сил Р эти листы стремятся сдвинуться один по другому, чему препятствуют заклепки, на которые и будет передаваться действие сил P).
Рис.5.7
Для проверки прочности заклепок применим общий порядок решения задач сопротивления материалов.
На каждую заклепку передаются по две равные и прямо противоположные силы: одна—от первого листа, другая — от второго. Опытные исследования показывают, что одни из заклепок ряда нагружаются больше, другие — меньше. Однако к моменту разрушения усилия, передающиеся на различные заклепки, более или менее выравниваются за счет пластических деформаций. Поэтому принято считать, что все заклепки работают одинаково. Таким образом, при n заклепках в соединении, изображенном на рис.5.7, на каждую из них действуют по две равные и противоположные силы (рис.5.8); эти силы передаются на заклепку путем нажима соответствующего листа на боковую полуцилиндрическую поверхность стержня. Силы стремятся перерезать заклепку по плоскости mk раздела обоих листов.
Рис.5.8
Для вычисления напряжений, действующих по этой плоскости, разделим мысленно заклепочный стержень сечением mk и отбросим нижнюю часть (рис.5.8). Внутренние усилия, передающиеся по этому сечению от нижней части на верхнюю, будут уравновешивать силу т. е. будут действовать параллельно ей в плоскости сечения, и в сумме дадут равнодействующую, равную . Следовательно, напряжения, возникающие в этом сечении и действующие касательно к плоскости сечения, это — касательные напряжения . Обычно принимают равномерное распределение этих напряжений по сечению. Тогда при диаметре заклепки d на единицу площади сечения будет приходиться напряжение:
Величина допускаемого касательного напряжения , или, как говорят, допускаемого напряжения на срез, принято определять в виде: . Зная , мы напишем условие прочности заклепки на перерезывание в таком виде:
т. е. действительное касательное напряжение в материале заклепки должно быть равно допускаемому , или меньше его.
Из этого условия можно определить необходимый диаметр заклепок, если задаться их числом, и наоборот. Обычно задаются диаметром заклепочных стержней d в соответствии с толщиной t склепываемых частей (обычно ) и определяют необходимое число заклепок n:
5.4. Расчет заклепок на смятие и листов на разрыв
Помимо среза заклепкам и соединяемым листам в конструкции угрожают и иные опасности.
Так как передача сил на заклепочный стержень происходит путем нажатия стенок заклепочного отверстия на заклепку, то необходимо установить, не произойдет ли наружное обмятие этого стержня или стенок отверстия, — произвести проверку на смятие.
Под смятием понимают пластическую деформацию, возникающую в соединениях на поверхностях контакта. Возникающие при этом напряжения являются нормальными, закон распределения которых по поверхности контакта достаточно сложен.
На рис.5.9 указана примерная схема передачи давлений на стержень заклепки. Закон распределения этих давлений по цилиндрической поверхности нам неизвестен; он во многом зависит от неправильностей формы заклепочного отверстиями стержня, вызванных условиями изготовления конструкции. Поэтому расчет производится условно. Принято считать, что неравномерное давление, передающееся на поверхность заклепки от листа, распределяется равномерно по диаметральной плоскости сечения заклепки. При этом напряжение по этой диаметральной плоскости оказывается примерно равным наибольшему сминающему напряжению в точке А поверхности заклепки.
Рис.5.9
Чтобы вычислить это условное напряжение смятия, необходимо разделить силу, приходящуюся на заклепку, на площадь диаметрального сечения ВСС'В'. Эта площадь представляет собой прямоугольник, одной стороной которого служит диаметр заклепки, другая же равна толщине листа, передающего давление на стержень заклепки.
Так как давление на одну заклепку равно P/n, то
условие прочности на смятие будет иметь вид:
где — допускаемое напряжение на смятие. Отсюда необходимое число заклепок
ВОПРОСЫ ДЛЯ САМОПРОВЕРКИ
- Какой вид нагружения называется кручением?
- При каком нагружении возникает кручение бруса (вала)?
- Какой силовой фактор вызывает закручивание бруса?
- Что такое крутящий момент?
- Что называется валом?
- Когда в брусе возникают деформации кручения?
- Как определяют величину крутящего момента, действующего в сечении?
- Какое правило знаков для Т принято при построении эпюр?
- Как строятся эпюры крутящих моментов?
- Как определяют угол закручивания на участке вала?
- Что называют относительным углом закручивания θ (или кривизной кручения kt)?
- Какие напряжения возникают в поперечном сечении круглого вала при кручении и как они направлены?
- Какое напряженное состояние возникает в каждой точке вала круглого сечения при кручении?
- Что называется жесткостью сечения при кручении?
- Что выражает условие жесткости при кручении?
- Чем объясняется, что вал кольцевого сечения при кручении экономичнее вала сплошного сечения?
- Как выполняют расчет вала на прочность?
- Как называется напряженное состояние, возникающее при кручении круглого бруса (вала)?
- Какие деформации возникают при кручении?
- Какие гипотезы выполняются при деформации кручения?
- По какой формуле определяется касательное напряжение при кручении?
- Как распределяется касательное напряжение при кручении? Чему равно напряжение в центре круглого поперечного сечения?
- Как вычислить потенциальную энергию деформации, накапливаемую валом при кручении?
- В каких точках бруса круглого сечения возникают наибольшее касательное напряжение? Как их вычисляют?
- Как определяется диаметр вала из условия жесткости?
- Как выбираются допускаемые напряжения при расчете на кручение?
- Укажите единицы измерения напряжений сдвига и смятия и модуля упругости.
- Что такое срез?
- Что такое смятие?
- Какие допущения проложены в основу практических расчетов элементов конструкции на срез и смятие?
- Опишите процесс разрушения при срезе?
- Как выбирается допускаемое напряжение при сдвиге?
- Что понимается под деформацией смятия?
- В чем заключается явление смятия и в каких местах оно наблюдается?
- Как записывается условие прочности на срез и на смятие?
- Как находится площадь смятия при соприкосновении цилиндрических поверхностей?
- Как определяется расчетная величина площади на срез и на смятие при болтовых соединениях листовых элементов внахлестку и с помощью накладок?
- Какие виды деформации испытывает нагруженное заклепочное соединение?
- Как учесть количество деталей, использованных для передачи нагрузки при расчетах на сдвиг и смятие?
- Как определить необходимое количество заклёпок, обеспечивающее безопасную прочность соединения?
6. Прямой изгиб
Общие сведения
Изгибом называется вид нагружения бруса, при котором к нему прикладывается поперечная нагрузка, лежащая в плоскости проходящей через продольную ось (рис.6.1, а). В этой же плоскости располагается изогнутая ось стержня (упругая линия) (рис.6.1, б). Брус, работающий при изгибе, называется балкой. Изгиб называется плоским или прямым, если плоскость действия нагрузки проходит через главную центральную ось инерции сечения (рис.6.1).
Рис. 6.1
При плоском поперечном изгибе в балке возникают два вида внутренних усилий (рис.6.1,в): поперечная сила Qy , где y – ось симметрии (главная центральная ось) и изгибающий момент Mx. , где x – другая главная центральная ось сечения, нормальная к оси симметрии. В раме при плоском поперечном изгибе возникают три усилия: продольная N, поперечная Q силы и изгибающий момент M.
Если изгибающий момент Mx является единственным внутренним силовым фактором, то такой изгиб называется чистым (рис.6.2). При наличии поперечной силы Qy изгиб называется поперечным. Строго говоря, к простым видам сопротивления относится лишь чистый изгиб; поперечный изгиб относят к простым видам сопротивления условно, так как в большинстве случаев (для достаточно длинных балок) действием поперечной силы при расчетах на прочность можно пренебречь.
Косой изгиб - изгиб, при котором нагрузки действуют в одной плоскости, не совпадающей с главными плоскостями инерции.
6.1. Построение эпюр поперечной силы и изгибающего момента
Для того, чтобы произвести расчет балки на изгиб, необходимо знать величину наибольшего изгибающего момента М и положение сечения, в котором он возникает. Точно также, надо знать и наибольшую поперечную силу Q. Для этой цели строят эпюры изгибающих моментов и поперечных сил. По эпюрам легко судить о том, где будет максимальное значение момента или поперечной силы.
Эпюра внутренней силы – график, показывающий изменение этой силы по длине балки.
Для построения эпюр балка разбивается на участки, в пределах которых функция внутренней силы не меняет своего аналитического выражения. За границы участков принимаются сечения, в которых приложены внешние нагрузки: сосредоточенные силы, сосредоточенные моменты, начинается или заканчивается распределенная нагрузка одного направления и изменяющаяся по одному закону, а также начало и конец балки.
Перед тем, как определять внутренние усилия (поперечные силы и изгибающие моменты) и строить эпюры, как правило, надо найти опорные реакции, возникающие в закреплении стержня. Если опорные реакции и внутренние усилия можно найти из уравнений статики, то конструкция называется статически определимой. Чаще всего мы встречаемся с тремя видами опорных закреплений стержней: жестким защемлением (заделкой), шарнирно-неподвижной опорой и шарнирно-подвижной опорой. На рис. 6.2 показаны эти закрепления. Для неподвижной (рис 6.2,б) и подвижной (рис. 6.5,в) опор приведены два эквивалентных обозначения этих закреплений. Напомним, что при действии нагрузки в одной плоскости в заделке возникают три опорных реакции (вертикальная, горизонтальная реакции и сосредоточенный реактивный момент) (рис. 6.2,а); в шарнирно-неподвижной опоре – две реактивные силы (рис. 6.2,б); в шарнирно-подвижной опоре – одна реакция – сила, перпендикулярная плоскости опирания (рис.6.2,в).
Рис. 6.2. Опорные реакции: а – в заделке; б – в шарнирно-неподвижной опоре;
в – в шарнирно-подвижной опоре
После определения опорных реакций внутренние усилия в статически определимых конструкциях определяем с помощью метода сечений.
Как было сказано выше, при плоском поперечном изгибе в балке возникают два внутренних усилия: поперечная сила Q и изгибающий момент M. В соответствии с методом сечений поперечную силу можно найти как сумму проекций всех внешних сил, взятых с одной стороны от сечения, на ось, перпендикулярную оси стержня (ось z). Изгибающий момент равен сумме моментов всех внешних сил, взятых с одной стороны от сечения, относительно оси, проходящей через центр тяжести рассматриваемого сечения (оси y).
Для того чтобы можно было вести расчет с любого конца балки, необходимо принять правило знаков для внутренних силовых факторов.
Если внешняя сила вращает отрезанную часть балки по часовой стрелке, то сила является положительной, если внешняя сила вращает отрезанную часть балки против хода часовой стрелки, то сила является отрицательной.
Если под действием внешней силы изогнутая ось балки принимает вид вогнутой чаши, такой, что идущий сверху дождь будет наполнять ее водой, то изгибающий момент является положительным. Если под действием внешней силы изогнутая ось балки принимает вид выпуклой чаши, такой, что идущий сверху дождь не будет наполнять ее водой, то изгибающий момент является отрицательным.
а) б)
Рис.6.3. а - правило знаков для поперечной силы Q; б - правило знаков для изгибающего момента M.
Достаточно очевидно и подтверждается опытом, что балка при изгибе деформируется таким образом, что волокна, расположенные в выпуклой части, растягиваются, а в вогнутой – сжимаются. Между ними лежит слой волокон, который лишь искривляется, не изменяя своей первоначальной длины (рис.6.4). Этот слой называется нейтральным или нулевым, а его след на плоскости поперечного сечения – нейтральной (нулевой) линией или осью.
Рис.6.4
При построении эпюр Q и М договоримся на эпюре Q положительные значения откладывать сверху нулевой линии. На эпюре М у строителей принято откладывать положительные ординаты снизу. Такое правило построения эпюры М называется построением эпюры со стороны растянутых волокон, т. е. положительные значения М откладываются в сторону выпуклости изогнутой балки.
Рассмотрим для простоты балку с прямоугольным поперечным сечением (рис.6.9). Следуя методу сечений, мысленно проведем разрез и отбросим какую-либо часть балки, а другую оставим. На оставшейся части покажем действующие на нее силы и в поперечном сечении – внутренние силовые факторы, которые являются результатом приведения к центру сечения сил, действующих на отброшенную часть. Учитывая, что внешние силы и распределенные нагрузки лежат в одной плоскости и действуют перпендикулярно оси балки, в сечении получим поперечную силу Qy и изгибающий момент Mx. Эти внутренние силовые факторы заранее неизвестны, поэтому их показывают в положительном направлении в соответствии с принятыми правилами знаков.
На рис.6.5 показаны два случая оставшейся части: левая и правая.
Для определения величины Qy и Mx составляются два уравнения равновесия для оставшейся части
Рис.6.5
Изгибающий момент Mx, действующий в поперечном сечении балки, по величине равен сумме моментов всех внешних сил, приложенных к рассматриваемой отсеченной части бруса, относительно центральной оси x этого сечения:
Если внешняя сила в данном сечении растягивает нижние волокна балки, то момент этой силы в этом сечении считается положительным, если растягиваются верхние волокна балки, то момент этой силы будет отрицательным.
Поперечная сила Qy в сечении бруса, по величине равна сумме проекций всех внешних сил, действующих на отсеченную часть бруса, на ось перпендикулярную оси бруса (ось y):
Уравнение момента составляется относительно оси Х, проходящей в поперечном сечении через точку на оси балки – тогда поперечная сила в уравнение не входит и величина Mx определяется независимо от Qy. Можно доказать, что результат вычислений Qy и Mx не зависит от того, равновесие какой оставшейся части рассматривается.
Рассмотрим характерный пример (рис. 6.6,а) и установим необходимые правила. Решение задачи, как правило, начинается с определения полной системы внешних сил. Для этого отбросим опоры и заменим их соответствующими реакциями (рис. 6.6,б), выполняющими ту же роль, что и опорные закрепления.
Заданная система статически определима, следовательно, из условий равновесия системы, т.е. равенства нулю суммы моментов всех сил относительно шарнирных опор (в шарнирах нет ограничений поворота сечений балки, поэтому изгибающих моментов не возникает) и , определяем вертикальные реакции в опорах:
Для определения имеем: откуда . Для проверки правильности вычислений воспользуемся условием равенства нулю суммы всех вертикальных сил откуда получим
0 = 0.
Рис. 6.6
Для определения внутренних силовых факторов изгибающего момента М(z) и поперечной силы Q(z) как функций от продольной координаты z, воспользуемся методом сечений. Для получения этих зависимостей балку разбивают на участки, границами которых являются следующие точки: начало и конец балки; точки приложения сосредоточенных усилий; начало и конец действия распределенных усилий; сечения, в которых скачкообразно изменяется жесткость балки; в точках, где происходит изменение ориентации элементов, если имеем дело с стержневой системой со сложной структурой.
Заданная система состоит из двух участков первого (0≤z≤a) и второго (a≤z≤a+b). Следовательно, задавая последовательно сечения, принадлежащие к первому и второму участкам, и рассматривая равновесие отсеченных частей системы при действии на них всех внешних сил и внутренних усилий, определим выражения для внутренних силовых факторов.
Из условия равновесия отсеченной части системы, расположенной левее от сечения z1 (первый участок), (см. рис. 6.6, в), получим:
Для определения Qy и Mx на втором участке рассмотрим равновесие отсеченной части балки, расположенной правее от сечения z2 (см. рис. 6.10, б), т.е. откуда и определим:
Эпюры Qy и Mx изображены на рис. 6.7. Заметим, что эпюры изгибающих моментов Mx, как и поперечных сил Qy строятся на оси бруса, однако в отличие от эпюры поперечных сил знак момента не указывается, а ординаты изгибающего момента откладываются co стороны растянутых волокон.
Рис. 6.7
6.2. Основные дифференциальные соотношения теории изгиба
Пусть брус нагружен произвольным образом распределенной нагрузкой q=f(z) (рис. 6.8,а).
Рис. 6.8
Выделим из бруса элемент длиной dz и приложим по его краям положительные внутренние усилия (рис. 6.8,б). В пределах малого отрезка dz нагрузку q можно считать распределенной равномерно. Приравняем нулю сумму проекций всех сил на вертикальную ось y и сумму моментов всех сил относительно поперечной оси x, проходящей через точку С (рис. 6.8,б), получим:
Производя упрощения и отбрасывая величины высшего порядка малости, получим теорему Журавского (теорему Шведлера):
откуда
Указанные дифференциальные зависимости при изгибе позволяют установить некоторые особенности эпюр поперечных сил и изгибающих моментов.
1. Эпюра Q является прямолинейной на всех участках. На тех участках, где нет распределенной нагрузки, эпюра Q ограничена прямыми, параллельными оси эпюры, а эпюра М, в общем случае, – наклонными прямыми (рис. 6.9).
Рис.6.9
2. На тех участках, где к балке приложена равномерно распределенная нагрузка, эпюра Q ограничена наклонными прямыми, а эпюра М – квадратичными параболами (рис. 6.14). При построении эпюры М на сжатых волокнах, выпуклость параболы обращена в сторону, противоположную действию распределенной нагрузки (рис. 6.10,а, б).
Рис.6.10
3. В тех сечениях, где Q = 0, касательная к эпюре М параллельна оси эпюры (рис. 6.10, 6.11). Изгибающий момент в таких сечениях балки экстремален по величине (Мmax, Mmin).
4. На участках, где Q>0, M возрастает, то есть слева на право положительные ординаты эпюры M монотонно увеличиваются, отрицательные – монотонно уменьшаются (рис. 6.9, 6.10); на тех участках, где Q < 0, M убывает (рис. 6.13, 6.14).
5. В тех сечениях, где к балке приложены сосредоточенные силы:
а) на эпюре Q будут скачки на величину и в направлении приложенных сил (рис. 6.13, 6.14).
