51. Системы электронного управления двигателями фирм «Катерпиллар», «МАН-Дизель», «Вяртсиля-Зульцер».
Начало работ по
системам электронного управления двухтактных малооборотных двигателей
относится к 1991 году, в 2003 году были построены и установлены на танкерах
первые двигатели 7S-50МЕ-С и 6S70ME-C с электронным управлением.
Фирмой было прежде всего разработано и заложено в основу электронной системы
программное обеспечение.
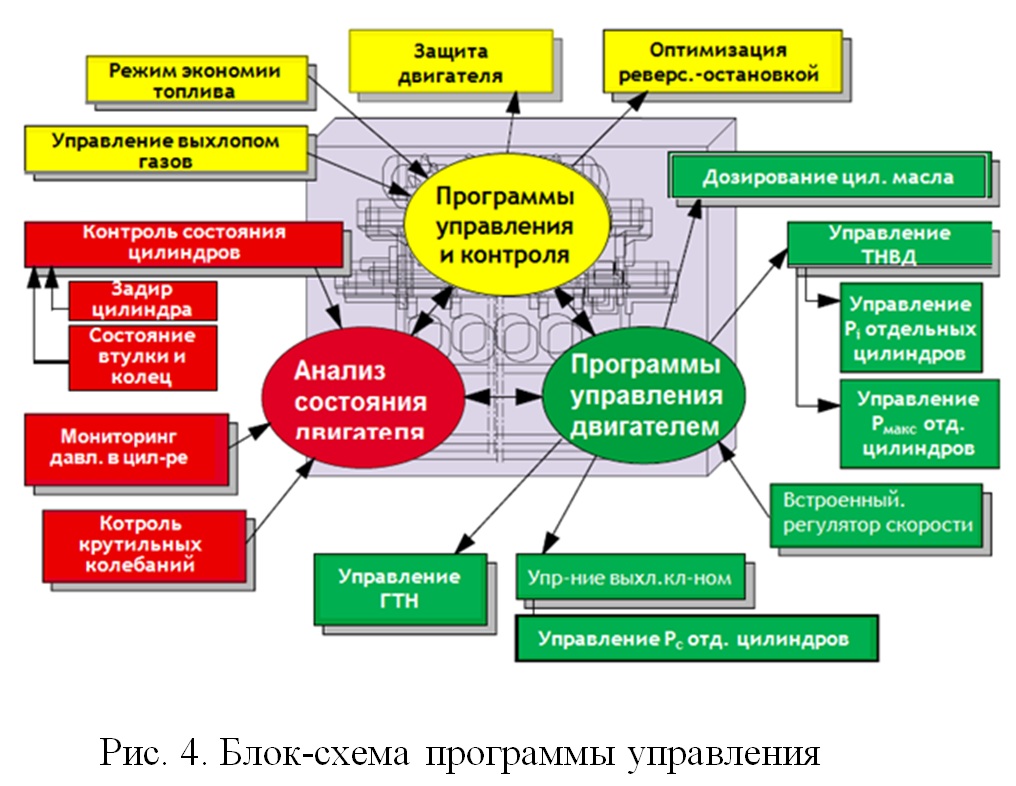
На Рис. 4 представлена блок-схема программ, включающих решение задач по анализу состояния двигателя и управлением топливоподачей, движением выхлопных клапанов, смазкой цилиндров и турбонаддувом.
Конфигурация системы управления, приведенная на Рис.5 включает панель управления на мостике, главную панель управления в посту управления, два микропроцессора (основной А и резервный В), в которые заложены программы управления, панель местного управления также с двумя электронными блоками А и В и модулями на каждом цилиндре.