б) на эпюре M будут переломы (рис. 6.9, 6.10), острие перелома направлено против действия силы.
6. В тех, сечениях, где к балке приложены сосредоточенные моменты, на эпюре M будут скачки на величину этих моментов, на эпюре Q никаких изменений не будет (рис. 6.12).
Рис.6.11
Рис.6.12
7. Если на конце консоли или в концевой опоре приложен сосредоточенный момент, то в этом сечении изгибающий момент равен внешнему моменту (сечения C и B на рис. 6.12).
8. Эпюра Q представляет собой диаграмму производной от эпюры M. Значит, ординаты Q пропорциональны тангенсу угла наклона касательной к эпюре M (рис. 6.14).
9. Порядок линии на эпюре Q всегда на единицу меньше, чем на эпюре M. Например, если эпюра M - квадратная парабола, то эпюра Q на этом участке - наклонная прямая; если эпюра M - наклонная прямая, то эпюра Q на этом участке - прямая, параллельная оси; если M =const (прямая, параллельная оси), то на этом участке Q=0.
10. Приращение функции изгибающего момента на рассматриваемом участке численно равно площади эпюры поперечных сил на этом участке с соответствующим знаком. При построении эпюры для изгибающего момента слева направо знаки приращения функции изгибающего момента и площади эпюры поперечных сил совпадают. При построении эпюры изгибающих моментов справа налево знаки приращения функции изгибающих моментов и площади эпюры поперечных сил противоположны.
6.3. Напряжение при чистом изгибе
Рассмотрим наиболее простой случай изгиба, называемый чистым изгибом и выведем формулу для определения нормальных напряжений для данного случая. Отметим, что методами теории упругости можно получить точную зависимость для нормальных напряжений при чистом изгибе, если же решать эту задачу методами сопротивления материалов, необходимо ввести некоторые гипотезы.
Таких гипотез при изгибе три:
1) гипотеза плоских сечений (гипотеза Бернулли). Сечения плоские до деформации остаются плоскими и после деформации, а лишь поворачиваются относительно некоторой линии, которая называется нейтральной осью сечения балки. При этом волокна балки, лежащие с одной стороны от нейтральной оси будут растягиваться, а с другой - сжиматься; волокна, лежащие на нейтральной оси своей длины не изменяют;
2) гипотеза о постоянстве нормальных напряжений - напряжения, действующие на одинаковом расстоянии у от нейтральной оси, постоянны по ширине бруса;
3) гипотеза об отсутствии боковых давлений - соседние продольные волокна не давят друг на друга.
Кроме этих гипотез следует ввести ряд ограничений:
1. Балка имеет хотя бы одну плоскость симметрии, и все внешние силы лежат в этой плоскости.
2. Материал балки подчиняется закону Гука, причем модуль упругости при растяжении и сжатии одинаков.
3. Соотношения между размерами балки таковы, что она работает в условиях плоского изгиба без коробления или скручивания.
Как было отмечено выше, под чистым изгибом понимается такой вид сопротивления, при котором в поперечных сечениях бруса возникают только изгибающие моменты, а поперечные силы равны нулю. Для тех участков бруса, где соблюдается данное условие, изгибающий момент, вдоль продольной оси z принимает постоянное значение. Так как в любом сечении стержня при чистом изгибе Mx(z)=const, то для однородного бруса постоянного поперечного сечения изменение кривизны постоянно вдоль оси z. Под действием изгибающих моментов ось бруса искривляется. Исходя из этого, ось бруса принимает форму дуги окружности с радиусом кривизны (рис. 6.13). В данном случае с высокой степенью точности справедлива гипотеза плоских сечений. Следовательно, точки, расположенные до изгиба в плоскости поперечного сечения бруса, в результате изгиба переместятся в пространстве таким образом, что их совокупность снова образует плоскость.
Процесс формирования деформаций при чистом изгибе может рассматриваться как результат поворота плоских поперечных сечений друг относительно друга.
Рассмотрим два смежных сечения, отстоящих один от другого на расстоянии dz (рис. 6.13).
В результате изгиба эти сечения наклонятся, образуя между собой угол dθ, в связи с чем верхние волокна удлиняются, а нижние укоротятся. Очевидно, что при этом существует слой, длина которого не изменилась. Назовем его нейтральным слоем и обозначим отрезком СD. При этом . Произвольный отрезок АВ, расположенный от СD на расстоянии y, в результате изгиба удлинится на величину . С учетом построений, изображенных на рис. 6.26, легко определить величину его относительной линейной деформации:
Рис. 6.13
Если предположить, что продольные волокна не давят друг на друга, то каждое из них будет находиться в условиях простого растяжения сжатия. Тогда переход от деформаций к нормальным напряжениям можно осуществить посредством закона Гука:
Рис. 6.14
Установим положение нейтральной оси x, от которой происходит отсчет координаты у (рис.6.14). Учитывая, что сумма элементарных сил по площади поперечного сечения A дает нормальную силу Nz. Но при чистом изгибе Nz =0, следовательно:
Как известно, последний интеграл представляет собой статический момент сечения относительно нейтральной линии (оси x). Статический момент равен нулю, значит, нейтральная линия проходит через центр тяжести сечения.
Выразим момент внутренних сил относительно нейтральной оси Mx через σ. Очевидно, что
C учетом выражения (2) получим:
Откуда
где кривизна нейтрального волокна; EIx жесткость бруса.
Из формулы (3), исключая , окончательно получим:
Эта формула была впервые получена Ш. Кулоном в 1773 году.
Таким образом, нормальные напряжения в любой точке сечения прямо пропорциональны величине изгибающего момента и расстоянию точки от нейтральной линии сечения и обратно пропорционально моменту инерции сечения относительно нейтральной оси.
Из выражения (5) можно сделать ряд важных выводов:
1) центр тяжести сечения балки является началом координат для анализа напряжений и приведения внешних сил;
2) напряжения изгиба зависят от значений изгибающего момента, момента инерции сечения и координаты точки, в которой это напряжение определяется;
3) напряжения в любой точке, лежащей на одинаковом расстоянии от нейтральной линии, равны между собой;
4) нормальные напряжения не зависят, а упругие перемещения зависят от модуля упругости материала балки.
В нейтральном слое при y=0 напряжения σ=0, в сжатой зоне (при y<0, рис.6.26) напряжения становятся отрицательными, в растянутой зоне (при y>0, рис. 6.26) напряжения становятся положительными. По мере удаления от нейтрального слоя нормальные напряжения σ в поперечном сечении бруса при его изгибе изменяются по линейному закону в зависимости от координаты y и принимают максимальное значение на уровне крайних волокон (при ):
Измеряется осевой момент сопротивления единицами длины в третьей степени, например (см3). Физический смысл момента сопротивления состоит в следующем: чем больше Wx, тем больший изгибающий момент может принять на себя балка, не подвергаясь опасности разрушения. Таким образом, величина момента сопротивления характеризует влияние формы и размеров поперечного сечения балки на ее способность сопротивляться внешним нагрузкам, не разрушаясь.
При симметричном относительно нейтральной линии сечении, например, прямоугольном, расстояния до крайних растянутых и сжатых волокон одинаковы и такое сечение имеет одно вполне определенное значение момента сопротивления относительно оси Oz. Так, при высоте прямоугольника (рис. 6.15, а), равной h
Рис. 6.15
Если сечение несимметрично относительно нейтральной линии – тавр, мы получим два момента сопротивления: один для волокон А (рис. 6.15,б): и другой для волокон В: . Теперь в формулу (6) следует вводить: W1 при вычислении напряжений в точке А и W2 при вычислении напряжений в точке В.
Для круга
Для прокатных профилей (двутавра, швеллера, уголка) Mx приводится в таблицах сортамента.
Формулой (6) удобно пользоваться для расчета балок пластичного материала в упругой области, одинаково работающего на растяжение и сжатие. Поскольку знак напряжения в этом случае не имеет значения, напряжения вычисляются по модулю, и условие прочности при изгибе балки в форме призматического стержня получает вид
где maxMx — максимальное значение изгибающего момента (легко определяемое по его эпюре), [σ] - допускаемое напряжение на простое растяжение (сжатие). Напомним, что чистый изгиб балки сводится к растяжению и сжатию ее волокон (неравномерному в отличие от деформации растяжения (сжатия) призматического стержня, при котором σ=const).
При расчете балок из хрупких материалов следует различать наибольшие растягивающие maxσp и наибольшие сжимающие maxσc напряжения, которые также определяются по модулю непосредственно и сравниваются с допускаемыми напряжениями на растяжение [σp] и сжатие [σc]. Условие прочности в этом случае будет иметь вид:
В зависимости от того, чему лучше сопротивляется материал, приходится соответсвующим образом конструировать сечение, выбирая его форму и размеры так, чтобы удовлетворяли условию прочности.
Из условия (7) формулируют три рода задач на прочность при изгибе:
1. Проверка прочности: задана балка, нагрузка, известен материал. Строится эпюра Mx – определяется Mmax, вычисляется Wx и по (7) проверяется условие прочности.
2. Определение максимально допустимой нагрузки по условию прочности.
Заданы размеры балки, характер нагрузки, материал балки.
Строится эпюра Mx – определяется Mmax от параметра нагрузки, вычисляется Wx и по (8) находят наибольший параметр нагрузки.
3. Конструирование балки – определение размеров ее поперечного сечения.
Строится эпюра – определяется , вычисляется правая часть (9) и подбираются размеры поперечного сечения, удовлетворяющие (9).
Для прямоугольного сечения
Обычно задаются отношением
Тогда
отсюда
Задаваясь шириной b по (10) получим h.
Для двутаврового сечения по таблице сортамента подбирают номер двутавра с Wx большим, чем правая часть (9).
ВОПРОСЫ ДЛЯ САМОПРОВЕРКИ
- Что называется балкой?
- Какой вид нагружения называется изгибом?
- Какой изгиб называется чистым, поперечным?
- Какой изгиб называют чистым, поперечным, прямым и косым?
- Чем отличается чистый изгиб от поперечного изгиба, прямой изгиб от косого изгиба?
- Сформулируйте определение «поперечный изгиб»?
- Сформулируйте понятие «чистый изгиб»?
- Что понимается под волокнами бруса? В чем сущность гипотезы плоских сечений и допущения о ненадавливании волокон друг на друга?
- Что такое нейтральная линия, силовая линия?
- Какие внутренние усилия возникают в поперечных сечениях балки в общем случае действия на неё плоской системы сил?
- Как формулируется гипотеза плоских сечений?
- Что представляет собой нейтральный слой и нейтральная ось?
- Какие силовые факторы возникают в сечении балки при чистом изгибе?
- Какие силовые факторы возникают в сечении при поперечном изгибе?
- Что такое поперечная сила (Qy)? Как определяется Qy через внешние силы?
- Какие виды опор встречаются при расчете балок? Чем они отличаются?
- Какое правило законов для определения поперечной силы используется?
- Каково правило законов для определения изгибающего момента используется?
- Как вычисляется изгибающий момент в поперечном сечении балки?
- Как вычисляются поперечная и продольная силы в поперечном сечении балки?
- Как определить значение поперечной силы и изгибающего момента в произвольном сечении балки?
- Как определить знаки поперечной силы и изгибающего момента?
- Как проверить правильность определения опорных реакций?
- Как формулируется гипотеза плоских сечений?
- По какой формуле определяются нормальные напряжения в поперечном сечении балки при чистом изгибе и как они изменяются по высоте балки?
- Для чего строят эпюры внутренних силовых факторов?
- Какая нагрузка вызывает скачок на эпюре поперечной силы?
- Какая нагрузка вызывает скачок на эпюре изгибающего момента?
- Как находят опасные сечения?
- Какая дифференциальная зависимость связывает q, Q и M?
- Какие допущения положены в основу вывода формулы для определения нормальных напряжений при изгибе?
Основные сведения
При простых видах деформации (осевое растяжение или сжатие, сдвиг, кручение, плоский изгиб) в поперечных сечениях возникает только одно внутреннее усилие (продольная или поперечная сила, крутящий или изгибающий момент), за исключением плоского поперечного изгиба. На практике же большинство элементов конструкций и машин подвергается действиям сил, вызывающих одновременно не одну из указанных деформаций, а две и более. Различные комбинации простых деформаций называются сложным сопротивлением.
В общем случае нагружения бруса в его поперечных сечениях действуют шесть компонентов внутренних усилий (N, Qx, Qy, Mx, My, Mкр).
Рис. 7.1
Сложный вид деформации можно рассматривать как сумму простых видов, изученных ранее (растяжение, изгиб, кручение), при которых в сечениях элементов конструкций возникал только один внутренний силовой фактор (рис.7.2): нормальная сила N - при растяжении, изгибающий момент
Мz - при чистом изгибе, крутящий момент Мx - при кручении. Эти виды нагружения, растяжение, изгиб, кручение, являются простыми.
Рис.7.2
Основные соотношения, полученные для них, приведены в таблице 7.1
Таблица 7.1
Виды нагружения |
Напряжения |
Деформации |
Растяжение |
. Условие прочности:
|
|
Изгиб |
Условие прочности:
|
|
Кручение |
Условие прочности:
|
|
Но при сложном сопротивлении должен быть применим принцип независимости действия сил (частный случай принципа суперпозиции или наложения, применяемый в механике деформируемого твердого тела).
Задачи на сложное сопротивление решаются следующим образом. Определяются напряжения и деформации при действии простейших видов деформации, составляющих сложное сопротивление, а затем полученные результаты суммируют, используя при необходимости теории прочности.
На практике одновременное действие всех силовых факторов встречается крайне редко. Чаще приходится иметь дело с более простыми комбинациями нагружений – косой или пространственный изгиб, внецентренное растяжение или сжатие и изгиб с кручением.
7.1. Расчет балки, подверженной косому или пространственному изгибу
Косым называют изгиб, при котором плоскость действия изгибающего момента, возникающего в сечении, не совпадает ни с одной из главных плоскостей бруса (при этом плоскость действия изгибающего момента обязательно должна проходить через центр тяжести сечения) (рис.7.4).
Рис.7.3
При косом изгибе изогнутая ось представляет собой плоскую кривую, и плоскость, в которой она расположена, не совпадает с плоскостью действия нагрузки.
При пространственном изгибе нагрузка приложена в разных плоскостях, деформированная ось является пространственной кривой.
Определение внутренних усилий при косом изгибе
При косом изгибе в поперечных сечениях бруса действуют следующие внутренние усилия: Mz, My – изгибающие моменты и Qy, Qz –поперечные (перерезывающие) силы. Это легко показать мысленно рассекая стержень и определяя внутренние усилия при косом изгибе консольной балки под действием сосредоточенной силы F на свободном конце (см. рис.7.4):
Рис. 7.4
Правило знаков для внутренних усилий: изгибающие моменты – положительны, если вызывают растяжение в положительном квадранте координатной системы zOy; поперечные силы – положительны, если под их действием отсеченный элемент поворачивается по часовой стрелке.
Таким образом, косой изгиб может быть представлен как совместное действие двух плоских изгибов в двух взаимно перпендикулярных плоскостях инерции.
Для определения полного изгибающего момента M и полной поперечной силы Q при косом изгибе достаточно определить внутренние усилия для каждого из плоских изгибов в отдельности (то есть Qy, Mz и Qz, My), а затем найти их векторную сумму:
Определение напряжений при косом изгибе
Если разложить внешние силы по главным осям инерции Ох и Оу, то получим две системы сил P1x, P2x, …, Pnx и P1y, P2y,..., Pny, каждая из.которых вызывает прямой изгиб с изгибающими моментами соответственно My и Мx (рис.7.6). Применяя принцип независимости действия сил, нормальные напряжения (рис.7.7) определим как алгебраическую сумму напряжений от Mx и Мy:
7.2. Изгиб с растяжением (сжатием)
Если нагрузить брус в главной плоскости силой F (рис. 7.5,а) под углом α к оси, то в поперечном сечении 1-1 (рис. 7.5,б) возникнут два внутренних силовых фактора: нормальная сила N =F∙cosα и изгибающий момент Mz = F∙xsinα. Следовательно, такое нагружение бруса вызывает сочетание изгиба с растяжением (сжатием).
Считая, что брус обладает большой жесткостью при изгибе (малые величины прогиба бруса), согласно принципу независимости действия сил, можно утверждать, что в любом сечении возникают напряжения растяжения (сжатия):
и напряжения изгиба
Рис. 7.5
Считая, что брус обладает большой жесткостью при изгибе (малые величины прогиба бруса), согласно принципу независимости действия сил, можно утверждать, что в любом сечении возникают напряжения растяжения (сжатия):
и напряжения изгиба
Таким образом, суммарные напряжения в любом сечении бруса находят алгебраическим сложением напряжений σN и σMZ:
При расчетах на прочность исходят из наибольших напряжений, возникающих в любом сечении. В частности, если сечение бруса симметрично относительно нейтральной оси, то
Необходимо учитывать, что в последних двух формулах значения напряжений берутся со своими знаками плюс или минус.
7.3. Внецентренное сжатие или растяжение
Вторым практически важным случаем сложения деформаций от изгиба и от продольных сил является так называемое внецентренное сжатие или растяжение, вызываемое одними продольными силами. Этот вид нагружения довольно распространен в технике, так как в реальной ситуации почти невозможно приложить растягивающую нагрузку точно в центре тяжести.
Внецентренным растяжением-сжатием называется случай, когда равнодействующая сил, приложенных к отброшенной части стержня, направлена параллельно оси стержня, но не совпадает с этой осью (рис.7.6).
Рис.7.6
Представим, что после проведения разреза равнодействующая Р сил действующих на отброшенную часть и приложенная к оставшейся проходит через точку с координатами (xp; yp) в главных центральных осях поперечного сечения (рис. 7.7).
центральных осях поперечного сечения (рис. 7.8).
Рис.7.7
Приведем силу Р в центр тяжести сечения, т.е. направим вдоль оси стержня (сила N). При этом появятся две пары сил относительно главных центральных осей (рис.7.8).
Таким образом, в поперечном сечении стержня при внецентренном растяжении и сжатии возникают три внутренних силовых фактора: нормальная сила N и два изгибающих момента относительно главных центральных осей поперечного сечения.
Для вычисления нормального напряжения в поперечном сечении в окрестности точки с произвольными координатами x,y воспользуемся принципом независимости действия сил. Будем вычислять нормальное напряжение от каждого внутреннего силового фактора в отдельности и результат сложим.
Рис.7.8
7.4. Критерии предельного состояния материала при сложном напряженном состоянии.
Теории прочности. Гипотезы (теории) прочности
Критерии разрушения или гипотезы прочности представляют собой предположения о преимущественном влиянии на прочность материалов того или иного фактора, сопутствующего процессу деформации и разрушения материалов.
Наиболее важными факторами, связанными с возникновением опасного состояния материала, являются: нормальные и касательные напряжения, линейные деформации и потенциальная энергия деформации.
При сложном напряженном состоянии следует говорить не о предельном напряжении, а о предельном напряженном состоянии. В качестве предельного состояния в опасной точке детали принимается переход материала в окрестности данной точки из упругого состояния в пластическое или разрушение детали, выражающееся в образовании трещин.
Теория наибольших нормальных напряжений (I теория прочности, Галилей, 1638 г.)
В основу теории наибольших нормальных напряжений положена гипотеза о преимущественном влиянии наибольших по абсолютной величине нормальных напряжений.
Согласно данной теории прочности опасное состояние материала при сложном напряженном состоянии наступает тогда, когда наибольшее из главных напряжений достигает величины, соответствующей пределу прочности при простом растяжении.
В этом случае условие прочности должно иметь вид:
- при растяжении, (14)
- при сжатии. (15)
Данная гипотеза удовлетворительно согласуется с результатами испытания деталей из хрупких материалов, таких как камень, кирпич, чугун. Для расчета деталей из пластичных материалов данная гипотеза непригодна.
Теория наибольших линейных деформаций (II теория прочности, Мариотт, 1682 г.)
В основу теории наибольших линейных деформаций положена гипотеза о преимущественном влиянии наибольших по абсолютной величине линейных деформаций.
Согласно данной теории прочности опасное состояние материала при сложном напряженном состоянии наступает тогда, когда наибольшее из относительных удлинений достигает опасной величины, соответствующей пределу прочности при простом растяжении.
Опыты этого не подтверждают. В связи с этим данная теория для расчета деталей не используется.
Теория наибольших касательных напряжений (III теория прочности; Кулон, 1773 год)
В основу теории наибольших касательных напряжений положена гипотеза о преимущественном влиянии наибольших по абсолютной величине касательных напряжений.
Согласно данной теории прочности опасное состояние материала при сложном напряженном состоянии наступает тогда, когда наибольшее из касательных напряжений достигает величины, соответствующей пределу текучести при простом растяжении.
Предельное значение максимальных касательных напряжений при растяжении
Сравнивая с условием наступления предельного состояния (13), получим эквивалентное напряжение по III теории прочности:
На практике встречаются случаи, когда σy =0, тогда
Условие прочности (31) хорошо согласуется с результатами испытания изотропных материалов, поэтому данная теория широко применяется для расчета деталей из металлических материалов.
Теория наибольшей удельной потенциальной энергии формоизменения (IV теория прочности; Бельтрами - 1885 г.; Губер - 1904 г.)
В основу энергетической теории прочности положена гипотеза о преимущественном влиянии удельной потенциальной энергии изменения формы.
Согласно данной теории прочности опасное состояние материала при сложном напряженном состоянии наступает тогда, когда удельная потенциальная энергия изменения формы достигает величины, соответствующей пределу текучести при простом растяжении.
В частном случае, когда σy = 0, то, приняв σx = σ и τxy = τ, найдем
Рассмотренная теория хорошо согласуется с экспериментами для пластичных материалов и широко применяется на практике.
Теория прочности Мора (V теория прочности)
Теория прочности Мора позволяет учесть различие в свойствах материалов при растяжении и сжатии. Ее можно получить путем модификации теории наибольших касательных напряжений в соответствии с уравнением:
для пластичных материалов, или
для хрупких материалов.
Условие прочности по теории Мора имеет следующий вид:
Замечания о выборе теории прочности
Обзор многочисленных теорий предельных состояний показывает, что совершенных теорий еще нет. Каждая из существующих теорий справедлива только в определенных условиях и для определенных материалов. Рассмотренными выше теориями можно пользоваться только при напряженных состояниях с главными напряжениями разных знаков. Возможность применения этих теорий в случаях трехосного растяжения или сжатия требует дополнительной экспериментальной проверки.
При выборе теории прочности в случае плоского напряженного состояния и объемного напряженного состояния с главными напряжениями разных знаков надо учитывать свойства материала. Если материал пластичен и одинаково работает на растяжение и сжатие, то следует пользоваться теорией наибольшей энергии формоизменения или теорией максимальных касательных напряжений. Если пластичный материал неодинаково сопротивляется растяжению и сжатию, то следует применить теорию Мора. Расчет хрупких материалов при указанных напряженных состояниях следует производить по теории Мора.
Совместные действия изгиба и кручения стержня
В случае изгиба с кручением от крутящего момента в поперечных сечениях бруса возникают касательные напряжения, которые рассчитываются по разному для круглых и прямоугольных брусьев. Вследствие этого, рассматривать расчет сечений произвольной формы не представляется возможным.
Кручение с изгибом – частный случай сложного сопротивления, который может рассматриваться как сочетание чистого кручения и поперечного изгиба.
Рис.7.9
Определение внутренних усилий и напряжений при кручении с изгибом
Для определения внутренних усилий воспользуемся методом сечений:
Обычно две составляющие поперечной силы (Qy, Qz) и изгибающего момента (My, Mz) приводят к их полным результирующим
Расчет валов круглого (кольцевого) поперечного сечения на кручение с изгибом
Исследуем этот вид деформации стержня на примере расчета вала кругового (кольцевого) поперечного сечения на совместное действие изгиба и кручения.
У кругового и кольцевого поперечного сечений все центральные оси главные, поэтому косого изгиба у вала вообще не может быть, следовательно, нет смысла в каждом сечении иметь два изгибающих момента Mx, и My, а целесообразно их заменить результирующим (суммарным) изгибающим моментом (рис.7.9)
Опасное сечение при кручении с изгибом устанавливается из совместного анализа эпюр крутящего Mx и полного изгибающего Mи моментов. Если в сечении вала постоянного диаметра с наибольшим изгибающим моментом М действует наибольший крутящий момент Мкр, то это сечение является опасным.
Наибольшие напряжения изгиба возникают в точках наиболее удаленных от нейтральной оси
где Wизг — момент сопротивления при изгибе.
В этих же точках имеют место и наибольшие касательные напряжения кручения
где Wр — момент сопротивления при кручении.
Условие прочности по III гипотезе записывается в виде
или
где - эквивалентный момент по третьей гипотезе прочности.
Условие прочности по IV гипотезе прочности записывается в виде
или
где - эквивалентный момент по четвертой гипотезе прочности.
ВОПРОСЫ ДЛЯ САМОПРОВЕРКИ
- Что такое сложное сопротивление стержней?
- Какие виды деформации бруса называют сложным сопротивлением?
- Сформулируйте принципы, на которых строится расчет брусьев при сложном сопротивлении?
- В чем заключается принцип независимости действия сил?
- Опишите методику определения компонентов внутренних сил при сложном сопротивлении?
- Какой изгиб называется косым?
- Какие точки сечения будут опасными при косом изгибе?
- Как записывают условия прочности при косом изгибе для балки из пластичного материала?
- По каким формулам определяются нормальные напряжения в поперечных сечениях балки при косом изгибе?
- Какой вид сложного сопротивления называется внецентренным растяжением (или сжатием)?
- К каким равнодействующим приводятся внутренние силы при внецентренном растяжении (или сжатии)?
- Какие виды напряжений испытывает сжимаемый стержень при внецентренном приложении сжимаемой или растягиваемой нагрузки?
- По каким формулам определяются нормальные напряжения в поперечных сечениях стержня при внецентренном растяжении и сжатии? Какой вид имеет эпюра этих напряжений?
- Как определить положение наиболее напряженной (опасной) точки сечения бруса при внецентренном растяжении (сжатии)?
- Как составить условие прочности бруса при внецентренном растяжении (сжатии)?
- Какие напряжения возникают в поперечном сечении бруса при изгибе с кручением?
- Как находятся опасные сечения бруса круглого сечения при изгибе с кручением?
- Как выполняют проверку безопасной прочности при кручении с изгибом круглого бруса?
- Что представляет собой эквивалентное напряжение?
- Чем отличаются между собой различные теории прочности?
- Какое назначение имеют гипотезы предельных напряжений состояний (гипотезы прочности)?
- В чем заключается сущность гипотезы прочности максимальных касательных напряжений и энергетической гипотезы прочности?
- Как формулируется теория прочности удельной потенциальной энергии, идущей на изменение формы и условие прочности по ней?
- В чем состоит теория прочности Мора?
- В чем преимущество гипотезы прочности Мора?
8. Прочность при переменных и циклически изменяющихся напряжениях
8.1. Усталость и выносливость материалов
Многие детали машин и механизмов, а также конструкции сооружений в процессе эксплуатации подвергаются циклически изменяющимся во времени воздействиям. Если уровень напряжений, вызванный этими воздействиями, превышает определенный предел, то в материале формируются необратимые процессы накопления повреждений, которые в конечном итоге приводят к разрушению системы.
Процесс постепенного накопления повреждений в материале под действием переменных напряжений, приводящих к разрушению, называется усталостью. Свойство материала противостоять усталости называется выносливостью.
Для раскрытия физической природы процесса усталостного разрушения в качестве примера рассмотрим ось вагона, вращающуюся вместе с колесами (рис. 8.1, а), испытывающую циклически изменяющиеся напряжения, хотя внешние силы и являются постоянными величинами. Происходит это в результате того, что части вращающейся оси оказываются попеременно то в растянутой, то в сжатой зонах.
Рис. 8.1
Опыт показывает, что при переменных напряжениях после некоторого числа циклов может наступить разрушение детали, в то время как при том же неизменном во времени напряжении разрушения не происходит.
Рис.8.2
Число циклов до момента разрушения зависит от величины и меняется в весьма широких пределах. При больших напряжениях для разрушения бывает достаточно 5-10 циклов. Это хорошо видно хотя бы на примере многократного изгиба куска проволоки (рис.8.2).
При меньших напряжениях деталь выдерживает миллионы и миллиарды циклов, а при еще меньших — способна работать неограниченно долго.
После разрушения на поверхности излома детали обнаруживаются обычно две ярко выраженные зоны (рис.8.3 и 8.4). В одной зоне кристаллы различаются невооруженным глазом с большим трудом. Поверхность излома имеет сглаженные очертания. В другой зоне явно выступают признаки свежего хрупкого разрушения. Кристаллы имеют острую огранку и блестящую чистую поверхность.
В целом создается первое впечатление, что подобного рода разрушение связано с изменением кристаллической структуры металла. Именно этим и объяснялось в свое время разрушение при циклических напряжениях. Описанное явление получило тогда название усталости, а направление исследований, связанных с прочностью, стало называться усталостной прочностью. В дальнейшем точка зрения на причины усталостного разрушения изменилась, но сам термин сохранился.
В настоящее время установлено, что структура металла при циклических нагрузках не меняется. Начало разрушения носит чисто местный характер и во многом связан с неоднородностью реальной структуры материалов (различие размеров, очертаний, ориентации соседних зерен металла; наличие различных включений – шлаков, примесей; дефекты кристаллической решетки, дефекты поверхности материала – царапины, коррозия и т. д.). В связи с указанной неоднородностью при переменных напряжениях на границах отдельных включений и вблизи микроскопических пустот и различных дефектов возникает концентрация напряжений, которая приводит к микропластическим деформациям сдвига некоторых зерен металла (при этом на поверхности зерен могут появляться полосы скольжения) и накоплению сдвигов (которое на некоторых материалах проявляется в виде микроскопических бугорков и впадинок – экструзий и интрузий); затем происходит развитие сдвигов в микротрещины, их рост и слияние; на последнем этапе появляется одна или несколько макротрещин, которая достаточно интенсивно развивается (растет). Края трещины под действием переменной нагрузки притираются друг об друга, и поэтому зона роста трещины отличается гладкой (полированной) поверхностью. По мере роста трещины поперечное сечение детали все больше ослабляется, и, наконец, происходит внезапное хрупкое разрушение детали, при этом зона хрупкого долома имеет грубозернистую кристаллическую структуру (как при хрупком разрушении).
Из фотографии (рис.8.3) видно, что разрушение бруса произошло в результате развития трещины, образовавшейся у края сечения. Разрушение рельса (рис.8.4) обусловлено развитием трещины, образовавшейся внутри сечения в зоне местного порока.
Теоретический анализ усталостной прочности связан с большими трудностями. Природа усталостного разрушения обусловлена особенностями молекулярного и кристаллического строения вещества. Поэтому схема сплошной среды, которая с успехом применялась в рассматривавшихся до сих пор задачах, в данном случае не может быть принята в качестве основы для исследования.
Рис. 8.3
Рис. 8.4
8.2. Основные характеристики цикла и предел усталости
Рассмотрим вначале случай одноосного напряженного состояния.
Закон изменения главного напряжения о во времени представлен кривой, показанной на рис.8.5.
Наибольшее и наименьшее напряжения цикла обозначим через и . Их отношение называется коэффициентом цикла .
Рис.8.5
В случае, когда и цикл называется симметричным. Такой цикл, в частности, имеет место в рассмотренном выше примере вращающейся оси вагона). Если или же , цикл называется пульсационным (рис. 8.6). Для пульсационного цикла r = 0 или . Циклы, имеющие одинаковые показатели r, называются подобными.
Рис.8.6
Любой цикл может быть представлен как результат наложения постоянного напряжения на напряжение, меняющееся по симметричному циклу с амплитудой (рис. 8.6). Очевидно, при этом:
Путем многократных испытаний (если имеется достаточное количество образцов) можно определить число циклов, которое выдерживает образец до разрушения, в зависимости от величины цикла. Эта зависимость имеет вид кривой, показанной на рис.8.7 и называется диаграммой усталостного разрушения Велера.
Рис. 8.7
Опыт показывает, что для большинства черных металлов можно указать такое наибольшее максимальное напряжение, при котором материал не разрушается при любом числе циклов. Такое напряжение называется пределом усталости, или пределом выносливости.
Предел выносливости обозначается через , где индекс r соответствует коэффициенту цикла. Так, для симметричного цикла обозначение предела выносливости принимает вид , для пульсирующего или и т. д.
Для цветных металлов и для закаленных до высокой твердости сталей не удается установить такое число циклов, выдержав которое, образец не разрушился бы в дальнейшем. Поэтому в подобных случаях вводится понятие условного предела выносливости. За условный предел выносливости принимается напряжение, при котором образец способен выдержать 108 циклов.
Обычно считается, что для сталей предел выносливости при изгибе составляет половину от предела прочности:
Для цветных металлов предел выносливости изменяется в более широких пределах:
Аналогично испытанию на чистый изгиб можно вести испытание на кручение в условиях циклически изменяющихся напряжений. В этом случае:
или для обычных сталей берется , для хрупких материалов (высоколегированная сталь, чугун) .
8.3.Расчет коэффициентов запаса усталостной прочности
Одним из основных факторов, которые необходимо учитывать при практических расчетах на усталостную прочность, является фактор местных напряжений.
Рис. 8.8. Очаги концентрации местных напряжений:
а) растяжение, б) изгиб, в) контактные напряжения
Многочисленные теоретические и экспериментальные исследования показывают, что в области резких изменений в форме упругого тела (входящие углы, отверстия, выточки), а также в зоне контакта деталей возникают повышенные напряжения с ограниченной зоной распространения, так называемые местные напряжения.
Например, при растяжении полосы с небольшим отверстием (рис.8.8, а) закон равномерного распределения напряжений вблизи отверстия нарушается. Напряженное состояние становится двухосным, а у края отверстия появляется пик напряжения. Аналогично при изгибе ступенчатого стержня (рис. 8.8, б) в зоне входящего угла возникает повышенное напряжение, величина которого зависит в первую очередь от радиуса закругления r. При прессовой посадке втулки на вал (рис. 8.8, в) у концов втулки и вала также возникают местные напряжения. Подобных примеров можно привести очень много.
Величина местных напряжений в зависимости от геометрической формы детали определяется обычно теоретически при помощи методов математической теории упругости.
Основным показателем местных напряжений является теоретический коэффициент концентрации напряжений:
где — наибольшее местное напряжение, а — так называемое номинальное напряжение. Это - то напряжение, которое определяется по формулам сопротивления материалов без учета эффекта концентрации. Обычно подсчет ведется по наиболее ослабленному сечению детали.
Влияние состояния поверхности и размеров детали на усталостную прочность
Так как при циклических напряжениях начало разрушения связано с образованием местной трещины, понятна та роль, которую играет в усталостной прочности детали состояние ее поверхности. Совершенно очевидно, что в случае чистой и тонко обработанной поверхности предел усталости возрастает. При грубой обработке наличие мелких поверхностных дефектов приводит к снижению показателей усталостной прочности. При этом для материалов, обладающих большой чувствительностью к местным напряжениям, влияние состояния поверхности будет более заметным.