Перевод мощных двигателей на
электронное управление потребовал не только поиска и разработки программ управления,
высоконадежных средств электроники, но и радикального решения по замене мощных
механических
приводов. Достаточно сказать, что привод топливного насоса в стандартном варианте испытывает весьма большие нагрузки, если учесть, что в мощной машине в цилиндр за цикл подается около 200 г. топлива, сжатого до 80-90 МПа. Высокие нагрузки приходятся и на привод выхлопных клапанов. Поэтому единственно верным решением было применить в качестве силовых передач гидропривод (МАН Дизель и Турбо), либо аккумуляторную систему топливоподачи, как это сделала фирма Зульцер. Схема системы топливоподачи с гидроприводом представлена на Рис.6. В число основных компонентов системы входят:
Самоочищающийся 10 микронный фильтр тонкой очистки маcла, необходимость в котором определяется более высокими требованиями к маслу, используемому в гидроприводе.
• Гидронасосы, использующие масло из общей системы смазки двигателя и поднимающие его давление до 17,5 МПа (электроприводные и применяемые при пуске двигателя) и до 25 МПа с приводом от двигателя, берущие на себя снабжение гидросистемы маслом во время его работы. Масло направляется в аккумулятор (Рис. 6), давление в котором поддерживается путем изменения производительности гидронасосов, находящейся под управлением электронных блоков. Из аккумулятора масло направляется к установленным на каждом рабочем цилиндре гидроцилиндрам-усилителям привода ТНВД и выхлопного клапана, включающим блок распределения с гидравлическими аккумуляторами и электронно управляемыми, пропорциональными, быстродействующими клапанами положения (NC) см. Рис.7. В задачу последних входит управление фазами и давлениями топливоподачи, фазами движения выхлопного клапана.
Электронное управление и гидропривод топливного насоса.
Топливный насос высокого давления
в сравнении с традиционными конструкциями механически значительно
проще. В нем отсутствуют механический привод плунжера, (заменен на гидропривод), механизм управления фазами подачи топлива, механизм VIT.
Плунжер представляет собой гладкий поршень без косых кромок, что существенно упрощает технологию его изготовления и повышает ресурс. Масло из аккумулятора через управляющий клапан, активизация которого осуществляется электронным блоком, попадает в полость над гидропоршнем. Воспринимаемое им усилие, будучи усиленным в 4,47 раза (отношение площадей Fгп / Fпл = 4,47), передается поршню-плунжеру топливного насоса, осуществляющему сжатие топлива до заданных процессором давлений в 50 - 100МПа и подачу его к форсункам.
Как уже отмечалось,
моменты поступления масла в цилиндр гидроусилителя, а,
следовательно, фазы и количественная характеристика подачи, задаются
микропроцессором, в свою очередь воздействующим на управляющий клапан. В
микропроцессор заложены программы, позволяющие изменять давление масла по ходу
процесса впрыска, тем самым менять характер кривой давлений впрыска и подбирать
необходимый для данного режима закон подачи топлива. Возможные варианты
приведены на Рис. 9. Рис. 10 иллюстрирует влияние характера
впрыска на развитие давлений в рабочем цилиндре. Здесь мы видим впрыск с резким ростом давлений в начальной стадии и последующим спадом давления и, сопровождаемым уменьшением скорости впрыска топлива (поз.А). Такой вариант, равно как и последующий (поз.В), приведет к резкому росту тепловыделения в цилиндре в начальной стадии сгорания и большим Рмакс. В итоге - будет достигнута высокая экономичность, но и большие тепловые и механические нагрузки на ЦПГ. Более мягкая организация подачи в ее начале и резкое окончание в конце (поз. С) позволяет уменьшить нагрузки, но в ущерб экономичности двигателя. В то же время, улучшается распыливание топлива в конце подачи, а, следовательно, достигается меньшее догорание на линии расширения. Мягкое сгорание в начальной стадии и меньшие температуры рабочего цикла достигаются при двухфазном впрыске (поз.D). К этому варианту прибегают, когда стоит задача уменьшения содержания в выхлопных газах NOx.
Электронное управление и гидропривод выхлопного клапана
Система привода включает
цилиндр-актюатор, заполняемый маслом высокого давления из аккумулятора через
управляющий клапан, активируемый электрическим сигналом, поступающим из
электронного блока (Рис. 7).