При расчетах на усталостную прочность особенности, связанные с обработкой поверхности детали, учитываются коэффициентом качества поверхности:
где — предел усталости, полученный на образцах, имеющих стандартную обработку поверхности. В качестве таковой — принимается обычно шлифовка. предел выносливости для образцов, состояние поверхности которых соответствует состоянию поверхности рассчитываемой детали.
При расчете детали на усталостную прочность наряду с фактором состояния поверхности необходимо учитывать также еще так называемый масштабный фактор.
Величина предела усталости зависит от абсолютных размеров испытываемых образцов. Объясняется это, как уже указывалось выше, тем, что усталостное разрушение определяется не только напряжением в наиболее опасных точках, но также и общими законами распределения напряжений в объеме тела в процессе образования и развития трещин.
Опыты, проведенные по определению предела усталости для образцов различных размеров, показали, что с увеличением последних предел усталости уменьшается.
Отношение предела усталости детали к пределу усталости образцов стандартного размера мм называется коэффициентом масштабного фактора, или просто масштабным фактором,
При определении масштабного фактора предполагается, что состояние поверхности испытываемых деталей и образцов одинаково.
ВОПРОСЫ ДЛЯ САМОПРОВЕРКИ
- Что называют усталостью материалов? В чем заключается физические причины усталости металлов?
- Почему многие детали машин имеют ограниченный срок службы (ресурс)?
- Как по виду излома детали узнать, что ее разрушение произошло от усталости?
- Объясните термин «долом»?
- Перечислить все характеристики цикла и указать зависимость между ними.
- Какой из различных по форме циклов напряжений самый неблагоприятный для работы детали?
- Какие напряжения называются циклическими?
- Что называется циклом напряжений? Какими величинами характеризуется цикл?
- Какой цикл называется симметричным, статическим, пульсирующим?
- Какие циклы называют симметричным и отнулевым?
- Что называется коэффициентом асимметрии цикла?
- Что представляет собой кривая усталостной прочности?
- Что называют пределом выносливости?
- Какую величину называют базовым числом циклов?
- Что представляет собой кривая усталости? Как ее строить?
- Что такое предел выносливость материала? Как он определяется?
- Какие факторы влияют на предел выносливости материала?
- Как строится диаграмма усталостной прочности?
- Как определяется коэффициент запаса прочности при действии на деталь циклической нагрузки?
- Влияние размеров, формы, шероховатости на величину предела выносливости.
- В чем заключается влияние абсолютных размеров поперечного сечения детали на предел выносливости?
- Почему на предел выносливости детали влияет шероховатость ее поверхности?
- Как учитывают совместное влияние различных факторов на предел выносливости детали?
9. теория машин и механизмов
9.1. Инженерное проектирование. Машина и механизм.
Теория механизмов и машин - научная дисциплина (или раздел науки), которая изучает строение (структуру), кинематику и динамику механизмов в связи с их анализом и синтезом (И.И.Артоболевский).
Цель ТММ - анализ и синтез типовых механизмов и их систем.
Задачи ТММ:
- создание робототехнических систем, связывающих отдельные технологические операции в единую цепь полностью автоматизированного производства;
- изучение совместной работы машин и управляющих ЭВМ, разработка необходимых алгоритмов и программ для функционирования автоматизированного производства;
- создание методов структурного, кинематического, динамического анализа и синтеза различных схем механизмов роботов, манипуляторов, шагающих и других машин и систем.
Типовыми механизмами будем называть простые механизмы, имеющие при различном функциональном назначении широкое применение в машинах, для которых разработаны типовые методы и алгоритмы синтеза и анализа.
Рассмотрим в качестве примера кривошипно-ползунный механизм. Этот механизм широко применяется в различных машинах: двигателях внутреннего сгорания, поршневых компрессорах и насосах, станках, ковочных машинах и прессах.
Основные разделы курса ТММ
- структура механизмов и машин;
- геометрия механизмов и их элементов;
- кинематика механизмов;
- динамика машин и механизмов.
Связь курса ТММ с общеобразовательными, общеинженерными и специальными дисциплинами.
Лекционный курс ТММ базируется на знаниях полученных студентом на младших курсах при изучении физики, высшей и прикладной математики, теоретической механики, инженерной графики и вычислительной техники. Знания, навыки и умение приобретенные студентом при изучении ТММ служат базой для курсов детали машин, подъемно-транспортные машины, системы автоматизированного проектирования, проектирование специальных машин и основы научных исследований.
Понятие о инженерном проектировании
Инженерное проектирование - это процесс, в котором научная и техническая информация используется для создания новой системы, устройства или машины, приносящих обществу определенную пользу.
Проектирование (по ГОСТ 22487-77) - это процесс составления описания, необходимого для создания еще несуществующего объекта (алгоритма его функционирования или алгоритма процесса), путем преобразования первичного описания, оптимизации заданных характеристик объекта (или алгоритма его функционирования), устранения некорректности первичного описания и последовательного представления (при необходимости) описаний на различных языках.
Проект (от латинского projectus - брошенный вперед) - совокупность документов и описаний на различных языках (графическом - чертежи, схемы, диаграммы и графики; математическом - формулы и расчеты; инженерных терминов и понятий - тексты описаний, пояснительные записки), необходимая для создания какого-либо сооружения или изделия.
Методы проектирования
1) Прямые аналитические методы синтеза (разработаны для ряда простых типовых механизмов);
2) Эвристические методы проектирования - решение задач проектирования на уровне изобретений (например, алгоритм решения изобретательских задач);
3) Синтез методами анализа - перебор возможных решений по определенной стратегии (на пример, с помощью генератора случайных чисел – метод Монте-Карло) с проведением сравнительного анализа по совокупности качественных и эксплуатационных показателей (часто используются методы оптимизации - минимизация сформулированной разработчиком целевой функции, определяющей совокупность качественных характеристик изделия);
4) Системы автоматизированного проектирования или САПР - компьютерная программная среда моделирует объект проектирования и определяет его качественные показатели, после принятия решения - выбора проектировщиком параметров объекта, система в автоматизированном режиме выдает проектную документацию.
Основные этапы процесса проектирования
При проектировании новой техники возникает необходимость проведения работ, связанных с анализом и синтезом новой конструкции.
Анализ осуществляется при заданных размерах и массе звеньев, когда необходимо определить: скорости, ускорения, действующие силы, напряжения в звеньях и их деформации. В результате может быть произведен проверочный расчет на прочность, выносливость и т.д.
Синтез осуществляется при заданных скоростях, ускорениях, действующих силах, напряжениях или деформациях. При этом требуется определить необходимые размеры звеньев, их форму и массу.
Для механической системы элементами могут быть: деталь, звено, группа, узел, простой или типовой механизм.
Деталь - элемент конструкции не имеющий в своем составе внутренних связей (состоящий из одного твердого тела).
Звено - твердое тело или система жестко связанных твердых тел (может состоять из одной или нескольких деталей) входящая в состав механизма.
Группа - кинематическая цепь, состоящая из подвижных звеньев, связанных между собой кинематическими парами (отношениями), и удовлетворяющая некоторым заданным условиям.
Узел - несколько деталей связанных между собой функционально, конструктивно или каким-либо другим образом.
Расположения - такие отношения между элементами, которые описывают их геометрические относительные положения.
Связи - отношения между элементами. Механические соединения могут быть подвижными (кинематические пары) и неподвижными.
9.2. Машины и их классификация
По мере развития машин содержание термина "машина" изменялось.
Для современных машин дадим следующее определение: машина есть устройство, создаваемое человеком для преобразования энергии, материалов и информации с целью облегчения физического и умственного труда, увеличения его производительности и частичной или полной замены человека в его трудовых и физиологических функциях.
Условно все машины можно разделить на технологические, транспортные, энергетические, информационные. С помощью технологических машин (например, металлообрабатывающие станки, землеройные машины и т.д.) происходит изменение форм, размеров, свойств, состояния исходных материалов и заготовок, подвергшихся воздействию рабочего (исполнительного) органа машины. С помощью транспортных машин происходит перемещение грузов по заданной траектории с требуемыми скоростью или ускорением. В энергетических машинах происходит преобразование энергии (например, электрической в механическую – в станках с электроприводом, тепловой в механическую – в тракторах и автомобилях с двигателями внутреннего сгорания и т.д.). В информационных машинах происходит преобразование вводимой информации для контроля, регулирования режима работы машины и управления движением.
Машина в общем виде состоит из основных частей: машина-двигатель, передаточный механизм, исполнительное устройство (механизм) и система управления. Такую машину называют механическим приводом. Машина-двигатель преобразует какой-либо вид энергии в механическую (электродвигатель, двигатель внутреннего сгорания, гидромотор и т.д.). Передаточный механизм преобразует движение (например, кулачковый, зубчатый, рычажный механизмы). Исполнительный механизм непосредственно обеспечивает выполнение технологического процесса, для которого предназначен механический привод.
В некоторых машинах передаточный механизм отсутствует (например, вентилятор, состоящий из электродвигателя с насаженной на вал крыльчаткой).
Энергетические машины - преобразующие энергию одного вида в энергию другого вида. Эти машины бывают двух разновидностей:
Двигатели, которые преобразуют любой вид энергии в механическую (например, электродвигатели преобразуют электрическую энергию, двигатели внутреннего сгорания преобразуют энергию расширения газов при сгорании в цилиндре).
Кибернетические машины (рис.1.8) - машины управляющие рабочими или энергетическими машинами, которые способны изменять программу своих действий в зависимости от состояния окружающей среды (т.е. машины обладающие элементами искусственного интеллекта).
Механизм и его элементы
В учебной литературе используются несколько определений механизма:
Первое: Механизмом называется система твердых тел, предназначенная для передачи и преобразования заданного движения одного или нескольких тел в требуемые движения других твердых тел.
Второе: Механизм - кинематическая цепь, в состав которой входит неподвижное звено (стойка) и число степеней свободы которой равно числу обобщенных координат, характеризующих положение цепи относительно стойки.
Третье: Механизмом называется устройство для передачи и преобразования движений и энергий любого рода.
Четвертое: Механизм - система твердых тел, подвижно связанных путем соприкосновения и движущихся определенным, требуемым образом относительно одного из них, принятого за неподвижное.
Механизмом называется система, состоящая из звеньев и кинематических пар, образующих замкнутые или разомкнутые цепи, которая предназначена для передачи и преобразования перемещений входных звеньев и приложенных к ним сил в требуемые перемещения и силы на выходных звеньях. Например, кривошипно-шатунный механизм двигателя внутреннего сгорания превращает поступательное движение поршня во вращательное движение коленчатого вала, а механизм подачи токарного станка − вращательное движение ходового винта в поступательное движение резца.
Механизм называется плоским, если все его звенья движутся параллельно одной плоскости и траектории всех его точек – плоские кривые. В пространственных механизмах подвижные точки их звеньев описывают неплоские траектории или траектории, лежащие в пересекающихся плоскостях.
Деталь – это изделие, изготовленное без сборочных операций.
Звено – одна или несколько неподвижно соединенных друг с другом деталей, входящих в механизм и движущихся, как одно целое.
Звено может состоять из одной или нескольких деталей, образующих между собой неподвижные соединения (резьбовые, прессовые, сварные и т.д.). Одним звеном в механизме считается любая совокупность деталей, не имеющих между собой относительного движения, например, детали, лежащие на ленте конвейера.
Стойка - звено, которое при исследовании механизма принимается за неподвижное. Так, например, корпус двигателя, подшипники коленчатого вала и т.п. образуют одно неподвижное звено, или стойку.
Рычажные механизмы
Рычажными механизмами называют механизмы, в которые входят жесткие звенья, соединенные между собой вращательными и поступательными кинематическими парами. Значительную часть плоских рычажных механизмов, которые получили наибольшее распространение на практике, составляют шарнирные механизмы, звенья которых соединены только вращательными парами.
Простейшим шарнирным рычажным механизмом является двухзвенный механизм, состоящий из неподвижного звена-стойки 2 (рис. 9.1) и подвижного рычага 1, имеющего возможность вращаться вокруг неподвижной оси (обычно это начальный механизм).
Рис. 9.1. Двухзвенный рычажный механизм
Рис. 9.2. Механизм шарнирного четырехзвенника
Более сложными рычажными механизмами являются механизмы, состоящие из четырех звеньев, так называемые четырехзвенные механизмы.
На рис. 9.2 показан механизм шарнирного четырехзвенника, состоящего из трех подвижных звеньев 1, 2, 3 и одного неподвижного звена 4. Звено 1, соединенное со стойкой, может совершать полный оборот и носит название кривошипа. Применяется в прессах, ковочных машинах, качающихся конвейерах, прокатных станах, муфтах сцепления, приборах и т.д.
Другим примером четырехзвенника является широко распространенный в технике кривошипно-ползунный механизм (рис. 9.3).
Рис. 9.3. Кривошипно-ползунный механизм
Кулачковые механизмы
Широкое распространение в технике получили кулачковые механизмы. Кулачковые механизмы предназначены для преобразования вращательного движения ведущего звена (кулачка) в заведомо заданный закон возвратно-поступательного движения ведомого звена (толкателя). Широко применяются кулачковые механизмы в швейных машинах, двигателях внутреннего сгорания, автоматах и позволяют получить заведомо заданный закон движения толкателя, а также обеспечить временные остановы ведомого звена при непрерывном движении ведущего.
Простейший кулачковый механизм – трехзвенный, состоящий из кулачка, толкателя и стойки. Входным звеном чаще всего бывает кулачок. Кулачковые механизмы бывают как плоскими, так и пространственными.
Плоские кулачковые механизмы для удобства рассмотрения разобьем на механизмы в зависимости от движения выходного звена на два вида:
1.Кулачковый механизм с поступательно движущимся толкателем (ползуном).
2. Кулачковый механизм с поворачивающимся толкателем (коромыслом).
Рис. 9.4. Механизм с поступательно-движущимся толкателем
Пример первого кулачкового механизма показан на рис. 9.4. Кулачок 1, вращаясь с заданной угловой скоростью, действует на ролик 3 и заставляет толкатель 2 в виде ползуна двигаться в направляющих возвратно-поступательно.
На рис. 9.5 приведена схема кулачкового механизма с поворачивающимся толкателем (коромыслом). Кулачок 1, вращаясь с заданной угловой скоростью ω1, действует на толкатель 2 и заставляет последний вращаться вокруг оси вращения А.
Рис. 9.5. Кулачковый механизм с поворачивающимся толкателем
Кулачковые механизмы имеют разновидности в зависимости от геометрических форм элемента выходного (ведомого) звена и взаимного расположения толкателя и кулачка. Например, кулачковый механизм, показанный на рис.4 может иметь разные виды ведомых звеньев (рис. 9.6).
Рис. 9.6. Виды ведомых звеньев, применяемые для кулачковых механизмов
с поступательно движущимся выходным звеном: а) толкатель с острием;
б) с плоскостью; в) толкатель с роликом; г) толкатель со сферическим наконечником.
Кулачковые механизмы с поступательно движущимся ведомым звеном можно разделить на:
кулачковые механизмы с центральным толкателем, у которых направление движения толкателя совпадает с осью вращения кулачка (рис. 9.7);
кулачковые механизмы со смещенным толкателем (дезаксиальные), если ось толкателя отстоит на расстояние е – дезаксиал от оси вращения кулачка (рис. 9.8).
Рис. 9.7. Кулачковый механизм с центральным толкателем
Рис. 9.8. Кулачковый механизм со смещенным толкателем
При работе кулачковых механизмов необходимо, чтобы было постоянное соприкосновение ведущего и ведомого звеньев. Это может быть обеспечено либо силовым замыканием, чаще всего с помощью пружин (рис. 9.9), либо геометрически, если выполнить профиль кулачка 1 в форме паза, боковые поверхности которого воздействуют на ролик 3 толкателя 2.
Рис. 9.9. Кулачковый механизм с силовым замыканием
Рис. 9.10. Кулачковый механизм с геометрическим замыканием
Пазовый кулачок обеспечивает геометрическое замыкание высшей пары кулачкового механизма (рис. 9.10).
Передачи вращения
Передачи вращения имеют широкое распространение в машиностроении.
Фрикционные передачи
Во фрикционных передачах передача вращательного движения между звеньями (катками – роликами) осуществляется вследствие трения возникающего между ними. На рис. 9.11 показан фрикционная передача с цилиндрическими катками. Передача движения от ведущего катка 1 к ведомому катку 2 осуществляется силой трения, возникающей под действием пружины с силой равной Q.
Нами рассмотрена фрикционная передача с цилиндрическими катками для передачи вращательного движения между параллельными валами. В передачах же с пересекающимися осями применяют фрикционные передачи с коническими катками.
Рис. 9.11. Фрикционная передача с цилиндрическими катками
Достоинствами фрикционной передачи являются плавность работы, простота конструкции, невозможность поломки при резком изменении крутящего момента на одном из валов благодаря возможности проскальзывания катков и возможность осуществления бесступенчатого изменения передаточного отношения, а также реверсирования. Поэтому фрикционные передачи широко применяют в машиностроении в качестве вариаторов. Простейший вариатор, называемый лобовым (рис. 9.12), состоит из диска 1 и ролика 2.
Ролик можно смещать вдоль оси О2, следствием чего точка контакта М может занимать различные положения, определяемые расстоянием x. Это позволяет плавно регулировать величину и направление угловой скорости выходного звена.
Рис. 9.12. Лобовая фрикционная передача
В процессе эксплуатации фрикционных передач, вследствие перегрузки или попадания масла на них, может наблюдаться проскальзывание одного катка относительно другого. Поэтому фрикционные передачи не обеспечивают постоянства передаточного отношения между ведущим и ведомым валами, что является существенным недостатком, который отсутствует у зубчатых передач.
Недостатками также являются: необходимость прижимного устройства, невозможность передачи значительных крутящих моментов.
В связи с указанными недостатками фрикционные передачи не получили такого широкого распространения как зубчатые.
Зубчатые передачи
Самое широкое применение в машинах и приборах находят зубчатые передачи которые позволяют передавать вращательные движения от одного вала к другому с заданными угловыми скоростями.
Зубчатые передачи получили наибольшее распространение в машиностроении благодаря следующим достоинствам:
а) практически неограниченной передаваемой мощности,
б) малым габаритам и весу,
в) стабильному передаточному отношению,
г) высокому КПД, который составляет в среднем 0,97 - 0,98.
Недостатком зубчатых передач является шум в работе на высоких скоростях.
При высоких угловых скоростях вращения рекомендуется применять косозубые шестерни, в которых зубья входят о зацепление плавно, что и обеспечивает относительно бесшумную работу. Недостатком косозубых шестерен является наличие осевых усилий, которые дополнительно нагружают подшипники.
На рис. 9.13 показаны цилиндрические колеса с внешним зацеплением, а на рис. 9.14 изображены цилиндрические колеса с внутренним зацеплением, где зубья одного из колес расположены по внутренней поверхности.
Рис. 9.13. Зубчатый механизм с внешним зацеплением
Рис. 9.14. Зубчатый механизм с внутренним зацеплением
Наряду с прямозубыми, широкое распространение получили зубчатые колеса с косыми и шевронными зубьями.
Зубчатая передача с реечным зацеплением имеет в составе зубчатую рейку 1 и зубчатое колесо 2 (рис. 9.15).
Рис.9.15. Зубчатый механизм с реечным зацеплением
Специальные многоступенчатые передачи имеют некоторые зубчатые колеса с подвижными осями (рис. 9.16). Здесь на подвижной оси О2 находится колесо 2, которое при вращении водила Н вокруг центральной оси О1 обегает неподвижное (опорное) колесо 3 и вращается вокруг собственной оси.
Рис. 9.16. Планетарный зубчатый механизм
Колеса 1 и 3 называются центральными колесами (солнечным и корончатым), колесо 2 сателлит или планетарное колесо. Рассматриваемая зубчатая передача называется планетарной и имеет одну степень подвижности, т.к. имеется неподвижное колесо 3. Достаточно задать закон движения одному звену, чтобы все остальные звенья двигались определенно и целесообразно.
Иными словами работу передачи следует описать так: центральное колесо 1 сообщает движение сателлиту 2, который обкатывается по колесу 3 и увлекает за собой по часовой стрелке водило.
Планетарные передачи компактны и используются для значительного уменьшения числа оборотов на выходе, при этом передаточные отношения могут быть более тысячи,
Планетарные передачи, в которых все колеса подвижны, обладают двумя степенями подвижности и называются дифференциальными передачами (рис. 9.17). Такая передача должна иметь заданными законы движения двух звеньев.
Рис. 9.17. Дифференциальный механизм
К зубчатым передачам относятся и устройства прерывистого движения: храповые механизмы, мальтийские механизмы и другие.
Храповые механизмы
Храповые механизмы относятся к механизмам прерывистого действия, которые обеспечивают движения ведомого звена в одном направлении с периодическими остановками. Конструктивно храповые механизмы делятся на нереверсивные с внутренним зацеплением и с храповым колесом, а также реверсивные в виде зубчатой рейки.
Нереверсивный храповый механизм с внутренним зацеплением (рис. 9.18). Ведущим звеном может быть как храповое колесо внутреннего зацепления 1, соединенное с зубчатым колесом внешнего зацепления, так и втулка 4 с закрепленной на ней собачкой 3, подпружиненной к зубьям храпового колеса 1 пружиной 2.
Рис. 9.18. Нереверсивный храповый механизм с внутренним зацеплением:
1 — храповое колесо; 2 — пружина; 3 — собачка; 4 — втулка
В нереверсивных механизмах (рис. 9.19) храповое колесо выполняют в виде рейки 1 в направляющих, и тогда собачка 2 сообщает рейке с храповым зубом прерывистое прямолинейное движение. В этом случае предусматривает устройство, которое возвращает рейку в начальное положение.
Рис. 9.19. Нереверсивный храповый механизм:
1 - рейка; 2 - собачка
Рис. 9.20. Реверсивный храповый механизм:
1- храповик; 2 - ведущий рычаг; 3 - собачка
Реверсивные храповые механизмы (рис. 9.20) имеют: храповое колесо 1 с зубьями эвольвентного профиля, а на ведущем рычаге 2 шарнирно устанавливают собачку 3, которую при необходимости реверса перебрасывают вокруг оси Ох.
Механизмы с гибкими звеньями
Ременные передачи
Механизмы с гибкими звеньями применяются при значительных межосевых расстояниях.
Рис. 9.21. Открытая ременная передача
На рис.9.21 показан простейший пример открытой ременной передачи, у которой вращение шкивов 1 и 2 происходит в одном и том же направлении.
Передача ремнем осуществляется за счет трения возникающего между шкивом и ремнем. Ремень может быть плоский, клиновой или зубчатый.
Все механические передачи характеризуются передаточным числом или отношением. Рассмотрим работу двух элементов передачи, один из которых будет ведущим, а второй — ведомым.
Введем следующие обозначения: ω1 и п1 — угловая скорость и частота вращения ведущего вала, выраженные соответственно рад/с и об/мин; ω1 и п2 — угловая скорость и частота вращения ведомого вала; D1 и D2 - диаметры вращающихся деталей (шкивов, катков и т. п.); v1 и v2 — окружные скорости, м/с.
Отношение диаметров ведомого элемента передачи к ведущему называют передаточным числом
Если известны параметры передачи — диаметры D1 и D2 или числа зубьев z1 и z2, передаточное число и определяем следующим образом.
Для зубчатых передач передаточное число и — отношение числа зубьев ведомого колеса к числу зубьев ведущего колеса, т.е. и = z2/z1, где z2 и z1 — числа зубьев соответственно ведомого и ведущего колеса.
Итак, передаточное число
(обратите внимание на индексы у букв ω, п, D и z); u=D2/D1 относится к фрикционной передаче без учета скольжения.
Отношение угловых скоростей ведущего ω1 и ведомого ω2 звеньев называют также передаточным отношением и обозначают і.
В передаче, понижающей частоту вращения n (угловую скорость ω), u>1; при и<1 частота вращения (угловая скорость) повышается. Понижение частоты вращения называют редуцированием, а закрытые передачи, понижающие частоты вращения,– редукторами. Устройства, повышающие частоты вращения, называют ускорителями или мультипликаторами. Передачи выполняют с постоянным, переменным или регулируемым передаточным отношением. Изменение передаточного отношения может быть ступенчатым (коробка передач) и бесступенчатым (вариаторы).
В приводах с большим передаточным числом (до и= 1000 и выше), составленных из нескольких последовательно соединенных передач (многоступенчатые передачи), передаточное число равно произведению передаточных чисел каждой ступени передачи, т. е.
Передача мощности от ведущего вала к ведомому всегда сопровождается потерей части передаваемой мощности вследствие наличия вредных сопротивлений (трения в движущихся частях, сопротивления воздуха и др.).
Если Р1 — мощность на ведущем валу, Р2 — на ведомом валу, то Р1 > Р2.
Отношение значений мощности на ведомом валу к мощности на ведущем валу называют механическим коэффициентом полезного действия (КПД) и обозначают буквой η:
Общий КПД многоступенчатой последовательно соединенной передачи определяют по формуле
где — КПД, учитывающие потери в отдельных кинематических парах передачи.
КПД характеризует качество передачи. Потеря мощности – показатель непроизводительных затрат энергии – косвенно характеризует износ деталей передачи, так как потерянная в передаче мощность превращается в теплоту и частично идет на разрушение рабочих поверхностей.
С уменьшением полезной нагрузки КПД значительно снижается, так как возрастает относительное влияние постоянных потерь (близких к потерям холостого хода), не зависящих от нагрузки;
9.3. Структура механизмов.
Понятие о структурном синтезе и анализе
Задачей структурного анализа является задача определения параметров структуры заданного механизма - числа звеньев и структурных групп, числа и вида КП, числа подвижностей (основных и местных), числа контуров и числа избыточных связей.
Задачей структурного синтеза является задача синтеза структуры нового механизма, обладающего заданными свойствами: числом подвижностей, отсутствием местных подвижностей и избыточных связей, минимумом числа звеньев, с парами определенного вида (например, только вращательными, как наиболее технологичными) и т.п.
Степень свободы и классы кинематических пар
Соединение двух соприкасающихся звеньев, допускающее их относительное движение, называется кинематической парой.
Совокупность поверхностей, линий и отдельных точек звена, по которым оно может соприкасаться с другим звеном, образуя кинематическую пару, называется элементом кинематической пары.
Если звенья подвижно соединяются в нескольких местах, то кинематическая пара является разветвленной, а отдельные части этого соединения называются ветвями кинематической пары.
Для абсолютно твердого тела, свободно движущегося в пространстве пространстве (в декартовой системе координат X, Y, Z), число независимых параметров, определяющих его положение в пространстве или число степеней свободы, равно шести (рис.22): три возможных перемещения вдоль неподвижных координатных осей X, Y и Z и три возможных вращения вокруг этих осей.
Рис. 9.22. Степени свободы тела в пространстве
Для звеньев, вошедших в кинематическую пару, число степеней свободы всегда меньше шести, так как кинематическая пара уменьшает число возможных перемещений и накладывает число условий связи S на относительное движение каждого звена, зависящих от способа соединения звеньев в пары. В таком случае число степеней свободы H кинематической пары равно
H = 6 − S. (1)
Все кинематические пары делятся на классы в зависимости от числа условий связи, налагаемых ими на относительное движение звеньев. Так как число условий связи может быть от одного до пяти, то число классов пар равно пяти. В соответствии с этим имеем кинематические пары I −V классов. Например, если телами (звеньями), образовавшими кинематическую пару, утрачено по 5 степеней свободы каждым, эту пару называют кинематической парой 5-го класса. Если утрачено 4 степени свободы – 4-го класса и т.д. (рис. 9.22). При S=0 пары не существует, а есть два тела, движущихся независимо друг от друга. При S=6 кинематическая пара становится жестким соединением двух звеньев, т.е. одним звеном.
Класс кинематической пары может быть определен из зависимости (1):
S = 6 – H. (2)
Классификация кинематических пар
Кинематические пары (КП) классифицируются по следующим признакам:
1) по виду места контакта (места связи) поверхностей звеньев:
- низшие, в которых контакт звеньев осуществляется по плоскости или поверхности (пары скольжения). К низшим парам относятся: вращательная, поступательная, винтовая, цилиндрическая, сферическая, плоскостная и т.п. (Пример низшей кинематической пары: два цилиндра, находящиеся в постоянном соприкосновении, из которых один вращается внутри другого).
- высшие, в которых контакт звеньев осуществляется по линиям или точкам (пары, допускающие скольжение с перекатыванием). Они имеются, например, в зубчатых и кулачковых механизмах. При этом линейный или точечный контакт понимается как первоначальный - при соприкосновении звеньев без усилия, а под нагрузкой звенья, образующие высшую пару, будут соприкасаться по некоторой фактической поверхности, называемой пятном контакта.
Рис. 9.23
Преимуществом низших кинематических пар по сравнению с высшими является возможность передачи больших нагрузок, поскольку контактная поверхность соприкасающихся звеньев низшей пары может быть весьма значительной, имеют большие потери на трение, сложнее синтезируются. Имеют простые формы в виде плоскостей, цилиндрических поверхностей, поэтому более технологичны, т. е. просты в изготовлении.
Таблица 9.1.
Условные обозначения кинематических пар
Класс пары |
Число условий связи |
Число степеней свободы |
Название пары |
Рисунок |
Условное обозначение |
I |
1 |
5 |
Шар-плоскость |
|
|
II |
2 |
4 |
Шар-цилиндр |
|
|
III |
3 |
3 |
Сферическая |
|
|
III |
3 |
3 |
Плоскостная |
|
|
IV |
4 |
2 |
Цилиндрическая |
|
|
IV |
4 |
2 |
Сферическая с пальцем |
|
|
V |
5 |
1 |
Поступательная |
|
|
V |
5 |
1 |
Вращательная |
|
|
V |
5 |
1 |
Винтовая |
|
|
Кинематической цепью называется система звеньев, связанных между собой кинематическими парами.
Механизм − это кинематическая цепь, в которой при заданном движении одного или нескольких звеньев относительно одного из них все остальные звенья совершают однозначно определяемые движения.
Степень свободы и структурная формула механизма
Число степеней свободы механизма – это число степеней свободы всей кинематической цепи относительно неподвижного звена (стойки).
Если на движение звена в пространстве не наложено никаких условий связи, то оно обладает шестью степенями свободы. Тогда если число звеньев кинематической цепи равно к, то общее число степеней свободы, которым обладают к звеньев до их соединения в кинематические пары, равно 6к. Соединение звеньев в кинематические пары накладывает различное число условий связи S на относительное движение звеньев, зависящее от класса пар.
Если число пар I класса, у которого S1=1, а H1=5, в которые входят звенья рассматриваемой кинематической цепи, равно р1, число пар II класса, у которого S1=2, а H1=4 – р2, число пар III класса, у которого S1=3, а H1=3 – р3, число пар IV класса, у которого S1=4, а H1=2 – р4, число пар V класса, у которого S1=5, а H1=1 – р5, то из 6к степеней свободы, которыми обладали звенья до вхождения в кинематические пары, необходимо исключить те степени свободы, которые отнимаются вхождением звеньев в кинематические пары. Тогда число степеней свободы Н кинематической цепи равно
Н = 6к - 5р5 - 4р4 - 3р3 - 2р2 – р1. (3)
Формула (3) − это формула подвижности или структурная формула кинематической цепи общего вида. Данная формула называется формула Малышева, получена П.И. Сомовым в 1887 году и развита А.П. Малышевым в 1923 году.
Число степеней свободы W механизма относительно неподвижного звена будет равно
W = H – 6 или W = 6(к-1) - 5p5 - 4p4 - 3p3 - 2p2 – p1
или
W = 6n -5p5 - 4p4 - 3p3 - 2p2 – p1, (4)
где n=k-1 − число подвижных звеньев кинематической цепи. Формула (4) носит название формулы подвижности, или структурной формулы механизма общего вида.
Величина W показывает, сколько должно быть у механизма ведущих звеньев (если W = 1 – одно, W = 2 – два ведущих звена и т.д.).
Когда три связи уже наложены условием параллельности осей, структурная формула будет такой:
W = (6-3)n - (5-3)p5 - (4-3)p4 - (3-3)p3,
или
W = 3n - 2p5 – p4. (5)
Формула (5) есть структурная формула для плоских механизмов общего вида. Формулу (5) называют также формулой П.Л. Чебышева (1869). Она может быть получена из формулы Малышева при условии, что на плоскости тело обладает не шестью, а тремя степенями свободы.
Показательным в этом отношении является пример зубчатого механизма планетарного типа, изображённый на рис. 9.24.
В состав механизма входит центральное колесо 1, являющееся ведущим, три параллельно работающих сателлита 2 и стержневое звено 3, образующее вращательные пары с сателлитами. Все подвижные звенья размещены внутри неподвижного колеса 0 с внутренними зубьями. Данные для расчёта таковы: количество пар 5-го класса p5=5 (они на схеме отмечены римскими цифрами), каждый сателлит 2 образует зацепление (две кинематические пары) с колёсами 0 и 1, поэтому p4=6, количество подвижных звеньев механизма n=5, количество степеней свободы механизма W=1.
Рис. 9.24
В результате расчёта получаем
q= (2p5 + p4) – (3n – W) = (2∙5 + 6) – (3∙5 - 1) = 2.
Таким образом, видим, что в данном механизме имеется две избыточных связи, это – два из трёх сателлитов, которые повторяют функции одного сателлита. Следует отметить, что в обоих механизмах избыточные связи играют положительную роль, разделяя общий силовой поток и уменьшая нагрузку на звенья.
9.4. Порядок структурного исследования плоского механизма
1) Пронумеровать все звенья механизма (если номера звеньев не указаны); неподвижному звену (стойке) обычно присваивают последний номер.
2) Рассчитать степень подвижности механизма w и проанализировать полученный результат; при наличии местных подвижностей и (или) пассивных связей избавиться от них, и повторить расчет w – в результате должна получиться фактическая степень подвижности механизма.
9.5. Кинематический анализ механизмов.
Цели и задачи кинематического анализа
Кинематический анализ механизма – исследование его основных параметров с целью изучения законов изменения и на основе этого выбор из ряда известных наилучшего механизма. По сравнению с синтезом анализ механизма широко используется в практике.
Цели:
1. Определение кинематических характеристик звеньев: перемещение; скорость; ускорение; траектория движения; функция положения при известных законах движения входных (ведущих) звеньев.
2. Оценка кинематических условий работы рабочего (выходного) звена.
3. Определение необходимых численных данных для проведения силового, динамического, энергетического и других расчётов механизма.
Исходные данные:
1. Кинематическая схема механизма.
2. Размеры и иные геометрические параметры звеньев (но только такие, которые не изменяются при движении механизма).
3. Законы движения входных звеньев (или параметры движения, например, угловая скорость и угловое ускорение входного звена в выбранном для анализа положении механизма).
Задачи:
- о положениях звеньев механизма. Определение траекторий движения точек;
- о скоростях звеньев или отдельных точек механизма;
- об ускорениях звеньев или отдельных точек механизма.