Перечисленные элементы практически выполняют функции традиционной системы механического привода клапана, состоявшей из распределительного вала с кулачком, толкателя и коромысла. В рассматриваемой системе гидропривода управляющий клапан по получении эл. сигнала от электронного блока в необходимый момент открывает доступ гидромасла высокого давления к поршню сервопривода (см. Рис. 11), который, двигаясь вниз, открывает клапан. Закрытие клапана происходит после перемещения управляющего клапана в положение, при котором полость актюатора разгружается от давления масла. Соответственно полость гидроусилителя также разгружается и воздушная пружина поднимает клапан в положение “закрыто”. В конструкции сервоприводов предусмотрены демпферы, смягчающие удары при открытии и закрытии клапана. Контроль за перемещениями клапана осуществляет установленный на корпусе датчик, реагирующий на изменение расстояния между ним и напрессованным на шток клапана измерительным конусом.
Важно отметить, что предоставленная электроникой возможность изменения фаз открытия и закрытия клапана позволяет их оптимизировать в соответствии с режимом работы двигателя.
Электронное управление лубрикатором.
Использование в системе
управления двигателем микропроцессоров позволило решить давно назревшую
проблему организации смазки цилиндров. В традиционной системе, где используется механический привод лубрикаторов,
ряд фирм для уменьшения подачи масла на смазку цилиндров при снижении
нагрузочного режима связывали механизм подачи с положением рейки топливных
насосов. Но, к сожалению, не могли достигнуть синхронизации подачи с движением
поршня рабочего цилиндра, а это приводило к тому, что часть поступающего из
штуцеров масла попадала в цилиндр над поршнем, и при его движении вверх
поршневыми кольцами перемещалось в направлении камеры сгорания, где выгорало.
Часть масла выходила из штуцеров цилиндра под поршень и при его движении вниз
кольцами забрасывалось в продувочные и выхлопные окна. Идеальной считается
подача в момент, когда масло выходит из штуцера в промежуток между первым и
вторым поршневыми кольцами. Тогда масло хорошо разносится по поверхности
цилиндра и ранее отмеченные потери исключаются. В современной системе эта задача
успешно решается и экономия в расходе цилиндрового масла в двигателях ME составляет свыше 0,3 г/кВт·час. Концепция новой
системы смазки цилиндров с электронным управлением представлена на Рис. 12.
Масло из цистерны цилиндрового масла поступает в насосную станцию, где его
давление поднимается до 4,5 МПа и направляется в индивидуальные для каждого
цилиндра аккумуляторы и далее в лубрикаторы. В станции находятся два рабочих
насоса и один, автоматически включаемый в режиме stand-by. Количество лубрикаторов (1 или 2) на каждом цилиндре
зависит от размеров цилиндра (количества штуцеров).
Лубрикатор
(см. Рис. 13) снабжен поршнем гидроусилителя, подача масла на который
осуществляется через быстродействующий двухпозиционный клапан, управляемый
микропроцессором. Поршень приводит в движение размещенные по окружности плунжеры
насосов высокого давления, обеспечивающие подачу одинаковых количеств масла по
всем точкам смазки и, практически, в один момент времени. Количество плунжеров
соответствует числу точек смазки. Лубрикатор подает масло через каждые в 4-5
или более оборотов коленчатого вала в зависимости от
требуемой величины подачи, выраженной в г\кВт·час. Увеличение подачи
достигается увеличением частоты подач, уменьшение - наоборот. Время впрыска
(момент подачи) задается микропроцессором с большой точностью с тем, чтобы
поступление масла в цилиндр происходило в период, когда поршень своим
комплектом колец находится в плоскости штуцера. Продолжительность подачи
укладывается в ~0,1°п.к.в. Величина создаваемого плунжерами давления в
нормальных условиях составляет 4,5 МПа, при закоксовывании отверстий может
существенно увеличиваться, что обеспечивает гарантированную подачу.