Методы:
- графический (или метод графиков и диаграмм);
- графоаналитический (или метод планов скоростей и ускорений);
- аналитический;
- экспериментальный.
Графический метод кинематического анализа
Преимущество этого метода заключается в наглядности и простоте. Он хорош для кинематического анализа звеньев, совершающих возвратно-поступательное движение. Недостаток метода – невысокая точность, которая зависит от точности графических построений.
Задача о положениях решается построением нескольких совмещённых планов механизма в выбранном масштабе длин при различных последовательных положениях ведущего звена.
Задачи о скоростях и ускорениях решаются построением графиков (диаграмм) перемещений, скоростей и ускорений исследуемой точки.
Последовательность кинематического анализа:
1. Сначала строят несколько (чаще всего 12 и более) совмёщенных планов механизма в произвольно выбранном масштабе длин.
2. Затем строят график пути (перемещения) исследуемой точки или звена, для чего используют совмещённые планы механизма и последовательные положения на них исследуемой точки или звена.
3. Графическим дифференцированием графика перемещений строят график скорости исследуемой точки.
4. Графическим дифференцированием графика скоростей строят график ускорений.
Графическое дифференцирование можно производить методом хорд и методом касательных. С целью повышения точности удобно использовать оба метода одновременно.
Пример
Даны кривошипно-ползунный механизм, длины звеньев которого – кривошипа и шатуна – LOA и LAB соответственно, и угловая скорость кривошипа .
Определить скорости и ускорения ползуна при различных положениях кривошипа.
Решение.
Выбираем масштабы длин , м/мм, где AO – длина отрезка, мм, изображающая кривошип длиной LОА на строящемся плане механизма; эта длина выбирается произвольно с учётом того, что совмещённые планы механизма должны разместиться на отведённом месте чертежа, а сам масштаб длин был бы удобен для дальнейших расчётов.
Вычисляем длину отрезка , мм, изображающего шатун на плане механизма. При построении совмещенных планов механизма используют метод засечек (рис. 9.25).
Для построения графиков скоростей и ускорений выбираются полюсные расстояния hu и ha, где hu – полюсное расстояние при построении графика скоростей, которое выбирается произвольной длины; рекомендуется его величину выбирать в пределах hu=30…40 мм; ha – полюсное расстояние при построении графика ускорений; его рекомендуется принимать в пределах ha=30…40 мм.
Масштабы времени, скорости и ускорения вычисляют по формулам, вывод которых приводится ниже.
Масштаб времени можно вычислить по формуле
,
где Т – период одного оборота кривошипа, с; LX – длина отрезка между точками 1 и 1 на графике (диаграмме) перемещений, мм.
Так как период Т можно вычислить по формулам
, или , с,
где – угловая скорость кривошипа, 1/с; n1 – частота вращения кривошипа, об/мин, то масштаб времени
, с/мм.
Масштаб скорости можно вывести из условия, что скорость исследуемой точки является производной перемещения S по времени:
.
Здесь предполагается, что масштаб перемещений и масштаб времени являются постоянными величинами.
Так как , то , отсюда
, .
Масштаб ускорения, вывод которого аналогичен предыдущему, вычисляется по формуле
, .
Для определения величины скорости или ускорения в каком-либо положении точки В необходимо длину ординаты соответствующего графика умножить на масштаб или соответственно.
Рис. 9.25 Совмещённые планы механизма, графики перемещений, скоростей и ускорений
Графоаналитический метод кинематического анализа
Графоаналитический метод называют методом планов скоростей и ускорений.
Задача о положениях решается графическим методом, то есть построением нескольких совмещённых планов механизма в выбранном масштабе длин.
Задачи о скоростях и ускорениях решаются построением планов скоростей и ускорений звеньев механизма при определённых (заданных) положениях ведущего звена на основе заранее составленных векторных уравнений скоростей и ускорений звеньев механизма.
Преимущество этого метода по сравнению с графическим в том, что он менее трудоёмок, так как позволяет определять скорости и ускорения (их величину и направление) на одном плане скоростей или плане ускорений для множества точек механизма.
Недостатком метода является то, что требуется построить планы скоростей и ускорений для нескольких положений механизма (если необходимо определять скорость и ускорение при различных положениях механизма и его звеньев).
План скоростей механизма – совокупность планов скоростей отдельных звеньев, построенных из одной общей точки , называемой полюсом плана скоростей.
Пример
Дано: , и (рис. 9.26).
Требуется определить: .
Зададимся неким масштабным коэффициентом .
Рис. 9.26
Решение:
Для построения плана скоростей механизма существуют различные методы, наиболее распространённым из которых является метод векторных уравнений, разработанный советскими учёными.
Модуль скорости точки можно определить по следующей формуле: . Линия действия вектора скорости точки перпендикулярна звену , а сам вектор направлен в сторону вращения звена .
Допустим, что точка не закреплена, и представим себе, что все точки звена совершают переносное движение со скоростью , то есть . С одной стороны , с другой стороны .
Вернём точку на действительную траекторию , для чего придадим точке скорость относительного вращательного движения около точки со скоростью относительного движения .
На плане скоростей векторы, исходящие из полюса скоростей являются векторами абсолютных скоростей соответствующих точек, а векторы, которые не проходят через полюс плана ускорений, являются относительных скоростей соответствующих точек. Отрезок является планом скоростей звена , а отрезок является планом скоростей звена .
Определение ускорений графоаналитическим методом.
Рассуждая аналогично теореме подобия для определения скоростей отдельных точек звеньев, очевидно, что план ускорений жёсткого звена подобен самому звену, и повёрнут на девяносто градусов.
Полное ускорение можно найти геометрически просуммировав нормальное и тангенциальное ускорения, то есть: (рис. 9.27).
Рис. 9.27
Модуль вектора нормального ускорения точки можно найти по формуле: . Линия действия этого вектора будет перпендикулярна звену .
Модуль вектора тангенциального ускорения точки можно найти по формуле: . Линия действия этого вектора будет параллельна звену .
План ускорений механизма, как и план скоростей, не подобен самому механизму, и является совокупностью планов ускорений отдельных звеньев, построенных из одного полюса плана ускорений .
Пример
Планы скоростей и ускорений кривошипно-ползунного механизма
Последовательность построения планов скоростей и ускорений кривошипно-ползунного механизма (рис. 9.25) аналогична той, которая приведена в предыдущем случае. В дальнейшем некоторые подробности (расчёты масштабов, длин , масштабов планов скоростей и ускорений и т.д.) будут пропущены.
План скоростей кривошипно-ползунного механизма начинают строить после построения плана механизма в заданном положении, в выбранном масштабе длин , составления векторного уравнения скоростей и выбора масштаба плана скоростей .
Векторное уравнение скоростей шатуна 2 (рис. 9.28)
где – скорость точки А, м/с; вектор этой скорости направлен перпендикулярно прямой ОА кривошипа 1 (рис. 9.28) на плане механизма; VВА – вектор скорости точки В относительно А; имеет направление, перпендикулярное прямой АВ на плане механизма; VВ – вектор полной (абсолютной), скорости ползуна 3; должен быть параллельным направлению движения ползуна.
Для построения плана скоростей сначала из полюса плана Рv (рис. 9.28) проводится вектор скорости точки А относительно О – VА, т.е. векторный отрезок Рva. Затем через точку а проводится перпендикуляр к прямой АВ плана механизма и через полюс Рv – прямая, параллельная движению ползуна 3. На пересечении этих двух прямых получается точка b. Направления векторов скоростей VВ и VВА обозначают стрелками.
Например, необходимо определить скорость точки S2, принадлежащей шатуну 2 и расположенной на середине отрезка АВ. Используя теорему подобия, на отрезке ab плана скоростей находят его середину (точка S2), которая, будучи соединенной с полюсом Рv, даст вектор VS2, изображающий абсолютную (полную) скорость точки S2.
Рис. 9.28. Построение планов скоростей и ускорений
кривошипно-ползунного механизма
Рассчитаем величину линейных скоростей и угловую скорость шатуна:
, м/с,
, м/с,
, м/с,
, с-1.
Направление вектора угловой скорости шатуна определяется следующим образом. Вектор скорости VВА условно переносится в точку В плана механизма. Куда он будет вращать шатун относительно точки А, в ту сторону и направлена угловая скорость шатуна.
План ускорений кривошипно-ползунного механизма строят после того, как будет составлено векторное уравнение ускорений шатуна, учитывая, что он совершает сложное движение:
где аА – ускорение точки А; его величину и направление можно определить, используя векторное уравнение ускорения точки А относительно оси О вращения кривошипа:
причём ускорение точки А относительно О можно разложить на две составляющие – нормальное ускорение и тангенциальное , т.е.
Так как точка О неподвижна и ускорение её равно нулю ( и при условии, что угловая скорость вращения кривошипа постоянна: и его угловое ускорение ), то векторное уравнение ускорения точки А можно записать в виде
Величина нормальной составляющей ускорения (нормальное ускорение) рассчитывается по формуле
(его вектор направлен по радиусу вращения кривошипа от точки А к точке О).
Затем вычисляется нормальное ускорение точки В относительно А по формуле
(его вектор направлен от В к А).
После выбора масштаба плана ускорений по формуле
величина нормального ускорения переводится этим масштабом в векторный отрезок длиной
, мм.
Затем строится план ускорений (см. рис. 9.28). Из произвольно выбранного полюса Ра параллельно отрезку ОА плана механизма проводится вектор ускорения , длина которого была выбрана произвольно при расчёте масштаба . Из конца этого вектора (точки ) проводится вектор ускорения длиной , который должен быть параллелен отрезку АВ плана механизма и направлен от точки В к А. Перпендикулярно ему через точку n2 проводят прямую до пересечения с прямой, проведённой через полюс Ра параллельно линии движения ползуна 3. Полученная точка их пересечения b' определяет длины векторов ускорений aBA и aB.
Для нахождения величины ускорения точки S2, принадлежащей шатуну, можно применить теорему подобия. При этом необходимо на векторе, изображающем на плане ускорений относительное ускорение aBA, найти соответствующую точку S2', делящую отрезок a'b' в той же пропорции, что и точка S2 делит отрезок АВ на плане механизма.
Угловое ускорение шатуна вычисляется по формуле
, с-1,
где n2b' – длина вектора на плане ускорений, изображающего тангенциальное ускорение .
Для определения направления вектора углового ускорения шатуна необходимо вектор тангенциального ускорения условно перенести в точку В плана механизма. Куда он будет вращать шатун относительно точки А, в ту сторону и направлено ускорение шатуна.
Аналитический метод кинематического анализа
Общие сведения о методе
Графический (метод диаграмм) и графоаналитический методы (метод планов скоростей и ускорений) кинематического анализа механизмов имеют недостатки: невысокая точность, определяемая точностью графических построений, и большая трудоёмкость.
Эти недостатки отсутствуют в аналитическом методе. Но при этом необходимо составлять достаточно сложные аналитические зависимости (формулы) и иметь возможность решать их с использованием компьютерных техники и технологии, что в последнее время возможно и доступно.
Методы аналитического исследования:
метод замкнутых векторных контуров (метод Зиновьева) удобен для кинематического анализа практически всех используемых в технике несложных рычажных механизмов;
метод преобразования координат (метод Морошкина) удобен для кинематического анализа многозвенных механизмов типа манипуляторов промышленных роботов.
Прежде чем говорить об аналитическом методе, введем некоторые понятия и определения.
Функция положения. Аналог скорости. Аналог ускорения
Положение любого звена механизма может определяться параметрами: углом относительно какой-либо координатной оси или координатами ХК и YК (рис. 9.29).
Рис. 9.29. Схема механизма
Функция положения – это аналитическая зависимость положения или координаты К-го звена ( , ХК или YК ) от положения ведущего звена , т.е. или и , где , XK и YK – координаты, определяющие положение К-го звена (ведомого), а угол – угол, характеризующий положение ведущего звена.
Аналог скорости. Угловая скорость К-го звена определяется зависимостью
, (3)
где – аналог скорости К-го звена (первая передаточная функция) для вращающегося звена, величина безразмерная; и – аналоги скорости К-го звена, движущегося поступательно, величины безразмерные.
Аналог ускорения. Угловая скорость К-го звена определяется зависимостью, получаемой дифференцированием уравнения (3) по dt:
.
Введение в кинематический анализ понятий аналогов отделяет геометрические свойства механизма от кинематических.
Величину называют ещё передаточным отношением, так как выражение можно преобразовать, умножив и разделив его на величину dt:
Для решения задачи о положениях звеньев исследуемого механизма необходимо найти функции положения ( или ХК и YК ), предварительно составив векторное уравнение замкнутого векторного контура кинематической цепи и уравнения проекций его на координатные оси Х и Y. Из этих уравнений находят функции положения (зависимости положений исследуемого звена от положения ведущего звена). При известном (заданном) законе движения ведущего звена задаются шагом и вычисляют координаты исследуемых звеньев (угловые координаты для вращающегося звена и прямоугольные для звена, совершающего возвратно-поступательное движение).
Для решения задачи о скоростях необходимо найти аналоги скоростей исследуемых звеньев и, умножив их на угловую скорость ведущего звена, получить формулы расчета искомых скоростей.
Для решения задачи об ускорениях находят также аналоги ускорений звеньев и по формулам, приведенным в таблице, находят величины ускорений. Ниже приводится пример кинематического анализа кривошипно-ползунного механизма аналитическим методом.
9.5. Силовой (кинетостатический) анализ механизмов.
Проектирование нового механизма всегда включает его силовое исследование, так как по найденным силам производится последующий расчет на прочность элементов кинематических пар и звеньев механизма.
Силы, действующие в механизмах
Различают две группы внешних сил.
Движущие силы Рдв или моменты движущих сил Мдв, которые:
- совершают положительную работу;
- направлены в сторону скорости точки приложения силы или под острым углом к ней;
- задаются посредством механической характеристики двигателя.
Пример: силы давления газа на поршень в двигателе внутреннего сгорания, силы веса при опускании груза и т.д.
Силы сопротивления РС и их моменты МС, которые:
- совершают отрицательную работу;
- направлены противоположно скорости.
В свою очередь силы сопротивления делятся на силы:
- полезного сопротивления Рп.с и моменты Мп.с (силы тяжести при подъеме груза);
- вредного сопротивления: трение в кинематических парах, сопротивление среды, внутреннее сопротивление (например, силы упругости звеньев).
Кроме этого существуют:
- силы веса (тяжести) , где – масса звена в кг; м/с2 – ускорение свободного падения. При кинематическом исследовании считают, что сила тяжести приложена в центре тяжести звена. Если звено выполнено в виде стержня, то его ц.т. расположен в центре симметрии звена, а если в виде ползуна, то в центре шарнира. Силы тяжести в течении расчётного цикла могут быть как движущими, так и силами полезного сопротивления, поэтому работа этих сил за цикл равна нулю. Эти силы считаются внешними силами.
- силы инерции ;
- моменты сил инерции , где m, JS – масса и массовый момент инерции звена; и – линейное и угловое ускорения;
- силы реакций в кинематических парах , возникающие в опорах звеньев и являющиеся внутренними силами для механизма в целом и внешними для каждого отдельного звена.
Необходимо отметить, что под силами понимаются равнодействующие соответствующих распределенных в месте контакта кинематической пары нагрузок. Все вышесказанное относительно сил распространяется и на моменты сил.
Силы инерции звеньев и моменты сил инерции.
Так как звенья механизма находятся в движении, и имеют свои массы, то, особенно в быстродействующих механизмах рычажного типа, обязательно имеет место неравномерность движения звеньев. Это означает, что ускорения этих звеньев не равны нулю, что приводит к возникновению дополнительных сил динамического характера в виде сил инерции и моментов инерции . Из теоретической механики известно, что все силы инерции звена, совершающего плоскопараллельное движение и имеющего плоскость симметрии, параллельную плоскости движения, могут быть сведены к силе инерции , приложенной в центре масс S звена, и паре сил инерции, момент которых обозначим (рис. 9.30).
Рис. 9.30. Сила инерции звена и момента сил инерции
– главный вектор сил инерции, или сила инерции;
– главный момент сил инерции, или момент сил инерции; m – масса звена;
– массовый момент инерции относительно центра масс;
– ускорение центра масс;
– угловое ускорение звена.
и направлены в стороны, противоположные ускорениям и .
Статическая определимость кинематической цепи
При силовом анализе механизмов (определении неизвестных сил, действующих на движущиеся звенья) можно использовать уравнения (законы) статики. Докажем это положение, проанализировав реакции в кинематических парах (табл. 9.2).
Таблица 9.2.
Кинематические пары |
Равновесие каждого звена |
Известные параметры |
Неизвестные параметры |
5-й класс Вращательная |
|
Точка приложения |
Величина, направление |
Поступательная |
|
Направление |
Величина, точка приложения |
4-й класс
|
|
Точка приложения, направление |
Величина |
Примечание. 2, 3, 5 – номера звеньев.
В кинематических парах 5-го класса известно по одному параметру сил реакций, неизвестны два, в кинематических парах 4-го класса известны два параметра, а неизвестен один.
Таким образом, плоская кинематическая цепь, состоящая из кинематических пар 5-го и 4-го классов, имеет 2Р5 + Р4 неизвестных величин сил реакций.
В то же время для одного звена можно составить 3 уравнения статики, а для n звеньев – 3n уравнений статики.
Кинематическая цепь будет статически определима, если число неизвестных величин сил реакций не превышает числа возможных уравнений статики, т.е.
3n = 2P5 + Р4.
Это и есть условие статической определимости кинематической цепи.
Полученное равенство можно записать в виде
3n – 2Р5 – Р4 = 0.
Но запись слева от знака равенства является числом степеней свободы кинематической цепи W, т.е.
W = 3n – 2Р5 – P4 = 0.
Таким свойством (W=0) обладают структурные группы, или группы Ассура – статически определимые кинематические цепи.
Силовой анализ механизма с учетом сил трения
9.6. Трение в механизмах. Виды трения.
Способность контактирующих поверхностей звеньев сопротивляться их относительному движению называется внешним трением. Трение обусловлено неидеальным состоянием контактирующих поверхностей (микронеровности, загрязнения, окисные пленки и т.п.) и силами межмолекулярного сцепления. Трение в кинематических парах характеризуется силами трения и моментами сил трения. Силой трения называется касательная составляющая реакции в кинематической паре (составляющая направленная по касательной к контактирующим поверхностям), которая всегда направлена против вектора скорости относительного движения звеньев.
Различают следующие виды трения:
- трение покоя проявляется в момент, когда два тела находящиеся в состоянии относительного покоя начинают относительное движение (касательную составляющую возникающую в зоне контакта до возникновения относительного движения, в условиях когда она меньше силы трения покоя, будем называть силой сцепления; максимальная величина силы сцепления равна силе трения покоя);
- трение скольжения появляется в кинематической паре при наличии относительного движения звеньев; для большинства материалов трение скольжения меньше трения покоя;
- трение качения появляется в высших кинематической паре при наличии относительного вращательного движения звеньев вокруг оси или точки контакта;
- трение верчения возникает при взаимодействии торцевых поверхностей звеньев вращательных кинематической паре (подпятники).
Сила трения покоя зависит от состояния контактных поверхностей звеньев, а сила трения скольжения - также и от скорости скольжения.
Теоретические основы определения коэффициента трения
Трение в поступательной кинематической паре
При перемещении одного тела (звена механизма) относительно находящегося с ним в контакте другого тела (звена) в месте их контакта возникает сила, сопротивляющаяся перемещению, – сила трения F (рис. 9.31).
Величину коэффициента трения в поступательной кинематической паре можно определить с помощью так называемого закона Кулона, в соответствии с которым величина силы трения F прямо пропорциональна нормальной силе N между соприкасающимися звеньями. Векторная сумма сил и равна полной силе реакций в кинематической паре: (рис. 30).
Рис. 9.31. Схема сил в поступательной кинематической паре
Отношение называют коэффициентом трения скольжения в поступательной кинематической паре, а угол – углом трения скольжения.
Полная реакция отклоняется на угол трения в сторону, противоположную скорости (см. рис. 4.16).
Величину коэффициента трения скольжения f можно определить экспериментально или по справочникам (величина f зависит от шероховатости, материалов, трущихся поверхностей, наличия смазки, ее качества, температуры и т.д.).
Трение во вращательной кинематической паре
Внешние нагрузки, действующие на вал при его вращении, показаны на схеме рис. 9.32.
Рис. 9.32. Схема сил во вращательной кинематической паре
Здесь А – точка приложения нормальной реакции , причем – равнодействующая всех нормальных сил (эпюра этих сил может иметь различный вид), (рис. 32); – сила трения (равно-действующая всех сил трения, распределенных по поверхности контакта); – сила давления цапфы вала на опору (корпус подшипника); – сила реакции во вращательной кинематической паре, ; ; – угол трения; r – радиус цапфы (опорной части) вала; – радиус круга трения; – приведенный коэффициент трения.
Во вращательной кинематической паре реакция отстоит от оси вращения на величину радиуса круга трения , причем всегда касательна к кругу трения.
Момент трения .
Величину можно определить:
– экспериментально (например, используя метод выбега);
– по эмпирическим формулам с учетом износа подшипника и соответствующего изменения эпюр давления (рис. 32): для нового подшипника , для изношенного – , где f – коэффициент трения скольжения в поступательной кинематической паре (берется из справочников).
а) б)
Рис. 9.33. Примерные схемы эпюр давления в новом
(а) и изношенном (б) подшипниках скольжения
Трение качения в высшей кинематической паре
Картину внешних сил и эпюр распределения давлений в месте контакта тел качения можно условно отобразить на нижеприведенных схемах (рис. 9.34). В состоянии покоя эпюра напряжений в зоне контакта симметрична относительно общей нормали, проведенной через условную точку касания, а равнодействующая сила N совпадает с нормалью. При качении симметрия эпюры нарушается, а сила N смещается в направлении качения на расстояние k.
а) б)
Рис. 9.34. Примерные схемы сил и эпюр давления в зоне контакта цилиндра
с плоскостью: а) состояние покоя; б) состояние перекатывания
Здесь – равнодействующая сила давлений в месте смятия соприкасающихся звеньев (тел качения); – нагружающая сила, ; – момент трения качения; – плечо силы трения качения или коэффициент трения качения (имеет размерность длины); – сила перекатывания.
Условие равновесия перекатывающегося тела в форме моментов можно записать как , откуда .
9.7. Динамика машин и механизмов.
Общие положения
Динамика - раздел механики машин и механизмов, изучающий закономерности движения звеньев механизма под действием приложенных к ним сил. Имеется такое определение: “Динамика рассматривает силы в качестве причины движения тел”. В основе динамики лежат три закона, сформулированные Ньютоном, из которых следует:
Из первого закона: Если равнодействующая всех внешних сил, действующих на механическую систему равно нулю, то система находится в состоянии покоя.
Из второго закона: Изменение состояния движения механической системы может быть вызвано либо изменением действующих на нее внешних сил, либо изменением ее массы.
Из этих же законов следует, что динамическими параметрами механической системы являются:
- инерциальные (массы m и моменты инерции I);
- силовые (силы Fij и моменты сил Mij);
- кинематические (линейные a и угловые ускорения).
Динамическая модель - модель системы, предназначенная для исследования ее свойств в функции времени (или модель системы, предназначенная для исследования в ней динамических явлений).
Прямая задача динамики - определение закона движения системы при заданном управляющем силовом воздействии.
Обратная задача динамики - определение требуемого управляющего силового воздействия, обеспечивающего заданный закон движения системы.
Методы составления уравнений (динамической модели системы):
- энергетический (уравнения энергетического равновесия - закон сохранения энергия);
- кинетостатический (уравнения силового равновесия с учетом сил инерции по принципу Д’Аламбера).
Задачами динамического анализа и синтеза механизма, машины являются изучение режимов движения с учетом действия внешних сил и установление способов, обеспечивающих заданные режимы движения. При этом могут определяться мощности, необходимые для обеспечения заданного режима движения машины, проводиться сравнительная оценка механизмов с учетом их механического коэффициента полезного действия, устанавливаться законы движения ведущего звена (например, колебания угловой скорости кривошипа за один оборот) под действием внешних сил, приложенных к звеньям механизма, а также решаться задачи подбора оптимальных соотношений между силами, массами, размерами звеньев механизмов.
В динамике машин объектом изучения (исследования) является машинный агрегат. В общем виде его можно представить как механическую систему, состоящую из трех основных частей: машина-двигатель, передаточный механизм и рабочая машина (или исполнительный механизм).
В машине-двигателе какой-либо вид энергии преобразуется в механическую энергию, необходимую для приведения в движение рабочей машины. Например, в электродвигателе электрическая энергия преобразуется в механическую, а в двигателе внутреннего сгорания в механическую энергию преобразуется тепловая энергия сгорания топлива.
Передаточный механизм служит для преобразования движения, изменения характера движения, скорости, направления движения и т.д.
Рабочая машина предназначена для выполнения работы, связанной с трудовой деятельностью человека или выполнением технологического процесса.
Работа – физическая величина, характеризующая преобразование энергии из одной формы в другую.
Элементарная работа силы выражается формулой
где Р – сила; dS – элементарная величина перемещения точки приложения силы; – угол между векторами силы и скорости.
Элементарная работа момента силы выражается формулой
,
где М – момент силы; – элементарный угол поворота.
Размерность работы измеряется в джоулях: Дж = Нм.
Полная работа выражается формулами
, или .
Мощность – это энергетическая характеристика, равная отношению работы к интервалу времени ее совершения, выражается формулами
,
где V – скорость точки приложения силы Р,
или ,
где – угловая скорость звена, к которому приложен момент.
Размерность мощности измеряется в ваттах: Вт = Дж/c; 1000 Вт =1 кВт (киловатт), 1 кВт = 1, 36 л.с.
Кинетическая энергия, приведенная масса, приведенный момент инерции механизма
Анализ движения машинного агрегата, находящегося под действием приложенных к нему внешних сил, удобно проводить с использованием метода приведения масс и сил к какому-либо звену механизма. Он сводится к анализу динамики тела (звена приведения), к которому приведены все внешние силы и моменты. Чаще всего звеном приведения выступает ведущее звено механизма.
Задача динамического анализа – определение истинного закона движения ведущего звена механизма, находящегося под действием заданных внешних сил и моментов, действующих в машинном агрегате.
Кинетическая энергия механизма
Для i-го звена, совершающего сложное движение (например, для шатуна кривошипно-ползунного механизма), кинетическую энергию можно выразить формулой
,
где первое слагаемое правой части – это кинетическая энергия поступательного движения центра масс звена; второе слагаемое – кинетическая энергия вращательного движения; mi – масса звена; Vsi – скорость центра масс; Jsi – момент инерции звена относительно центра масс; – угловая скорость звена.
Для всего механизма кинетическая энергия равна сумме кинетических энергий всех звеньев механизма:
(1)
где n – количество подвижных звеньев.
Приведенная масса механизма
Условно заменим механизм его динамической моделью. Например, кривошипно-ползунный механизм (рис. 9.35) заменим динамической моделью, состоящей из стойки и кривошипа.
Рис. 9.35. Замена кривошипно-ползунного механизма динамической моделью
Здесь ОА – звено приведения механизма, в котором как бы сосредоточена инертность всех звеньев механизма, А – точка приведения.
Уравнение (1) умножим и разделим на квадрат скорости точки приведения VA:
Выражение в квадратных скобках имеет размерность массы (кг) и называется приведенной массой mпр механизма в точке А.
Тогда
где
. (2)
Приведенной массой механизма называется такая условная масса, которая как бы сосредоточена в точке приведения механизма, кинетическая энергия которой равна сумме кинетических энергий всех звеньев механизма.
Приведенным моментом инерции механизма называется такой условный момент инерции, которым как бы обладает звено приведения относительно оси вращения, кинетическая энергия которого (при таком моменте инерции) равна сумме кинетических энергий всех звеньев механизма.
Величины mпр и Jпр не являются постоянными для данного механизма, а меняют свое численное значение в зависимости от положений звеньев, так как звенья меняют свои скорости.
Пример 1.
Определить приведенную массу и приведенный момент инерции для заданного положения кривошипно-ползунного механизма (рис. 35), если известны положения центров масс звеньев (S1 и S2), линейные и угловые скорости звеньев и центров масс звеньев: , и – скорости центров масс кривошипа, шатуна и ползуна, и – угловые скорости кривошипа и шатуна.
Рис. 9.36. Кривошипно-ползунный механизм
Пусть кривошип 1 – звено приведения, А – точка приведения.
Приведенная масса механизма согласно (4.2) вычисляется по формуле
,
а приведенный момент инерции согласно (3) – по формуле
.
Уравнение движения машины в форме кинетической энергии
Рассмотрим состояние механизма при двух различных положениях ведущего звена, разделяемых каким-либо промежутком времени или углом поворота ведущего звена – кривошипа (рис. 9.37).
Рис. 9.37. Кинематические и динамические параметры механизма
при различных положениях звена приведения
При положении кривошипа угловая скорость звена приведения – , Iпр.0 – приведенный момент инерции механизма в рассматриваемом положении.
При положении угловая скорость звена приведения – , Iпр.1 – приведенный момент инерции механизма.
Изменение кинетической энергии механизма за этот промежуток времени будет равно разности работ сил движущих Адв и сил сопротивления Асопр, выполненных за это время (или избыточной работе ):
. (4)
(5)
где Е0 и Е1 – величины кинетических энергий механизма при положениях и кривошипа.
(6)
(7)
где Мдв и Мсопр – приведенные моменты сил движущих и сил сопротивлений.
Подставив (5-7) в (4), получим
. (8)
Из (8) выразим угловую скорость кривошипа при положении :
(9)
Уравнение (9) называют уравнением движения машины в форме кинетической энергии.
Режимы движения машины
В общем виде движения машины можно разделить на три основных режима (периода): разгон, установившееся движение и останов (рис. 9.38).
Рис 9.38. Схема режимов движения машины
В режиме разгона угловая скорость в начале режима , в конце – , что следует из уравнения (9). При этом всегда , иначе разгон невозможен.
В режиме установившегося движения , изменение кинетической энергии (в среднем за один оборот ведущего вала) . В пределах одного оборота происходят периодические колебания угловой скорости вала машины.
В режиме останова (когда двигатель отключен) . При этом выполняется работа, затрачиваемая на преодоление сил трения:
9.8. Механический кпд механизма
В период установившегося движения машины соблюдается условие равенства работ сил движущих и сил сопротивлений:
.
Работа сил сопротивления складывается из суммы работ сил полезного сопротивления и сил вредного сопротивления . Тогда
.
Разделим левую и правую части равенства на величину работы сил движущих:
и получим
где – механический (цикловой) коэффициент полезного действия (кпд); – коэффициент механических потерь.
Определение кпд машинного агрегата при последовательном соединении входящих в него механизмов
Рассмотрим машинный агрегат, состоящий из последовательно соединенных механизмов, условно обозначенных на схеме (рис. 9.39) цифрами 1, 2 и 3.
А А1 А2 А3
Рис. 9.39. Машинный агрегат с последовательно соединенными механизмами
Пусть к механизму 1 подводится работа величиной А. На выходе получаем работу величиной А1, которая подводится к механизму 2 и т.д. Величина работы на выходе всегда меньше, чем подведенная работа на входе (А1<A, A2<A1, A3<A2), так как в каждом механизме имеются механические потери подведенной к нему работы.
Тогда общий кпд машинного агрегата
а кпд каждого механизма
, , .
Перемножим кпд всех последовательно соединенных механизмов:
Вывод: общий механический кпд машинного агрегата, состоящего из последовательно соединенных n механизмов, равен произведению их кпд:
Определение кпд машинного агрегата при параллельном соединении входящих в него механизмов
Рассмотрим машинный агрегат, состоящий из трех параллельно соединенных механизмов, условно обозначенных на схеме (рис. 9.40) цифрами 1, 2, 3. Пусть к механизмам подводится работа величиной А, которая распределяется на каждый механизм в разных долях, определяемых коэффициентами , , , каждый из которых меньше 1, а их сумма .
Рис. 9.40. Машинный агрегат с параллельно соединенными механизмами
Общий кпд всего машинного агрегата можно выразить отношением суммы работ на выходе механизмов к общей подведенной работе А:
. (12)
Так как
, ;
, ;
, ,
то, подставив эти выражения в (12), получаем
.
Отсюда следует, что общий механический кпд машинного агрегата при параллельном соединении механизмов равен сумме величин кпд каждого механизма, умноженных на коэффициенты долей работ, подводимых к механизмам:
.
Сравним варианты последовательного и параллельного соединения механизмов с точки зрения минимизации механических потерь в машинном агрегате.
Пусть величины кпд каждого механизма равны . При этом коэффициенты, учитывающие доли распределения общей работы А между всеми механизмами, также равны:
.
Тогда
, .
Так как , то . Отсюда следует, что параллельное соединение механизмов в машинном агрегате предпочтительнее с точки зрения уменьшения механических потерь.
Самоторможение
Если , то действительного движения механизма произойти не может. Это называется явлением самоторможения. Следовательно, если при теоретических расчетах получим , то механизм в заданном направлении двигаться не может.
Для возможности движения механизма необходимо обеспечить условие
.
Неравномерность хода ведущего звена машины
Уравнение движения главного вала машины в форме кинетической энергии имеет вид
.
Так как величина избыточной работы , являясь функцией угла поворота вала , угловой скорости и времени t, есть величина переменная, т.е. , при этом , то при установившемся режиме работы машины угловые скорости в начале и конце одного цикла Т (например, одного оборота) равны: (рис. 40).
За цикл изменение кинетической энергии равно нулю . Внутри цикла угловая скорость вала может меняться, что вызывает дополнительные динамические (инерционные) нагрузки, а также дополнительное трение в кинематических парах, снижающее надежность механизма и его кпд.
Ухудшаются условия работы механизма, приходится увеличивать материалоемкость машины, повышать прочность звеньев, нести дополнительные энергетические затраты на преодоление трения.
Рис. 9.41. Периодические колебания угловой скорости главного вала машины в период установившегося движения
Коэффициент неравномерности хода ведущего вала машины выразим формулой
, (13)
где
. (14)
Из (13) и (14) получим
Величина может находиться в следующих пределах: для ударных машин и прессов , для металлорежущих станков , для двигателей .
9.9. Регулирование периодических колебаний угловой скорости с помощью маховика
В случае необеспечения требуемой величины при работе машины могут возникнуть нежелательные явления и процессы (вибрация, повышенные энергетические затраты, невозможность выполнения технологического процесса и т.д.). При условии периодических колебаний угловой скорости вала для получения заданной величины используют маховик – массивное колесо с большим моментом инерции.
Основная задача при расчете маховика – это определение его момента инерции. Маховик с таким моментом инерции в интервале скоростей от до (см. рис. 5.5) должен произвести работу, равную изменению кинетической энергии механизма за это время:
.
Расчет величины момента инерции маховика
Приведенный момент инерции механизма можно представить в виде
при ,
при ,
где – постоянная составляющая приведенного момента инерции механизма; – момент инерции маховика или маховых масс (колес, валов и т.д.), (величина постоянная для данного механизма); – составляющая приведенного момента инерции при максимальной скорости в цикле ; – составляющая приведенного момента инерции при минимальной скорости в цикле .
Тогда
. (15)
Из (15) следует (если ,
.
С учетом (13) и (14) получим
. (16)
Для определения величины задаются величинами и . Формулу (16) можно упростить, если принять . Тогда
.
При больших маховых массах (когда ) можно приближенно принять
.
Для определения величины можно пользоваться диаграммами моментов сил движущих и сил сопротивлений (рис. 9.42).
Рис. 9.42. Моменты сил движущих и сил сопротивлений в цикле Т
Площади f1…f4, ограниченные кривой Мсопр и графиком Мдв, представляют собой разности работ движущих моментов Мдв и моментов сопротивлений Мсопр. Суммы площадей имеют соотношение
Выбирают наибольшую из заштрихованных площадей. Если , то величину максимальной избыточной работы можно определить по формуле
,
где и – масштабы графиков по осям и М.
Регулирование непериодических колебаний скорости движения машин
В процессе выполнения работы приходится регулировать скорость рабочего органа машины. Например, в стационарных двигателях необходимо поддерживать скорость рабочего органа постоянной, а в двигателях транспортных машин эта скорость должна изменяться в широких пределах.
Из уравнения движения машины следует, что изменения скорости рабочего органа можно достигнуть за счет изменения разности работ движущих сил и сил сопротивления ( ).
Устройства, обеспечивающие изменения работы сил сопротивления применяются в виде тормозов, например, в транспортных машинах, которые снабжаются также и приспособлениями для одновременного разобщения двигателя с машиной – орудием.
Другим способом регулирования является изменение работы движущих сил путем воздействия на орган, подающий энергию к входному звену (поршню у двигателя внутреннего сгорания, лопаткам турбины и т.д.).
Регулирование может осуществляться либо человеком-оператором, либо автоматически – с помощью устройств, называемых регуляторами.
Рис. 9.43
Одним из них является центробежный регулятор (рис.42), приводимый во вращение валом двигателя В. Ползун А соединяется с органом, подводящим рабочее тело (пар, горючая смесь и т.д.). Регулятор автоматически поддерживает скорость вала двигателя постоянной, т.к. ее увеличение приводит к уменьшению подачи рабочего тела и наоборот.
ВОПРОСЫ ДЛЯ САМОПРОВЕРКИ
- Что является целью курса ТММ, какие задачи решаются в курсе ТММ?
- Какие основные разделы содержит курс ТММ?
- Что называется "проектом" и "инженерным проектированием"?
- Перечислите основные этапы процесса проектирования?
- Дайте определения понятий "техническая система" и "структура"?
- Что называется "машиной", какие виды машин Вы знаете?
- Дайте определения понятий "звено" и "кинематическая пара"?
- Какая техническая система называется механизмом?
- Почему вращательное движение наиболее распространено в механизмах и машинах?
- Какие функции могут выполнять механические передачи?
- Какие механизмы называют рычажными?
- Какие звенья всегда входят в состав шарнирных механизмов?
- Чем кривошип отличается от коромысла?
- В чем особенность зубчатой передачи и кулачкового механизма?
- Что такое кулачок?
- Что такое передаточное число?
- Как определяют передаточное число и КПД многоступенчатой передачи?
- Как изменяются от ведущего к ведомому валу такие характеристики передачи как мощность, вращающий момент, частота вращения?
- В какой форме может быть представлена структурная модель механизма?
- Какова цель структурного анализа?
- Что понимают под логическими приемами анализа и синтеза?
- Что называют звеном механизма?
- Что называют кинематической парой?
- Как классифицируются плоские кинематические пары?
- Что называется кинематической цепью?
- Как рассчитать подвижность плоского механизма?
- Какой физический смысл имеет подвижность механизма?
- Что собой представляет избыточная связь?
- Перечислите признаки по которым классифицируются кинематические пары?
- Что называют структурным анализом и структурным синтезом?
- Каким образом при выборе структурной схемы механизма учитываются ее функциональные возможности?
- Какие избыточные связи полезны для работы механизма?
- Чем кинематическая пара отличается от других подвижных соединений двух звеньев?
- Какими преимуществами и недостатками обладают низшие пары по сравнению с высшими?
- Напишите формулы для подсчета подвижности механизма для плоскости и для пространства?
- Как из кинематической цепи получить механизм?
- Чему равно минимальное число звеньев и кинематических пар в кинематической цепи?
- Что называется "функцией положения" для звена или точки механизма?
- В чем различие между кинематическими и геометрическими характеристиками механизма?
- Какие функции называются кинематическими передаточными функциями механизма?
- Какие передаточные функции механизма называются главными, а какие вспомогательными?
- Перечислите методы геометро-кинематического исследования механизмов?
- Что называется "центроидой", как центроиды используются при кинематическом исследовании механизма?
- Как метод кинематических диаграмм применяется при кинематическом исследовании механизмов?
- Как применяется метод преобразования координат при решении прямой задачи о положении точки выходного звена?
- Опишите последовательность кинематического анализа плоского механизма.
- По какому признаку можно установить, является ли равномерным (или неравномерным) относительное движение звеньев, образующих поступательную пару?
- Дайте классификацию сил, действующих в кинематических парах механизмов?
- Перечислите виды силового расчета механизмов?
- Как определить число неизвестных в силовом расчете?
- Назовите цели и методы силового анализа механизма.
- Сформулируйте условие статической определимости плоского механизма.
- Что изучается в разделе курса динамика машин и механизмов?
- Как формулируются прямая и обратная задачи динамики машин?
- Что называется "энергией", "работой" и "мощностью"?
- Как идеальные механизмы преобразуют энергию?
- Что называют коэффициентом полезного действия механической системы ?
- Как определяется КПД механической системы при последовательном и параллельном соединении элементов ?
- Какой режим движения машины называется установившимся ?
- Что называется "коэффициентом неравномерности" и какие величины этого коэффициента установлены для различных машин?
- Какими методами регулируется величина "коэффициента неравномерности" ?
- Как влияет момент инерции маховика на коэффициент неравномерности ?
- Как по коэффициенту неравномерности определяется необходимая маховая масса первой группы звеньев ?
- Изложите алгоритм решения задачи регулирования хода машины по методу Н.И. Мерцалова ?
- По каким зависимостям рассчитываются первые передаточные функции кривошипно-ползунного механизма ?
- Как определяются параметра динамической модели для двигателя внутреннего сгорания ?
- Как строится диаграмма кинетической энергии второй группы звеньев ?
- Как строится диаграмма угловой скорости звена приведения ?
- Как учитывается статическая характеристика асинхронного электродвигателя при анализе динамических процессов ?
БИБЛИОГРАФИЧЕСКИЙ СПИСОК
1. Александров А.В. и др. Сопротивление материалов: Учебник для ст-тов вузов – 2-е изд., испр. – М.: Высшая школа, 2008. – 559 с.
2. Бояршинов, С.В. Основы строительной механики машин – М. : Машиностроение, 2006. – 456 с.
3. Гафаров Р.Х. Что нужно знать о сопротивлении материалов: Учебное пособие для вузов обуч. по направлениям подгот. и спец. в области техники и технологии – М.: Машиностроение, 2007. – 275 с.
4. Дарков, А.В. Сопротивление материалов. – М. : Высшая школа, 2007. – 623 с
5. Миролюбов И.Н. и др. Пособие по решению задач по сопротивлению материалов: учебное пособие для технических вузов. – М.: Высшая школа, 2007. – 399 с
6. Степин П.А. Сопротивление материалов. – М. : Высшая школа, 2008. – 303 с.
7. Феодосьев В.И. Сопротивление материалов: Учебник для студ-ов высш. техн. учеб.зав. – 10-е изд., перераб. и доп. – М.: Изд-во МГТУ им. Н.Э. Баумана, 2008. – 588 с.
- Управляющий: Иванов Николай Юрьевич
Курс дисциплины позволяет сформировать базовые знания, которые обеспечат эффективную практическую отработку на базе учебно-тренажёрного центра по следующим разделам:
- выживание в море в случае оставления судна;
- сведение к минимуму риска пожара и поддержание состояния готовности к действиям в аварийных ситуациях, связанных с пожаром;
- борьба с огнём и тушение пожара;
- принятие немедленных мер при несчастном случае или в иной ситуации, требующей неотложной медицинской помощи;
- соблюдение порядка действий при авариях;
- принятие мер предосторожности для предотвращения загрязнения морской среды;
- соблюдение техники безопасности;
- содействие установлению эффективного общения на судне;
- содействие установлению хороших взаимоотношений между людьми на судне.
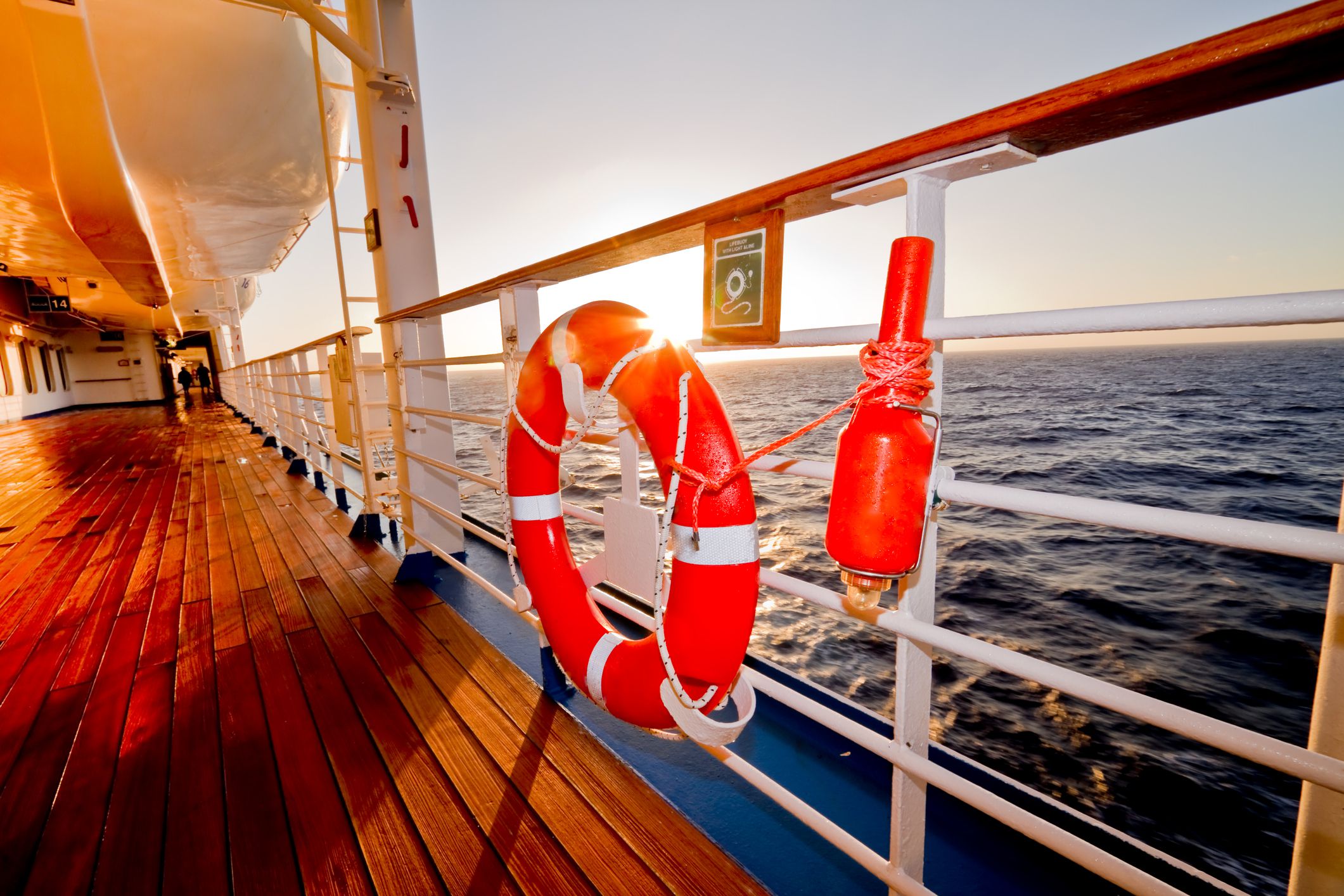
- Управляющий: Александров Вениамин Юрисович
Физика часть III. Оптика и атомная физика. Для студентов технических специальностей.
- Управляющий: Егоров Сергей Валентинович
В курсе рассматриваются вопросы, связанные с поиском, сбором, хранением, преобразованием и использованием информации в самых различных направлениях будущей профессиональной сферы деятельности. Решаются прикладные задачи на языке программирования Python
- Управляющий: Николаева Наталья Александровна
Электронное учебное пособие ознакомит курсантов с методикой выполнения научных исследований в современных условиях.
В пособии рассмотрены методические разработки по формулированию темы, цели и задач научного исследования; методология теоретического и экспериментального исследований; анализ теоретико-экспериментальных исследований и формулирование выводов и предложений.
Значительное внимание уделено внедрению и эффективности научных исследований, а также правилам оформления курсовых работ, дипломных проектов, научно-исследовательских статей и конкурсных работ, диссертаций на соискание ученых степеней.
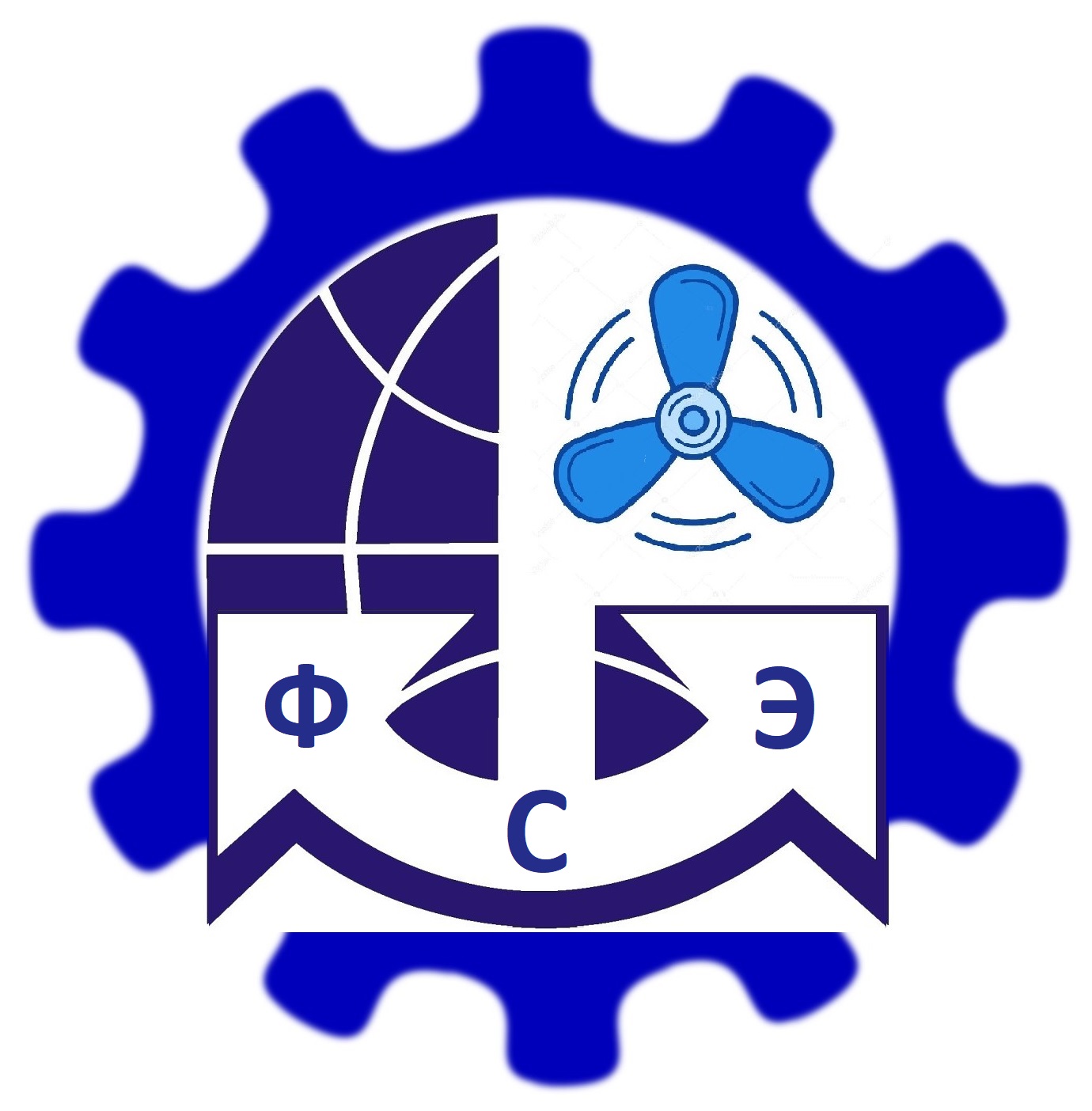
- Управляющий: Радаев Анатолий Вячеславович
- Управляющий: Клепикова Татьяна Альбертовна
- Преподаватель: Асамбаева Любовь Александровна
- Преподаватель: Быков Алексей Сергеевич
- Преподаватель: Виноградов Андрей Александрович
- Преподаватель: Крымова Татьяна
- Преподаватель: Малетин Евгений Андреевич
- Преподаватель: Паничкина Светлана Дмитриевна
- Преподаватель: Бабурина Ирина Михайловна
- Преподаватель: Володькина Наталья Алексеевна
- Преподаватель: Минаева Ирина Дмитриевна
Физика II. Электричество и магнетизм.
- Управляющий: Егоров Сергей Валентинович